DOZAMEL
CASE-ONDERZOEK
Lees meer over de thermische modernisering van de gevel en het dak van een industrieel gebouw.
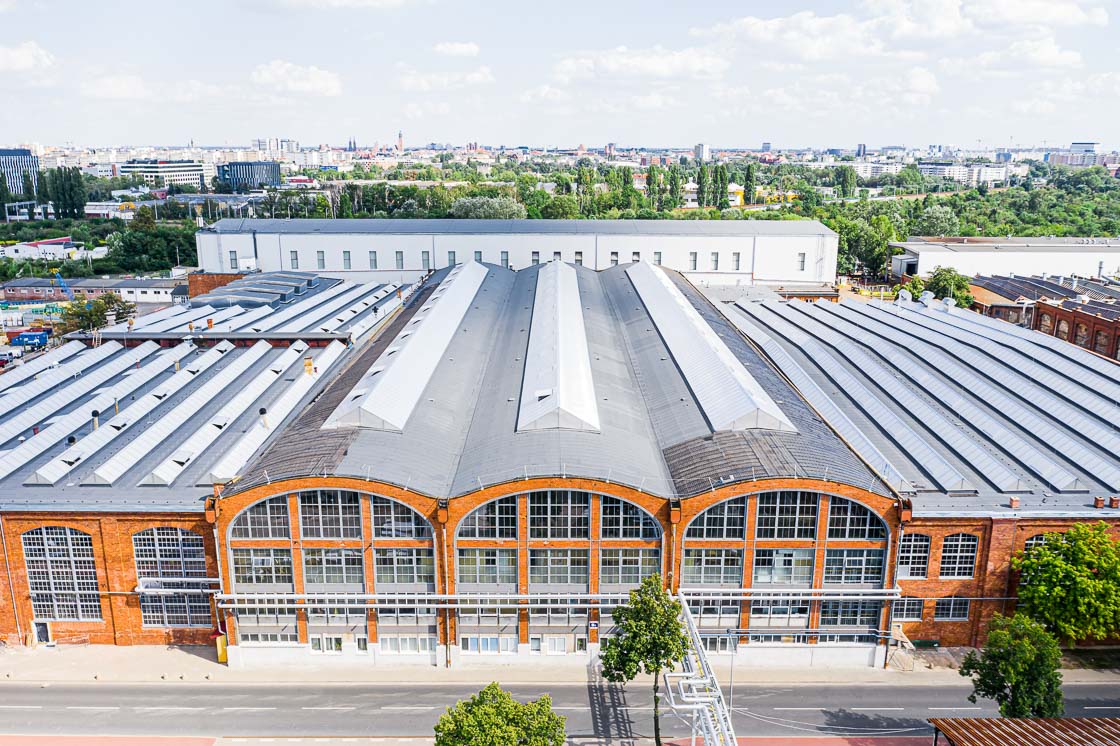
In 2020 hebben we een van onze meest complexe en veeleisende projecten met succes afgerond. Het was ongetwijfeld een van de belangrijkste uitdagingen die Aluco System tot nu toe is aangegaan. Gezien onze aanwezigheid in de industrie sinds 1997 is er weinig dat ons nog verrast.
Het project omvatte de uitgebreide thermische modernisering van een productiegebouw in Wrocław, in een van de oudste industrieparken van Polen. Het project werd uitgevoerd voor OZBUD uit Wrocław, als EPC-aannemer. Het gebouw had een historische betekenis, wat de belangrijkste reden was voor de complexiteit van het project.
In dit artikel geven we u graag wat inzicht in de uitvoering van het project, waarbij we de belangrijkste aspecten behandelen.
Een korte geschiedenis van het Wrocław Industrial Park
De geschiedenis van het Wrocław Industrial Park (WPP) gaat terug tot de 19e eeuw, met de fabrieken Linke-Hofmann Werke en Fahrzeug und Motoren Werke, afgekort als “Famo”, als belangrijke initiatiefnemers van de ontwikkeling in het gebied. Aanvankelijk produceerden ze locomotieven en elektrische machines. Tijdens de tussenoorlogse periode veranderde de locatie in een fabriek voor wapenproductie, waar gevangenen uit het concentratiekamp Gross-Rosen bij betrokken waren.
Na de Tweede Wereldoorlog werd de locatie, ondanks de grote schade, snel herbouwd. De fabriek richtte zich op de productie van elektromotoren en generatoren. In 2003 vatte DOZAMEL het idee op om het DOLMEL Industrial Park op te richten op een terrein van 34 hectare om bedrijven aan te trekken en EU-fondsen te gebruiken voor de revitalisering van de bestaande infrastructuur.
Door een wijziging van een relevante wet in 2003 werd het echter noodzakelijk om een overeenkomst met het lokale zelfbestuur te ondertekenen om EU-financiering te verkrijgen. Pas in 2005 werd de overeenkomst eindelijk getekend en werd het Wrocław Industrial Park opgericht. Het 163 hectare grote gebied werd een verenigd industrieel centrum, waarbij de stad Wrocław, DOZAMEL, Archimedes S.A., Wrocławski Park Technologiczny S.A., Bombardier Transportation Polska Sp. z o.o. en Wojdyła Inwestycje Sp. z o.o. als partners samenwerkten.
De oprichting van het Wrocław Industrial Park was een antwoord op de strategie om de industriële gebieden van de stad nieuw leven in te blazen. Het gebied, met zijn unieke industriële tradities en historisch erfgoed, werd opgenomen in het historisch register. Het ontwikkelingsplan, opgesteld door DOZAMEL Sp. z o.o., schetste een geavanceerde renovatie van de industriële infrastructuur.
Beschrijving van het project
DEEL I
Het project richtte zich op het B1-gebouw in het Wrocław Industrial Park. Het B1-gebouw is het grootste gebouw binnen het complex. De geschiedenis gaat terug tot de 20e eeuw toen het Duitse bedrijf Linke-Hofmann-Werke AG op deze locatie locomotieven produceerde. Het is een 10-verdiepingen productiegebouw met opslag-, kantoor- en personeelsfaciliteiten, met een nuttig vloeroppervlak van ongeveer 26.000 m². De gevel is opgetrokken uit gevelstenen en bevat veel grote beglazing.
PROJECTDOELSTELLING:
Uitgebreide thermische modernisering van het B1-gebouw
Onze taak was het uitvoeren van een thermische modernisering van het B1-gebouw. Het project omvatte de vervanging van alle dakramen en de gevel van het gebouw. Al deze taken moesten worden uitgevoerd zonder de lopende werkzaamheden in het gebouw te verstoren. Het was een uitdagende opdracht die veel creativiteit, zorgvuldige planning en uitgebreide ervaring vergde.
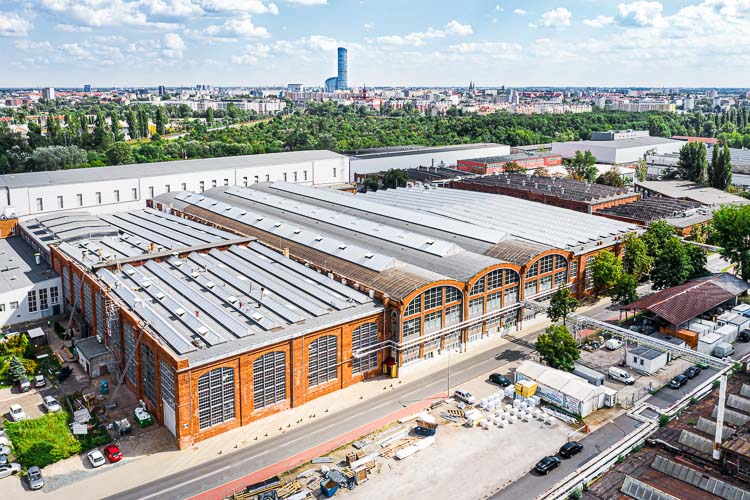
Fase I
In de eerste fase werden de polygoon dakramen over het hele dak vervangen, zowel de smallere dakramen in de eindvleugels als de bredere dakramen in de drie centrale vleugels van de constructie. Het behoud van de polygoon vorm van de dakramen was essentieel; kiezen voor doorlopende dakramen, een populaire en voordelige keuze, was in dit geval geen haalbare optie.
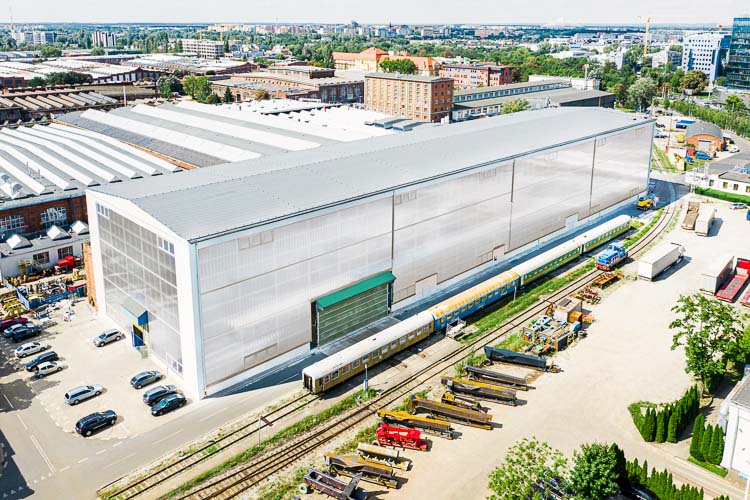
Fase II
De tweede fase bestond uit het upgraden van de gevel van een van de gebouwen in het complex. We installeerden een licht doorlatende polycarbonaat gevel met behulp van ons beproefde systeem.
De grootste uitdaging
We willen benadrukken dat de thermische modernisering van dit gebouw een uitdagend project was dat ons voor de volgende uitdagingen stelde:
- Groot oppervlak aan dakramen en gevels: We vervingen in totaal 6.860 m² dakramen en installeerden 5.000 m² polycarbonaat panelen.
- Logistiek: Het verwerken van zulke grote hoeveelheden materialen vereiste talrijke systematische leveringen, die nog werden bemoeilijkt door de aanzienlijke afstand tussen Wrocław en Kielce – het hoofdkantoor van ons bedrijf.
- Continuïteit van de productie: Alle dakwerkzaamheden moesten worden uitgevoerd zonder de productieprocessen in de fabriek te onderbreken. Daarom moesten de dakopeningen 100% veilig zijn.
- Behoud van erfgoed: Het B1-gebouw is, net als vele andere in het industriepark van Wrocław, een erfgoedstructuur die voortdurend wordt beschermd als historische locatie. Daarom moesten onze dakramen niet alleen voldoen aan alle toepasselijke technische vereisten, maar mochten ze ook het architecturale concept van het gebouw niet verstoren. Gelukkig was ons Aluco-dakraamsysteem perfect ontworpen om aan deze vereiste te voldoen, zoals verder in dit artikel zal worden besproken.
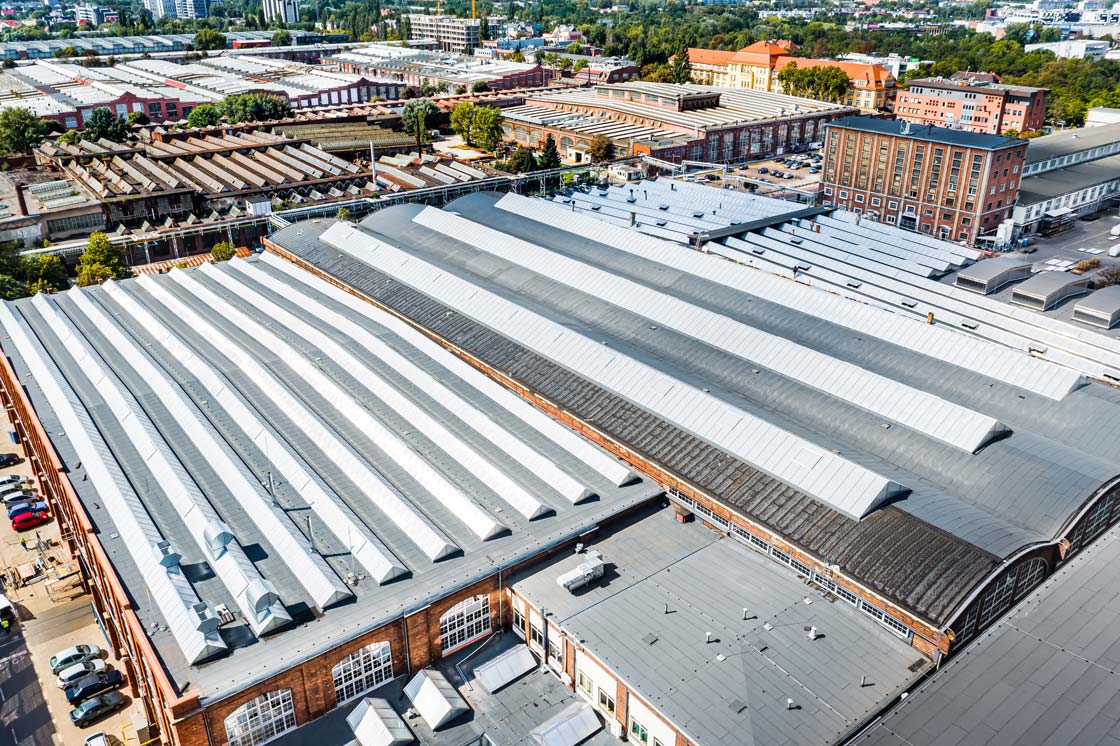
Toegepaste oplossingen
We hebben het project uitgevoerd met onze eigen systemen, namelijk Aluco Skylight polygoon dakramen en ventilatieopeningen, en Aluco Panel polycarbonaat gevels.
ALUCO SKYLIGHT TR THERM
Thermisch geïsoleerde polygoon dakramen
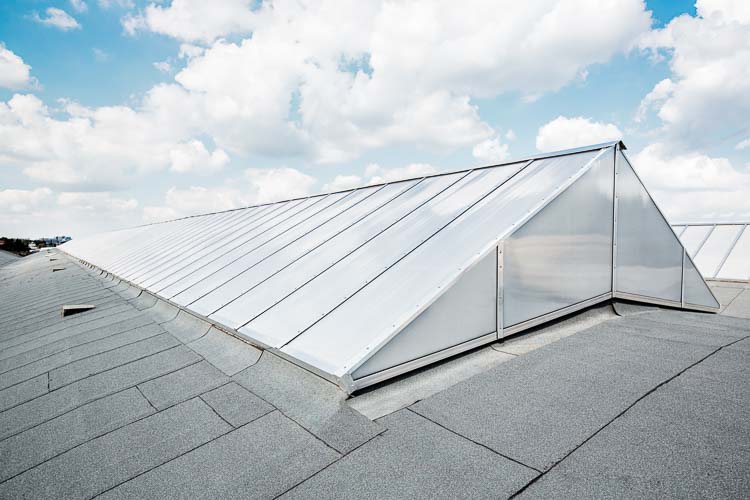
ALUCO PANEL
Polycarbonaat gevels met optionele ventilatieramen
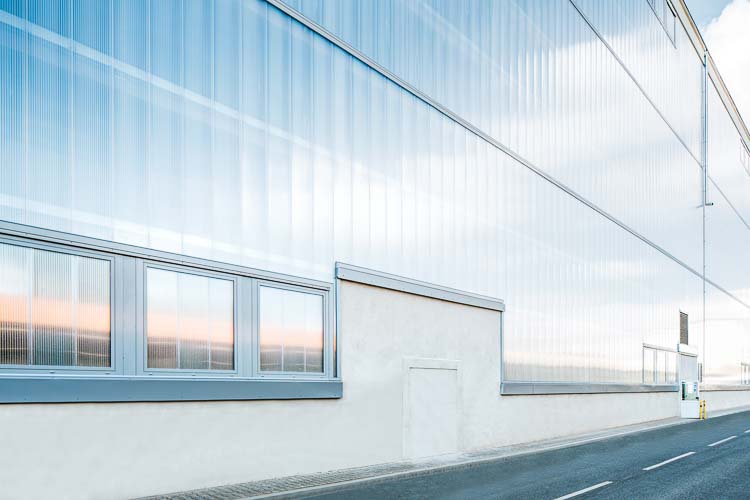
ALUCO SKYLIGHT AIR TR
Industriële ventilatieopeningen speciaal voor polygoon dakramen
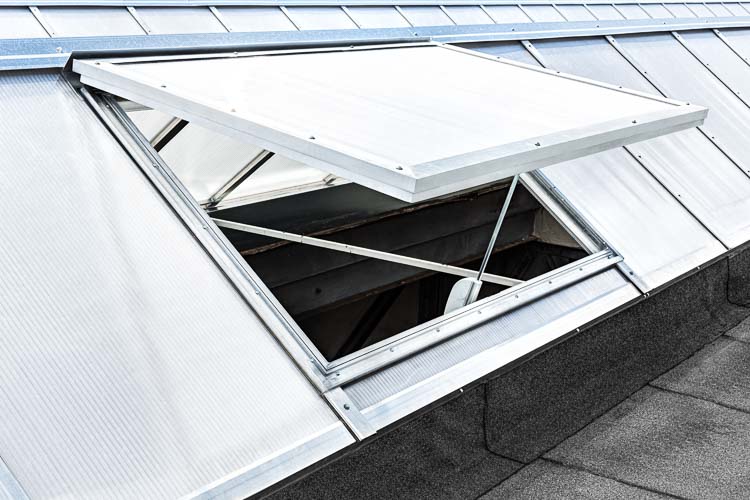
Uitgangstoestand
Zeggen dat de bestaande dakramen “aan vervanging toe waren” was niet eens genoeg om de situatie te beschrijven. De foto hieronder laat zien dat het bestaande dakraam dringend aan reparatie toe was. Het was het oorspronkelijke dakraam die werd geïnstalleerd tijdens de bouw van het gebouw aan het begin van de 20e eeuw, wat aangeeft dat hij zeker meer dan 100 jaar oud was op het moment van vervanging.
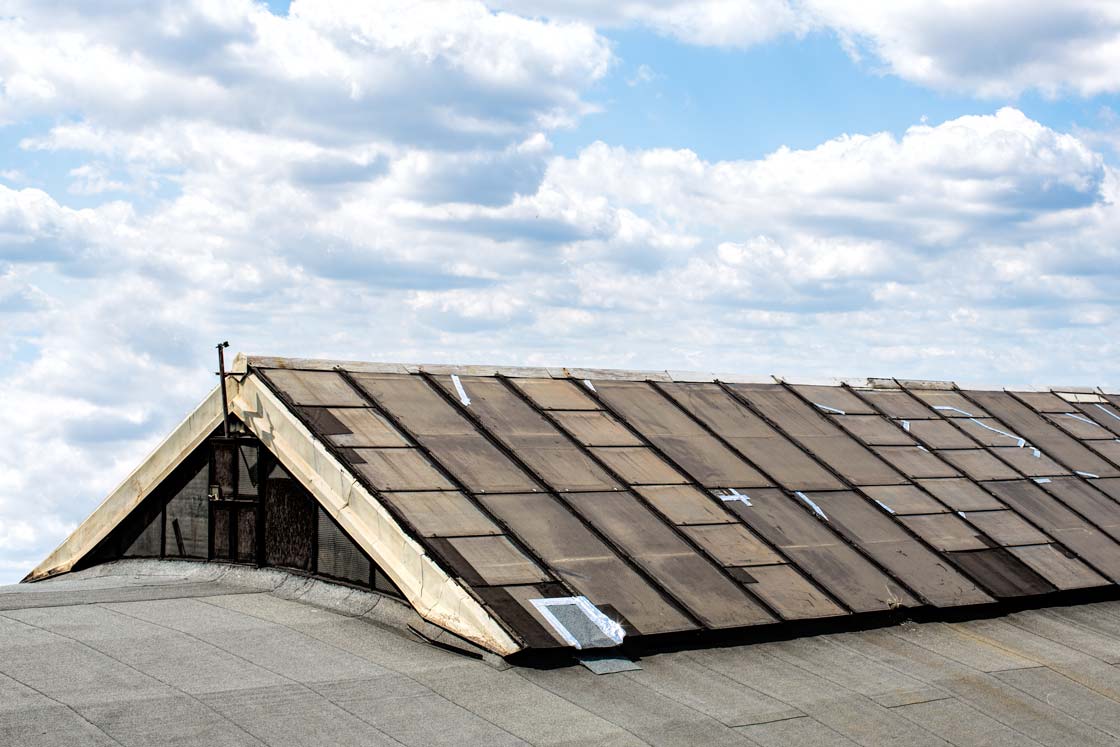
De dakramen die we op het dak aantroffen waren gemaakt van dik draadglas, gebarsten en op veel plaatsen opgelapt. Ondanks het gebrek aan thermische isolatie liet het glas heel weinig licht door. Het gevolg was dat het interieur van het gebouw ernstig onderbelicht was. Hierdoor ontstond een ongunstige situatie die het werkklimaat in het gebouw negatief beïnvloedde. De gevelramen van het gebouw waaraan we moesten werken, verkeerden in een vergelijkbare toestand.
Aluco System Solutions bracht hier al snel verandering in!
Dozamel Case Study
Download PDF
Download de volledige versie van het artikel "Dozamel Case Study" als PDF-bestand naar uw apparaat. Tekst in het Engels.
Uitvoering van het project
Deel II
Laten we het doel van het hele project nog eens herhalen: “Alomvattende thermische modernisering van dakramen en gevel van gebouw B1”, met de nadruk op de term “alomvattend”. In ons bedrijf betekent alomvattende implementatie van een project het minimaliseren van de betrokkenheid van de klant of projecteigenaar bij de coördinatie van het project. Aluco System neemt de verantwoordelijkheid voor het organiseren en uitvoeren van zoveel mogelijk taken, die verder gaan dan de taken die direct verband houden met de installatie van onze producten..
Dat was onze benadering van dit project. In de praktijk betekende dit dat ons bedrijf de verantwoordelijkheid nam voor de demontage en verwijdering van bestaande dakramen en geveldelen, de bescherming van het werkterrein en de installatie van nieuwe dakramen en gevels. Als de klant dat wilde, konden we ook dakreparaties uitvoeren.
Om al deze taken uit te voeren, ondernamen we de volgende stappen:
- Materiaal logistiek
- Bestaande dakramen demonteren en de gevel voorbereiden
- Het dak beschermen om onderbrekingen in de productieprocessen in het gebouw te voorkomen
- Fase I – installatie van nieuwe dakramen
- Fase II – installatie van een nieuwe polycarbonaat geve
- Verwijdering en afvoer van afval
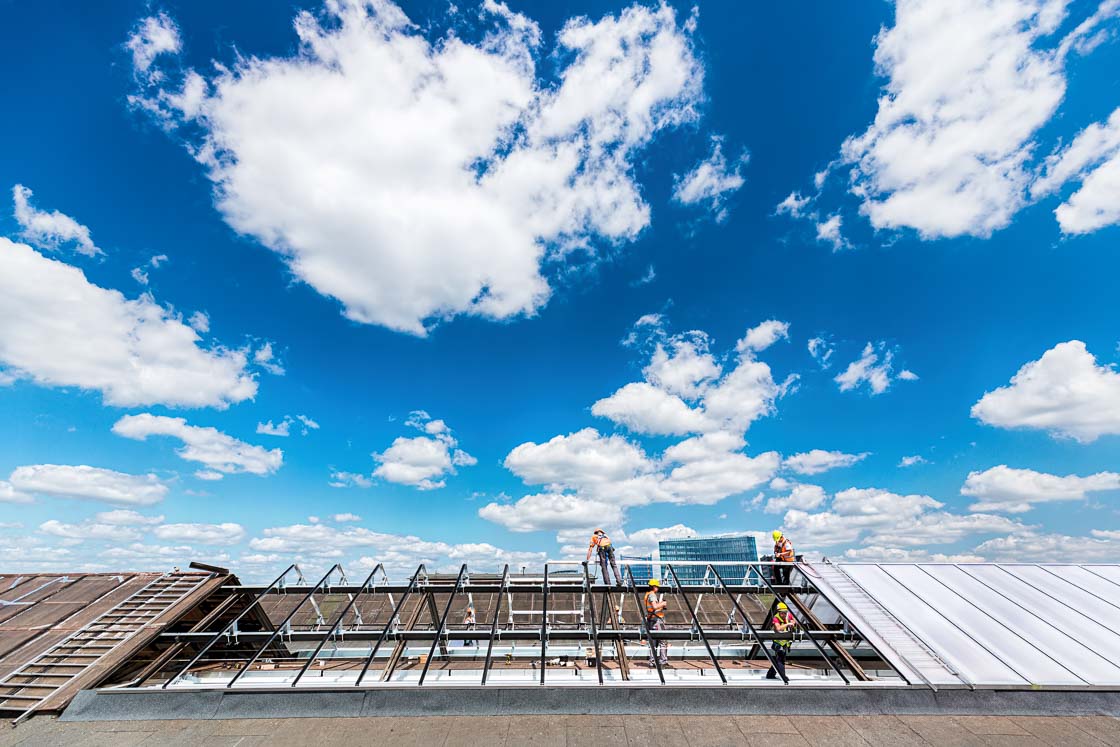
Materiaal logistiek
Om deze uitdaging aan te gaan, moesten we alle details met betrekking tot materiaalleveringen zorgvuldig overwegen en nauwkeurig regelen. Door een voldoende hoge voorraad aan te houden van tussenproducten – in dit geval aluminium profielen – konden we de leveringsdata van afgewerkte dakraamconstructies voor de afzonderlijke fasen aanpassen aan de data die in het contract waren vastgelegd.
De polycarbonaatpanelen die als beglazing voor de dakramen werden gebruikt, werden geleverd door een fabriek in Tsjechië. Het contract bepaalde de levering van kant-en-klare polycarbonaatpanelen, op maat gesneden en omwikkeld met afdichtband. Dankzij deze regeling en de korte afstand tussen de productiefabriek en de projectlocatie in Wrocław konden we niet alleen extra besparen, maar ook alle onderdelen op tijd op de locatie leveren.
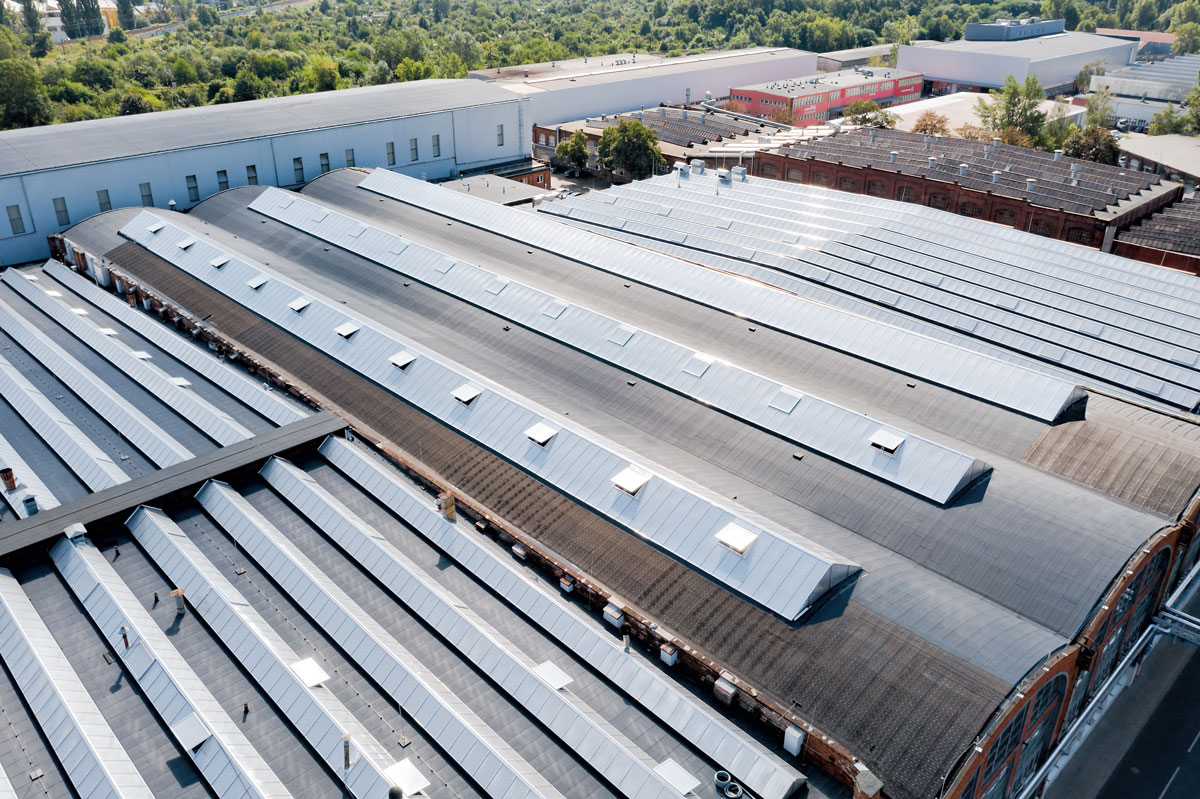
Demontage van bestaande dakramen
We begonnen met de ontmanteling van bestaande dakramen door routes vast te stellen voor de horizontale verplaatsing van de gedemonteerde materialen. OSB’s werden langs de dakramen gelegd om het gedemonteerde glas en de staalstructuur te vervoeren. De volgende stap bestond uit het reinigen van de resterende staalstructuur en het beschermen tegen corrosie. Tijdens deze werkzaamheden werden de oppervlakken onder de dakramen op de juiste manier afgeschermd om te voorkomen dat het installatiepersoneel of de gedemonteerde onderdelen zouden vallen.
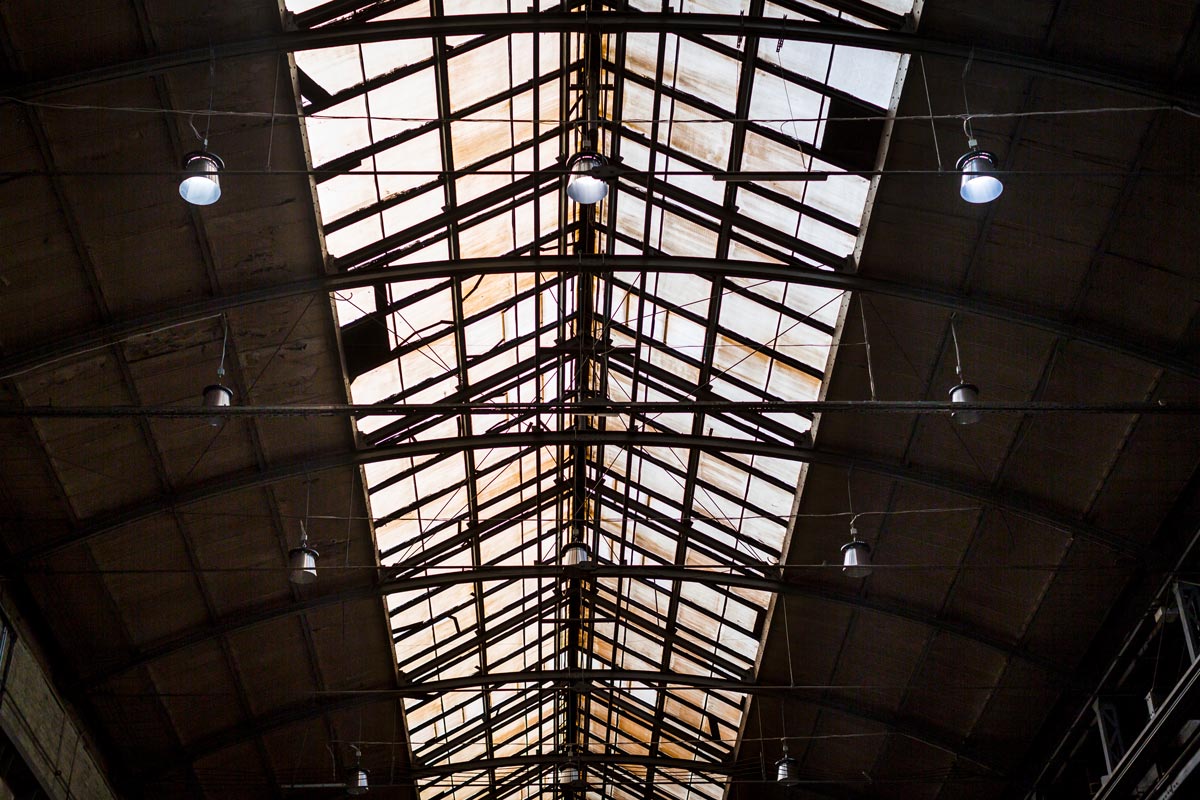
Veiligheid
De bescherming van het werkterrein was een van de belangrijkste uitdagingen van dit project, vooral vanwege de grote oppervlakte van het gebouw en de noodzaak om de dakopeningen te beveiligen zonder de lopende werkzaamheden in het gebouw te verstoren. Bij Aluco System geven we prioriteit aan veiligheid en houden we ons strikt aan de toepasselijke voorschriften voor gezondheid en veiligheid op het werk.
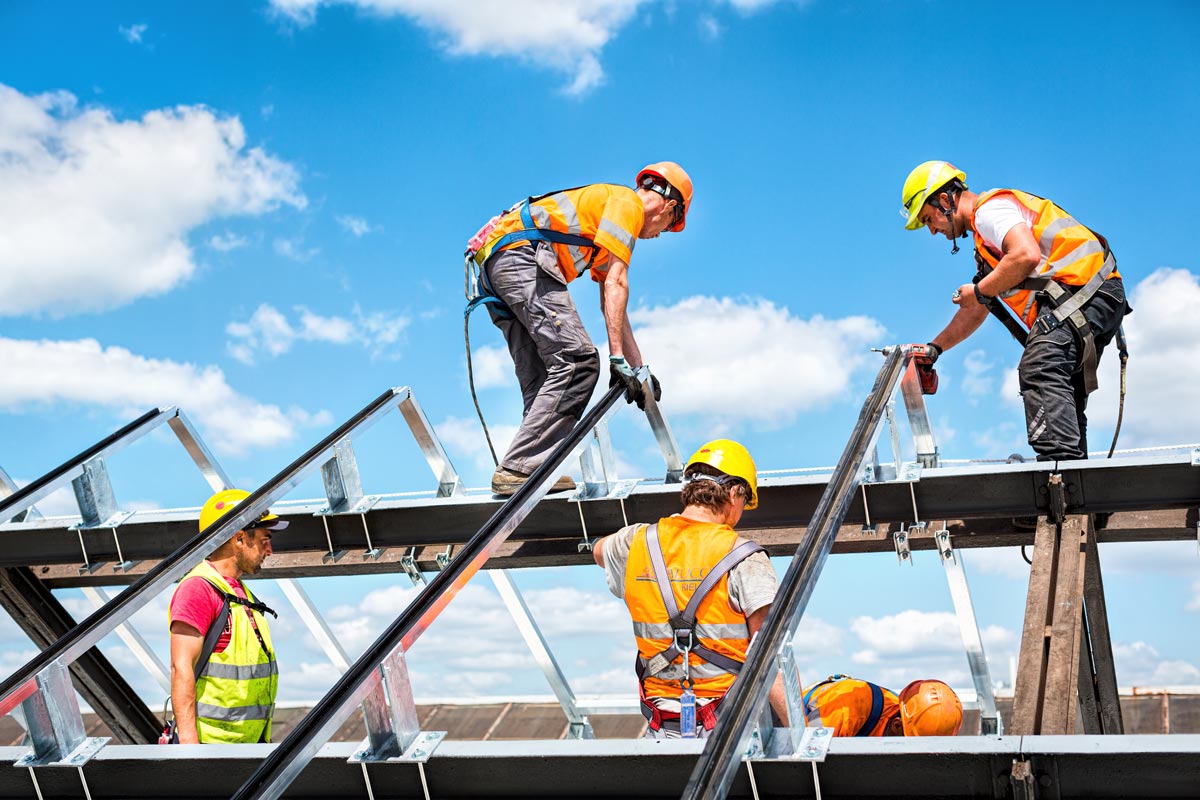
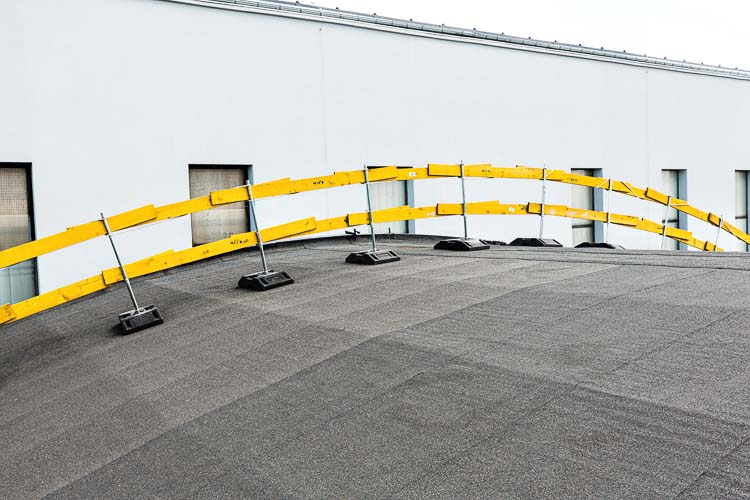
Werken op hoogte
Het werkgebied op het dak, waar afzonderlijke demontage- en installatiewerkzaamheden werden uitgevoerd, werd afgesloten en beveiligd met leuningen die we op de projectlocatie leverden. Onze werknemers gebruiken veiligheidsharnassen bij het werken op hoogte. Bovendien beschermden we alle dakopeningen tijdens de installatie van nieuwe dakramen. Deze maatregel garandeerde de veiligheid van het personeel op het dak en elimineerde het risico dat gereedschap, onderdelen en kleine voorwerpen per ongeluk in het gebouw zouden vallen.
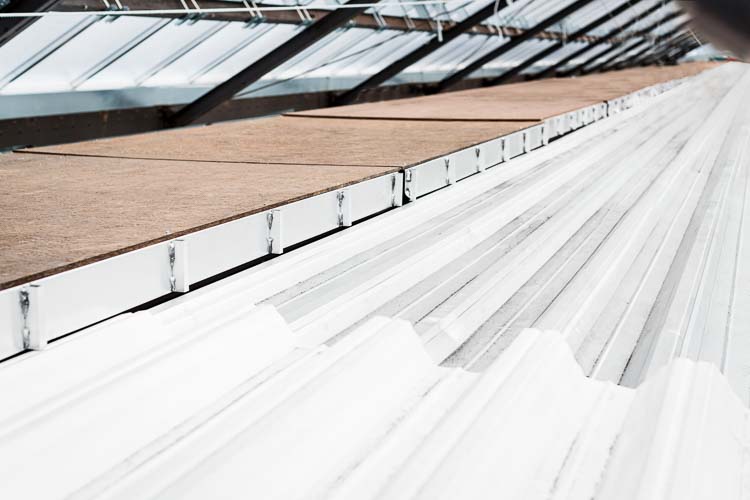
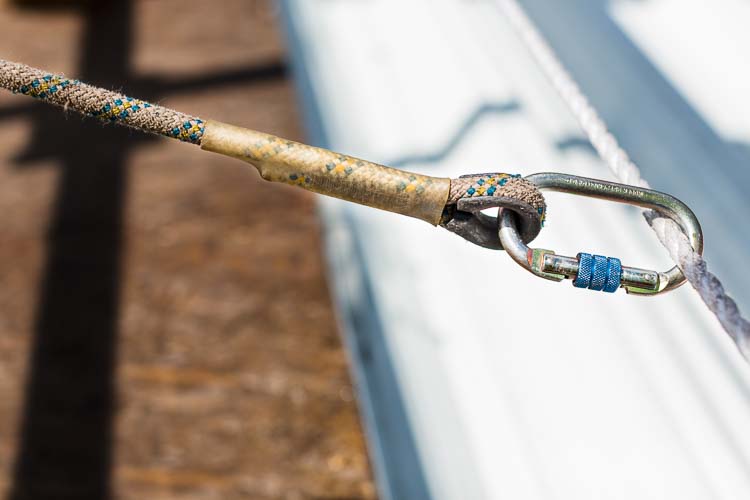
Bescherming van het hoofddakraam
Om de veiligheid van de installatiewerkzaamheden te garanderen, was de belangrijkste uitdaging hoe we de drie grootste dakopeningen in de centrale vleugels van het hoofdgedeelte van het B1-gebouw konden beschermen. Aangezien het dakraam 8,00 m lang is, was het nodig om over de hele lengte een extra ondersteuningsstructuur te installeren om de installatie van trogplaten en OSB’s te vergemakkelijken en de oppervlakken onder het dakraam te beschermen. Dankzij zo’n goed doordachte structuur konden we ook snel en veilig over het hele oppervlak van de dakopening bewegen. De taak werd verder bemoeilijkt door de lengte van het dakraam van 80 meter en de eis om de hele dakopening vast te zetten voordat de volgende fase van de werkzaamheden begon.
Geen onderbrekingen in de productie
Het was van essentieel belang om de dakopeningen tijdens de hele duur van de thermische moderniseringswerkzaamheden zorgvuldig te beschermen, in overeenstemming met een extra voorwaarde die door de eigenaar van het project werd opgelegd. Alle activiteiten moesten worden uitgevoerd zonder de productieprocessen in het gebouw te verstoren. Hoewel het een uitdaging was om aan deze eis te voldoen, was deze volledig gerechtvaardigd. In een faciliteit die zich bezighoudt met geavanceerde industriële productie kan elke vertraging, zelfs van een dag of een uur, leiden tot financiële verliezen, contractuele sancties, enz. We voldeden met succes aan deze voorwaarde, met als enige merkbare impact de beperking van de daglichttoetreding tijdens onze installatiewerkzaamheden.
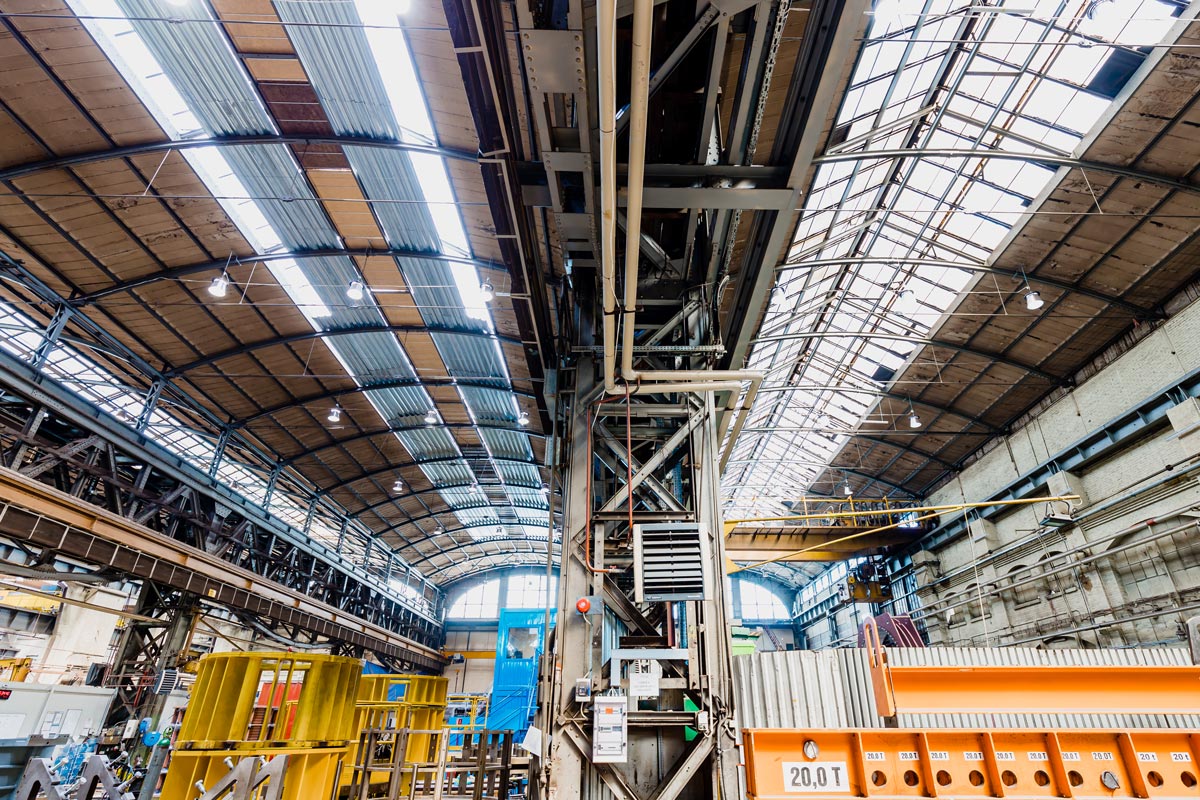
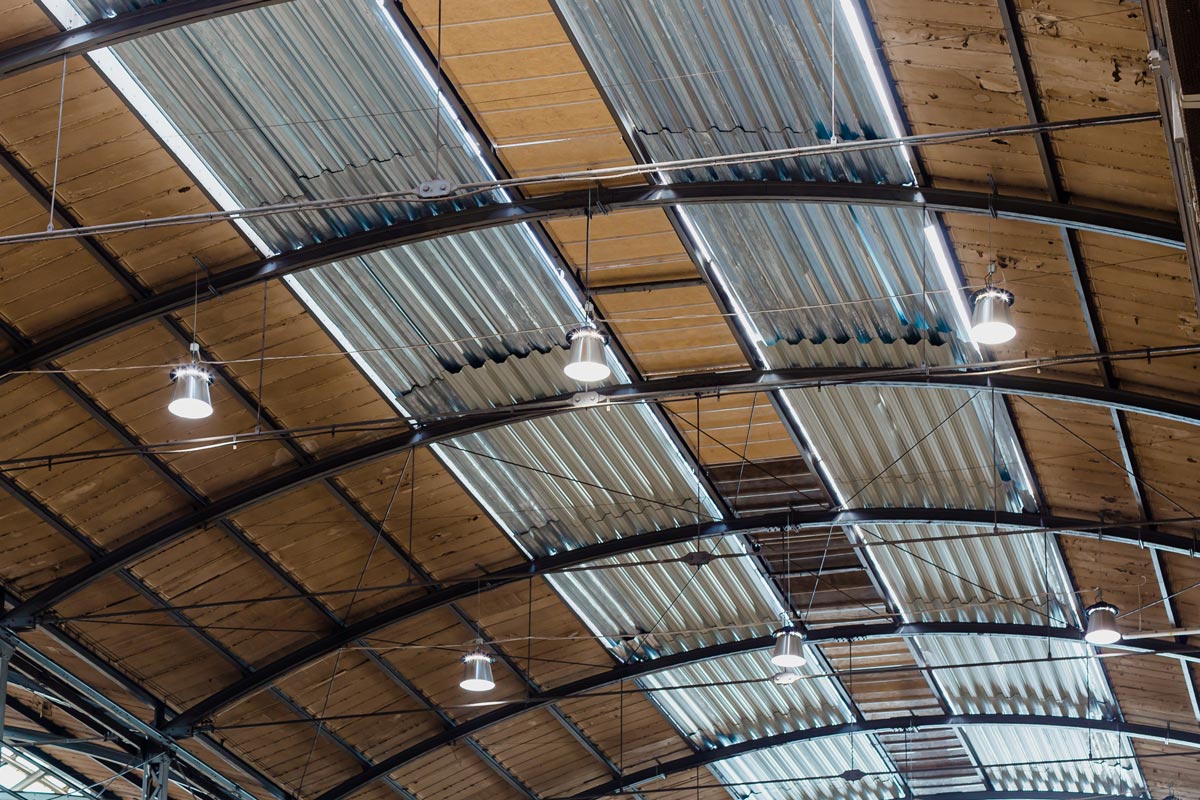
Implementatie van Fase I
THERMISCHE MODERNISERING VAN DAKRAMEN
De eerste fase van het project bestond uit het vervangen van de dakramen in het hele gebouw. Het gebouw heeft een oppervlakte van 26.000 m² en alle dakramen moesten worden vernieuwd. De onderstaande illustratie geeft een levendig beeld van de aanzienlijke hoeveelheid werk die we moesten verzetten. Volgens het principe “er is maar één manier om een olifant op te eten: hapje voor hapje”, verdeelden we de hele eerste fase in drie delen. We verbeterden achtereenvolgens de dakramen aan beide uiteinden van het gebouw en lieten de drie grootste dakramen in de centrale vleugels van het gebouw over voor de laatste fase.
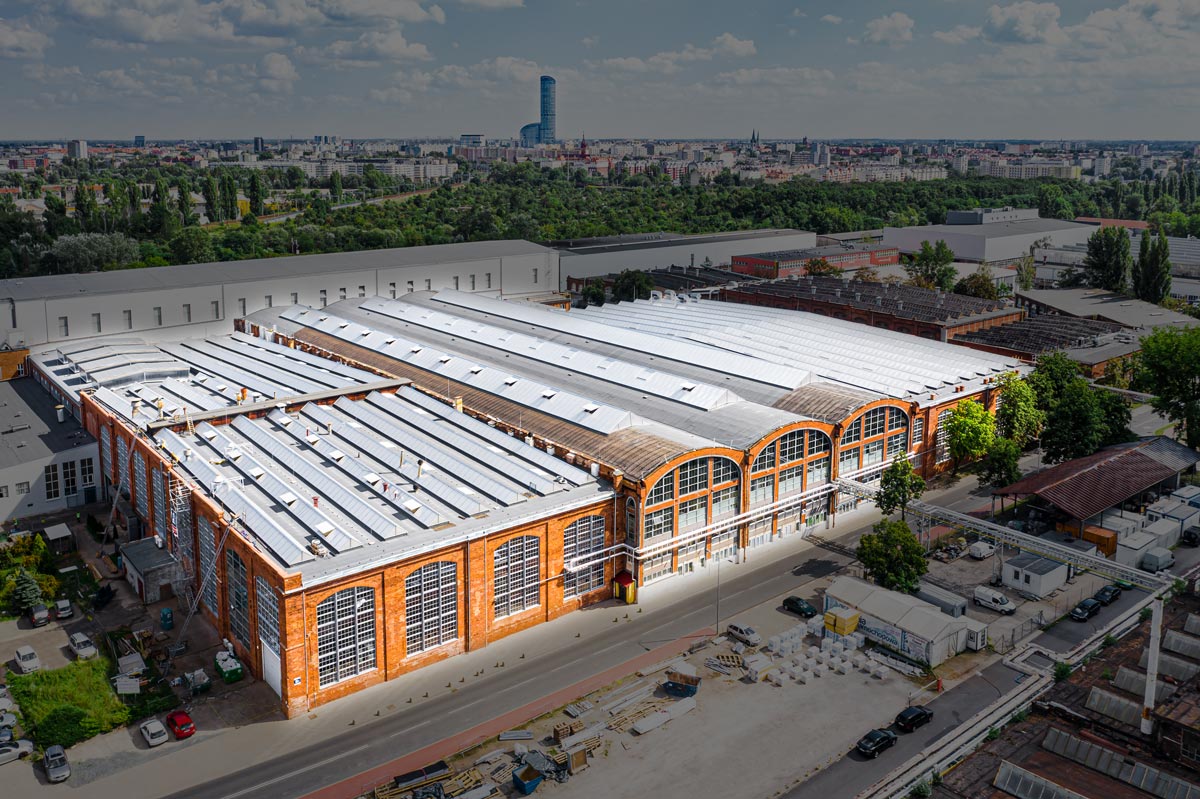
Alle dakramen op het dak van het B1-gebouw hebben de vorm van doorlopende polygoon dakramen. Er moet worden opgemerkt dat de hele B1-structuur al vele jaren beschermd is als erfgoedlocatie. Een van de eisen van het project was dan ook om de architectonische vorm van het dakraam te behouden, inclusief de oorspronkelijke vorm. Bij Aluco System hebben we een product dat speciaal ontworpen is voor dergelijke situaties – de Aluco Skylight TR Therm thermisch geïsoleerde dakraam.
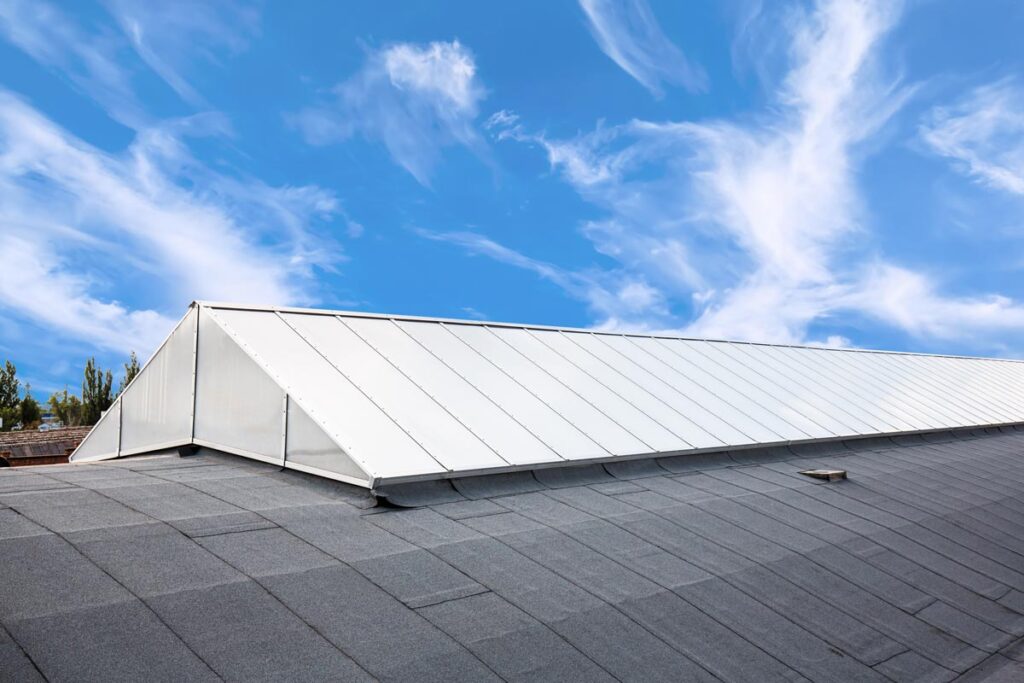
ALUCO SKYLIGHT TR THERM
POLYGOON DAKRAMEN MET THERMISCHE ISOLATIE
Het polygoon dakraamsysteem ALUCO SKYLIGHT TR THERM is een innovatieve oplossing die ontworpen is voor industriële gebouwen met erfgoed, waarbij het historische karakter behouden blijft dankzij de polygoon vorm. Het biedt thermische isolatie om energie te besparen. Het systeem voldoet aan de Europese normen en heeft een zeer lage warmteoverdrachtscoëfficiënt van U = 0,5 W/(m²K).
Afmetingen dakraam
Het ALUCO SKYLIGHT TR THERM doorlopende polygoon dakraam wordt vervaardigd volgens aangepaste afmetingen, waarbij de breedte (overspanning) van ons product varieert van 1.000 mm tot 4.000 mm. Bovendien kunnen we door het gebruik van een stalen draagstructuur industriële dakramen maken met een overspanning tot 14 meter.
In het besproken project fabriceerden we doorlopende dakramen met een breedte van 8.000 mm voor de smallere dakramen in de eindtraveeën en drie doorlopende dakramen met een breedte van 3.000 mm in de hoofdvleugels van het gebouw.
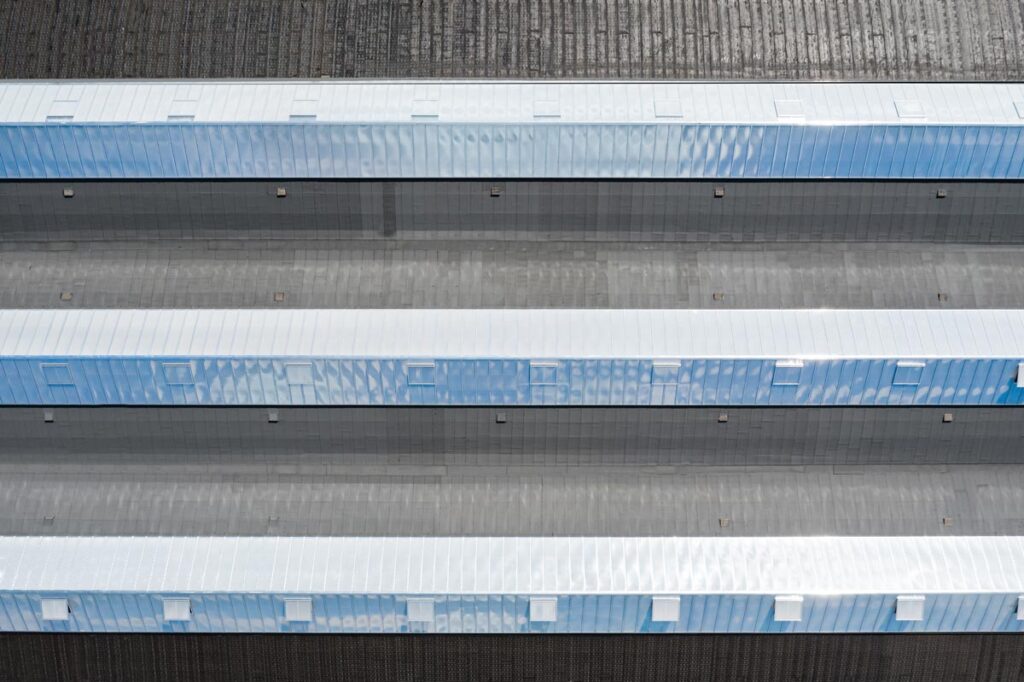
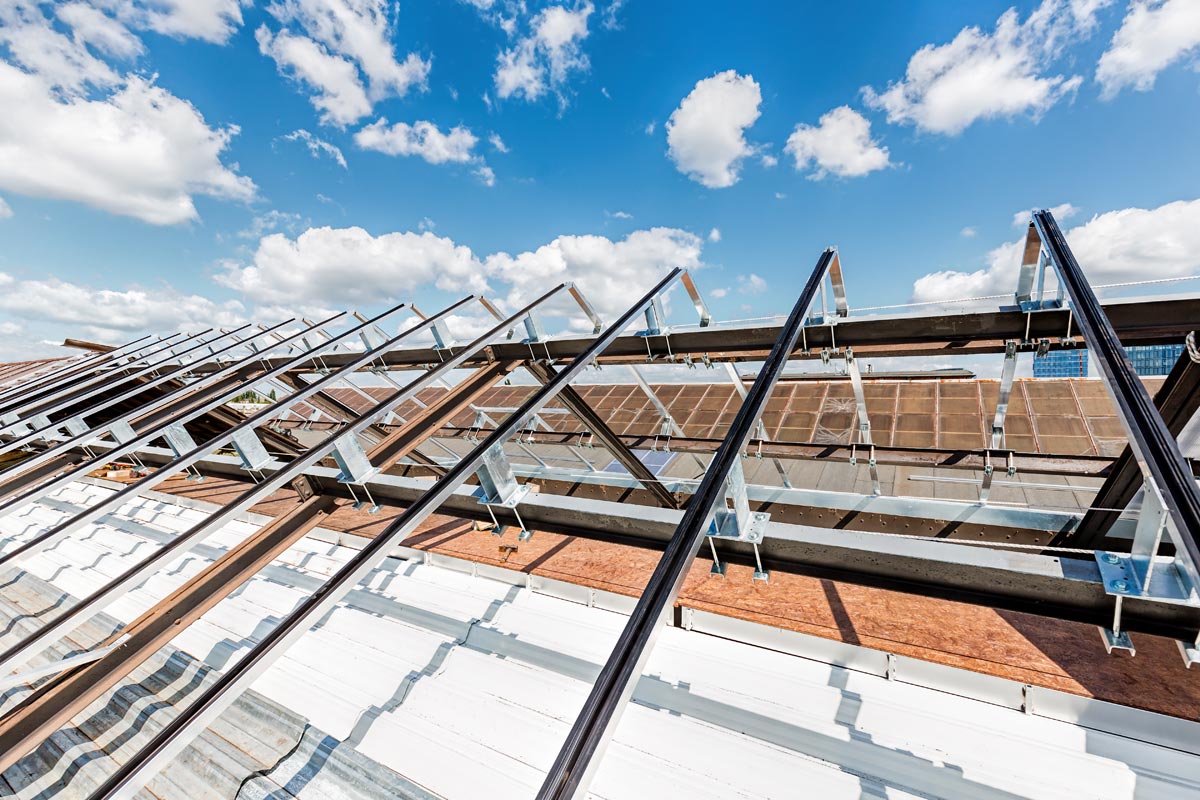
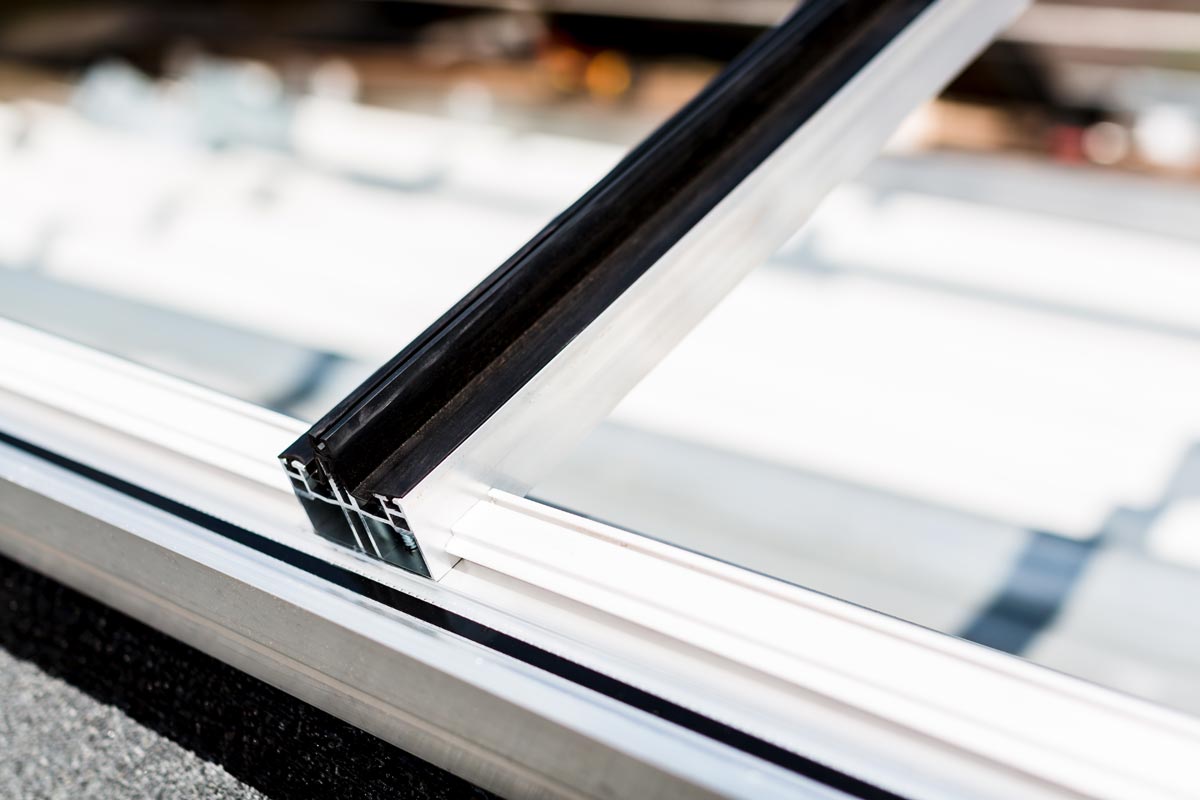
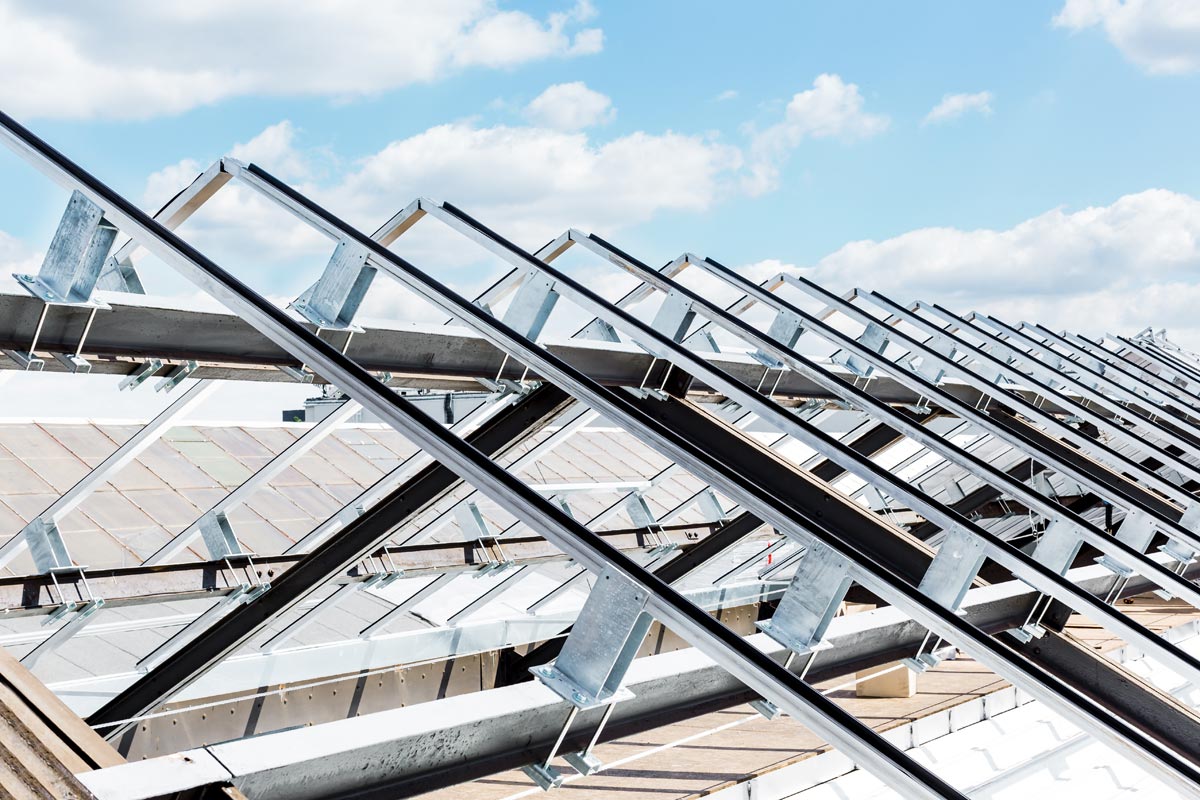
Thermische isolatie
Effectieve thermische isolatie is een belangrijk voordeel van onze ALUCO SKYLIGHT TR THERM-dakramen. De doorlopende dakramen op het dak van het B1-gebouw zijn beschermd tegen koudebruggen door het gebruik van aluminium isolatieprofielen, de zogenaamde thermische onderbrekers, die in elk dakraam zijn aangebracht. Daarnaast werden de dragende profielen van de dakramen voorzien van thermische isolatiepakkingen om te voorkomen dat condensatie het gebouw binnendringt.
Het onderste profiel van het dakraam heeft ook een isolerende pakking over de hele lengte. Bovendien is er een extra profiel geïntegreerd tussen de individuele ribben van het onderprofiel van het dakraam om de thermische isolatie van het hele systeem te verbeteren.
Ventilatieroosters
Alle doorlopende dakramen zijn voorzien van ventilatieopeningen.
Aluco Skylight Air-ventilatieroosters zijn ontworpen voor installatie in dakramen met doorlopende tongewelven en veelhoekige dakramen. Ze vormen een nieuwe toevoeging aan ons Aluco Skylight-dakraamsysteem en dienen voor de dagelijkse ventilatie.
De ventilatieopeningen worden geïnstalleerd in doorlopende dakramen en zorgen voor een effectieve daglichttoetreding in de binnenruimte en een goede luchtcirculatie. Dit beïnvloedt op zijn beurt de luchtkwaliteit binnenshuis aanzienlijk en verbetert het comfort en de werkefficiëntie van de gebruikers binnen de industriële faciliteit.
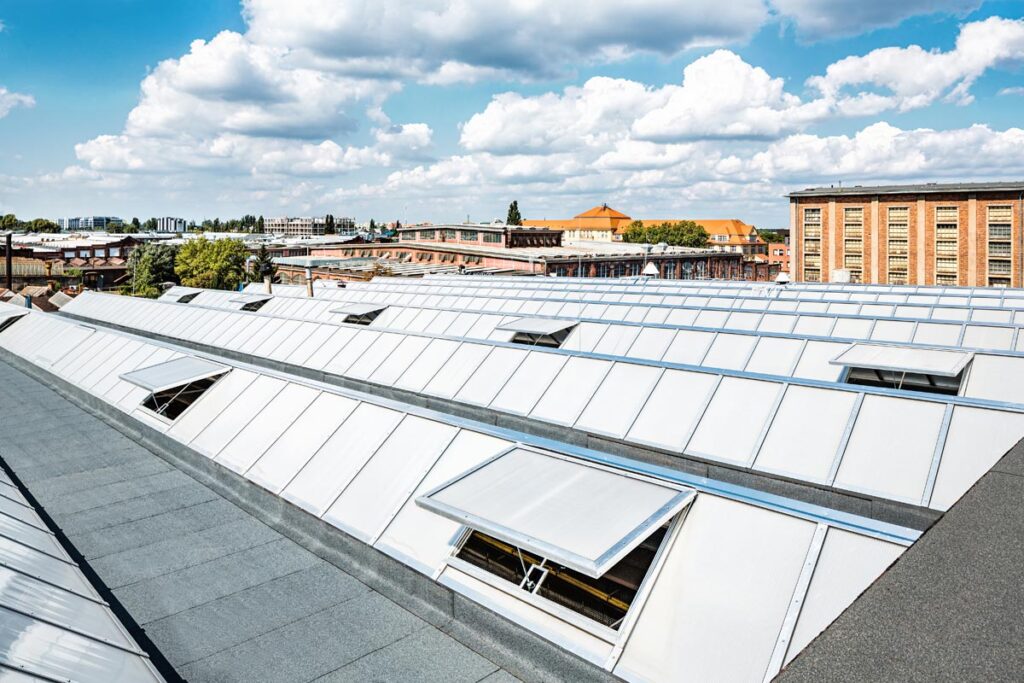
Ontdek Aluco Skylight TR Therm
Werkschema en uitvoering van de werkzaamheden
De volgende maatregelen werden geïmplementeerd om aan het werkschema te voldoen:
I. Het oppervlak onder de gedemonteerde dakramen beschermen. Een van de voor de hand liggende doelstellingen van deze fase was het garanderen van veilig werk voor de installatieteams van Aluco System tijdens de demontagewerkzaamheden en de installatie van nieuwe dakramen, en het mogelijk maken van veilig werk in het gebouw in de ruimte direct onder de dakramen. Tijdens onze werkzaamheden verliepen de werkzaamheden in het gerenoveerde gebouw zonder onderbrekingen.
II. Bij de installatie van de dakramen werd een specifieke regel gevolgd: de hoeveelheid gedemonteerde dakramen was gelijk aan de hoeveelheid nieuw geïnstalleerde dakramen. Deze aanpak beperkte de mogelijke negatieve impact van regenval op het werkgebied.
III. Voor de installatiewerkzaamheden gebruikten we speciale aluminium loopbruggen. Het aluminium rooster, ontworpen door de technische afdeling van Aluco System, had de vorm van loopbruggen met steunen op 9 m afstand en een breedte van 0,9 m, waardoor de platen met troggen gemakkelijk en snel konden worden geïnstalleerd om het dakraamoppervlak te beschermen.
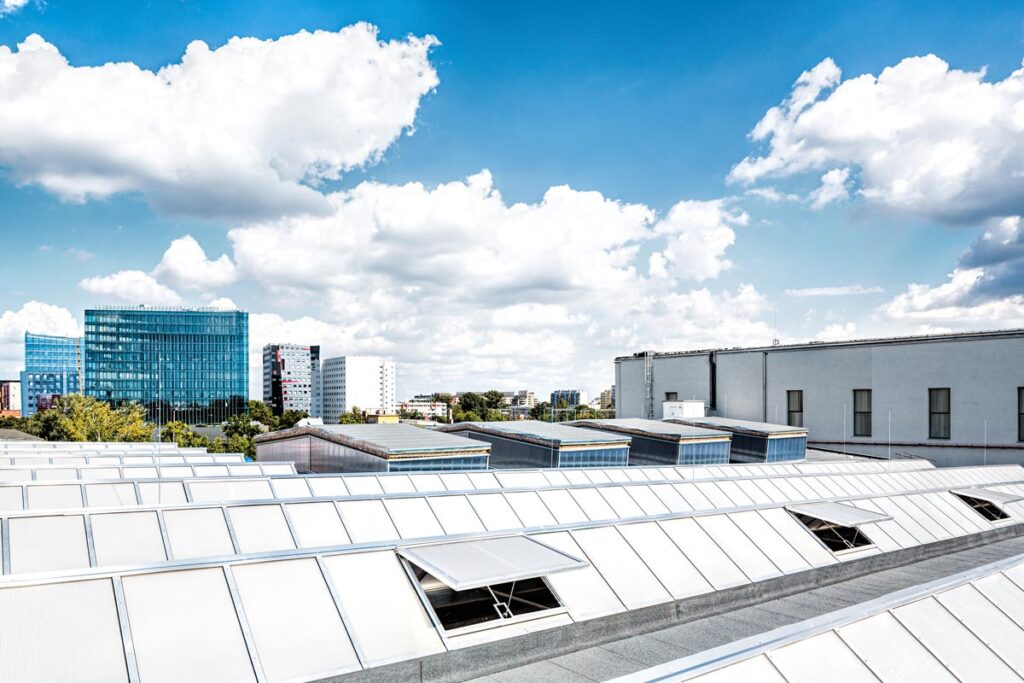
Noordelijk gedeelte: 11-2019 – 1-2020
Dakramen: ALUCO SKYLIGHT TR THERM
Afmetingen: 3000 mm x 40 000 mm
Hoeveelheid: 8 stuks
Warmteoverdrachtscoëfficiënt: U = 1,1 W/m2K
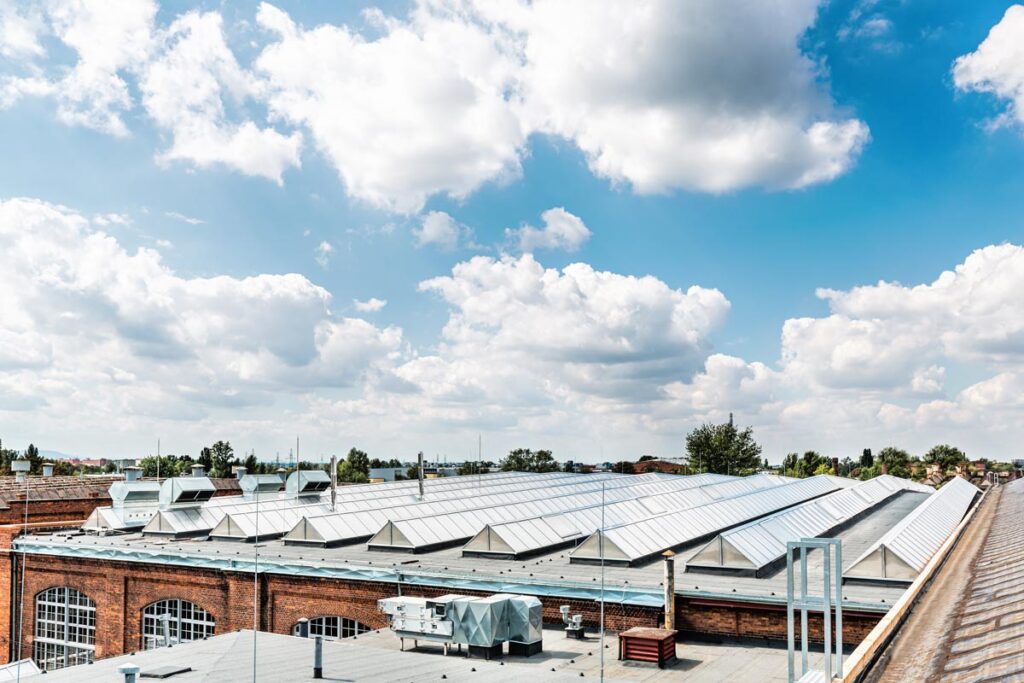
Hala południowa: 07.2020 – 07.2020
Dakramen: ALUCO SKYLIGHT TR THERM
Afmetingen: 3000 mm x 40 000 mm
Hoeveelheid: 9 stuks
Warmteoverdrachtscoëfficiënt: U = 1,1 W/m2K
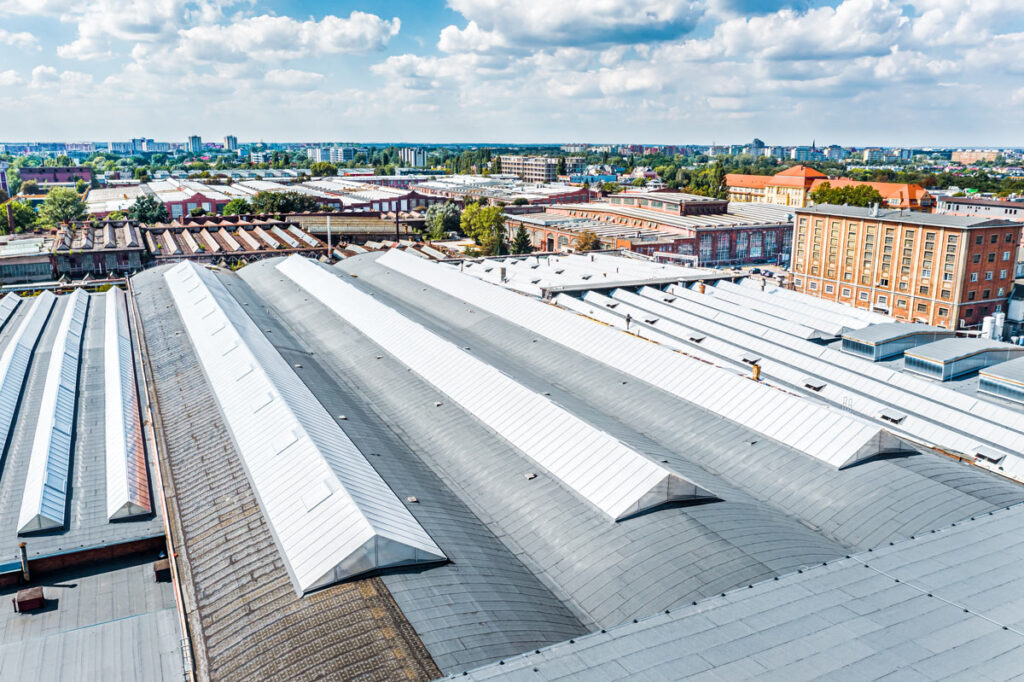
Hala centralna: 05.2020 – 09.2020
Dakramen: ALUCO SKYLIGHT TR THERM
Afmetingen: 8000 mm x 108 000 mm
Hoeveelheid: 3 stuks
Warmteoverdrachtscoëfficiënt: U = 1,1 W/m2K
Implementatie van Fase II
THERMISCHE MODERNISERING VAN DE GEVEL
Tijdens de tweede fase van ons project zijn we begonnen met de upgrade van een deel van de gevel van het gebouw, waarbij we ervoor kozen om polycarbonaatpanelen van ALUCO PANEL te gebruiken als het primaire vulmateriaal. Deze verbetering was specifiek gericht op het productiegedeelte van het B1-gebouw, zoals te zien is in de onderstaande afbeelding.
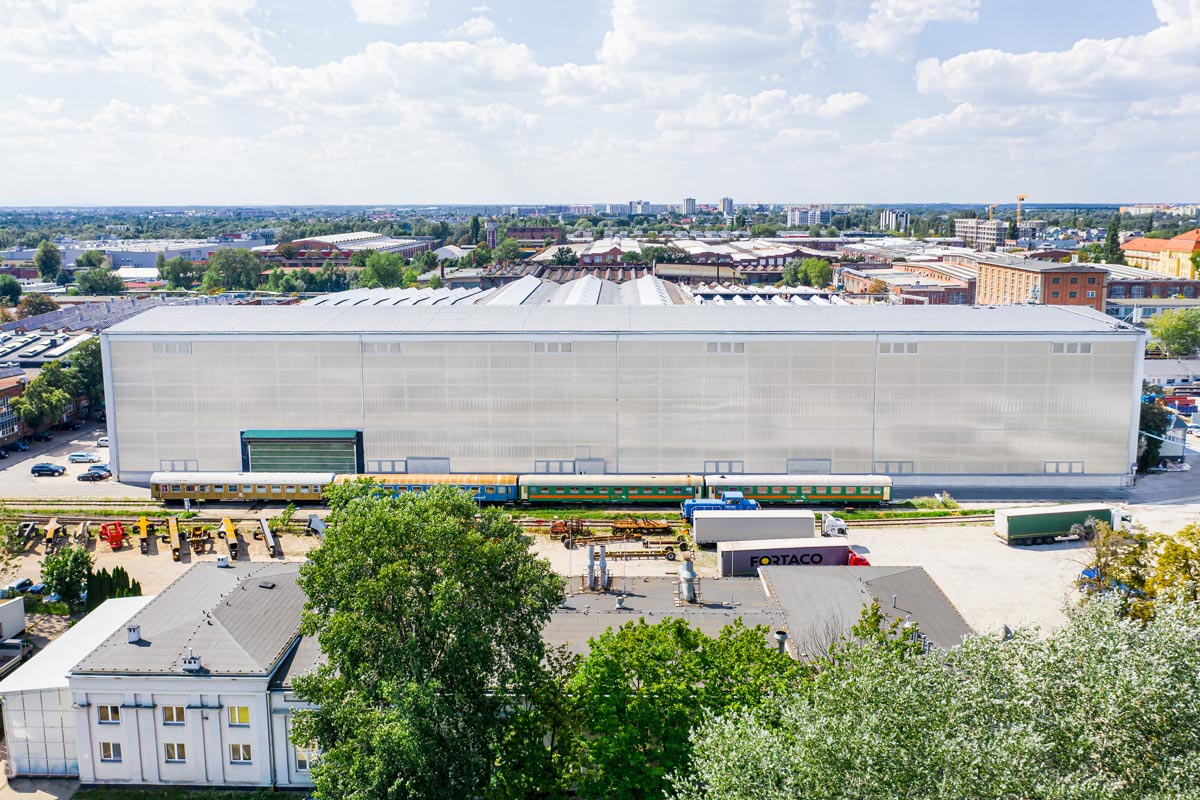
Vóór de upgrade bestond de gevel van gebouw B1 uit een combinatie van draadglas en polycarbonaatpanelen met dubbele beglazing, allemaal gevat in ongeïsoleerde stalen profielen.
De warmteoverdrachtscoëfficiënt van een dergelijke gevel varieerde van 3,5 W/m²K tot 5,5 W/m²K. Als gevolg daarvan week de thermische prestatie van de gevel aanzienlijk af van de hedendaagse normen, wat leidde tot aanzienlijke warmteverliezen en bijgevolg hoge uitgaven voor de verwarming van het gebouw.
ALUCO PANEL AP 50
We stelden voor om een nieuwe gevel te installeren met het ALUCO PANEL AP 50- systeem. Het systeem bestaat uit polycarbonaatpanelen van 50 mm met een warmteoverdrachtscoëfficiënt van U = 0,9 W/m²K, gevat in thermisch geïsoleerde aluminium profielen.
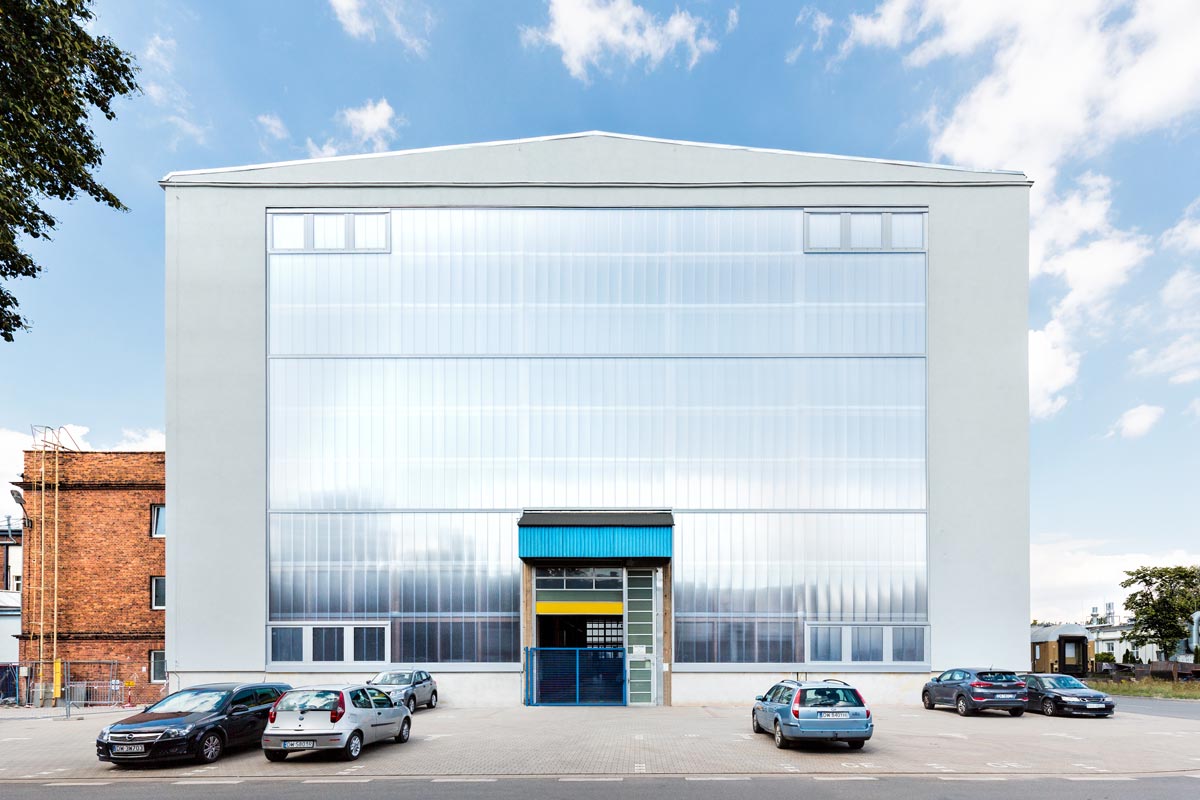
ALUCO PANEL
POLYCARBONAAT GEVEL
ALUCO PANEL is een innovatief en duurzaam systeem van polycarbonaat gevels die bestand zijn tegen weersomstandigheden, UV-straling en chemische factoren. Deze panelen zijn robuust, slagvast en eenvoudig te installeren. Polycarbonaat wordt vaak gebruikt in de bouwindustrie als materiaal voor gevels, daken en ruimteverdelers. Onze doorschijnende polycarbonaat panelen zijn bijzonder geschikt voor gebruik in opslaggebouwen, productiefaciliteiten en openbare gebouwen.
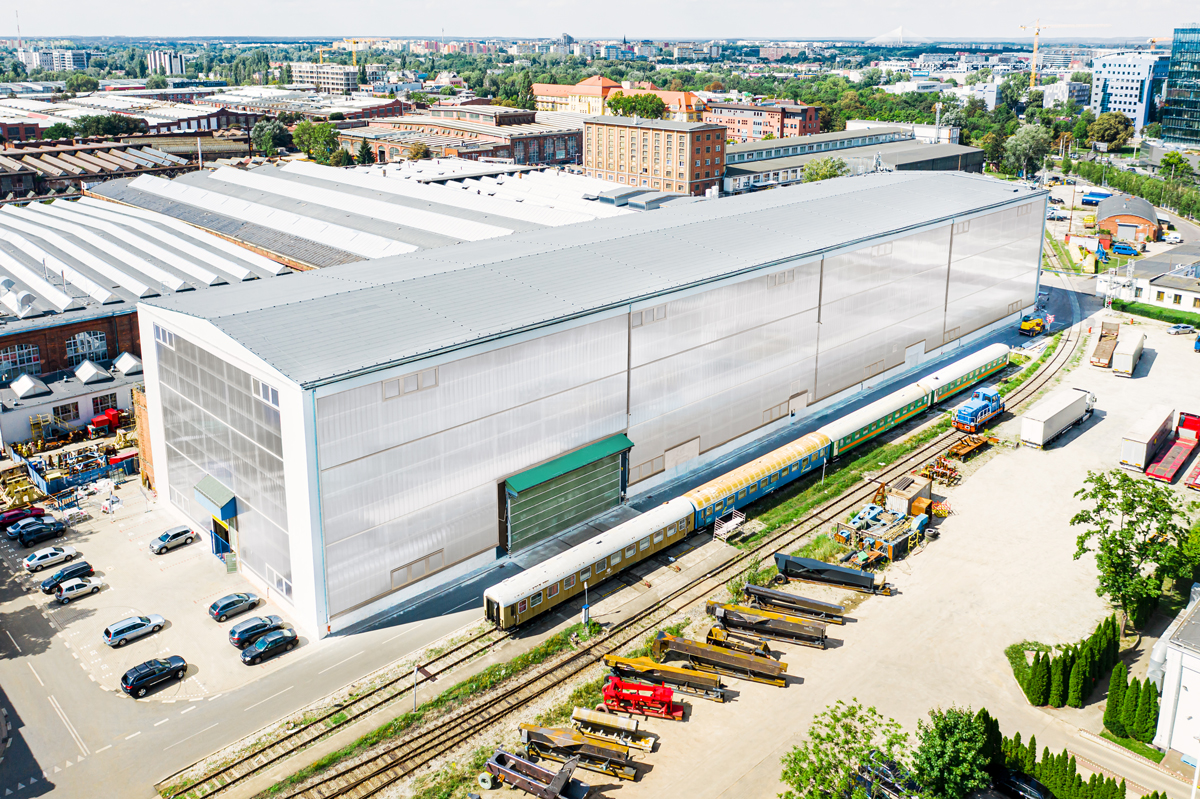
De installatie van polycarbonaat panelen
De oppervlakte van de gerenoveerde gevel was 5.000 m². De uitdaging kwam voort uit de hoogte van het gebouw van 19,5 m en de moeilijke toegang tot de kopgevels. Dit probleem werd opgelost door gebruik te maken van een gespecialiseerde telescoophoogwerker met een reikwijdte van 53,0 m. Vanuit zijn mand kon het installatiepersoneel de installatiewerkzaamheden veilig uitvoeren.
Om het werkschema te kunnen volgen, was het van cruciaal belang om professionele telescoophoogwerkers en platformen aan te schaffen. Dit materiaal vergemakkelijkte de veilige en efficiënte ontmanteling van de bestaande gevel en de installatie van de nieuwe gevel.
Net als bij de thermische modernisering van de dakramen op het dak van het gebouw, werkte het gebouw continu tijdens de thermische modernisering van de gevel.
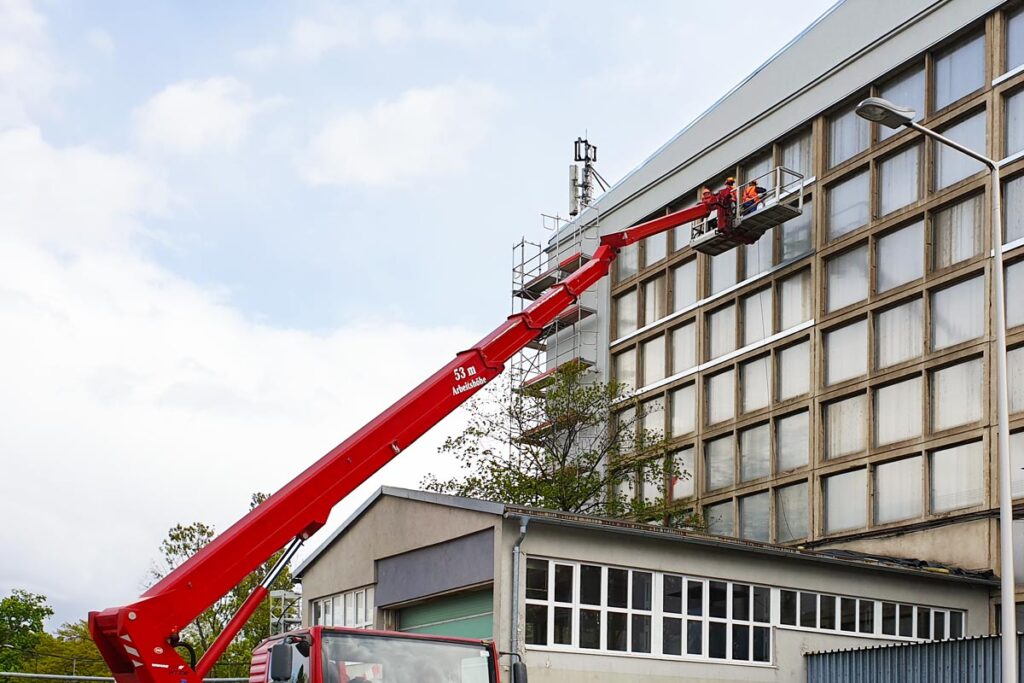
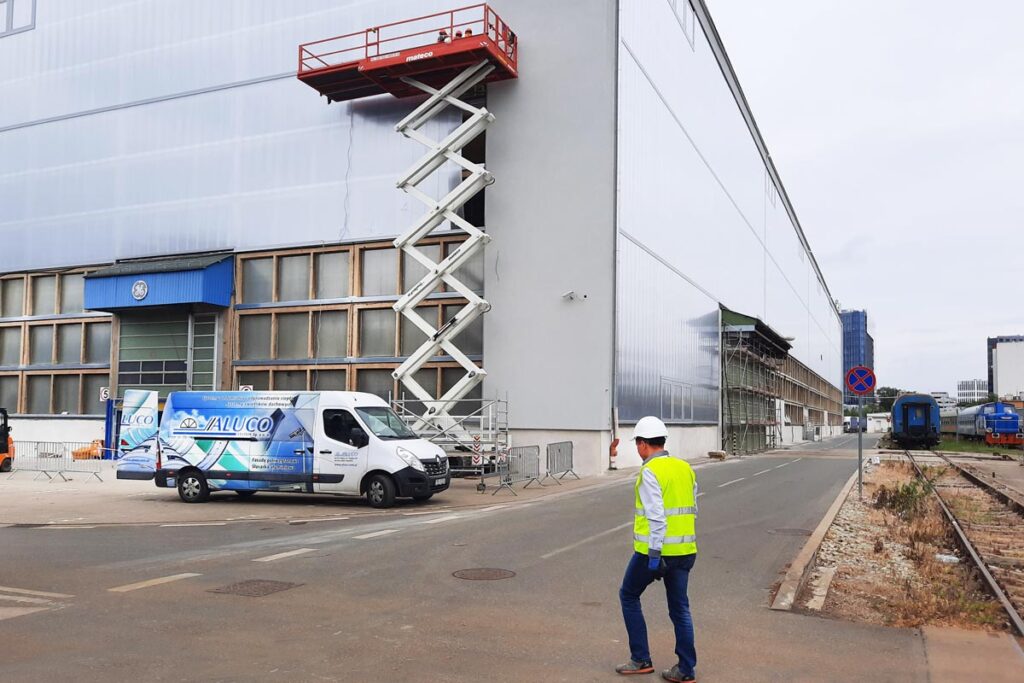
Uitvoering van de werkzaamheden
De eerste fase omvatte de installatie van de draagstructuur van koud gevormde stalen profielen. Vervolgens installeerden we aluminium perimeterprofielen met uitzettingsvoegen. De volgende stap was de geleidelijke demontage van de bestaande beglazing en we bedekten de gedemonteerde oppervlakken met nieuwe polycarbonaatpanelen om te voorkomen dat er regen in het gebouw zou vallen tijdens werkonderbrekingen (zoals ’s nachts en in het weekend).
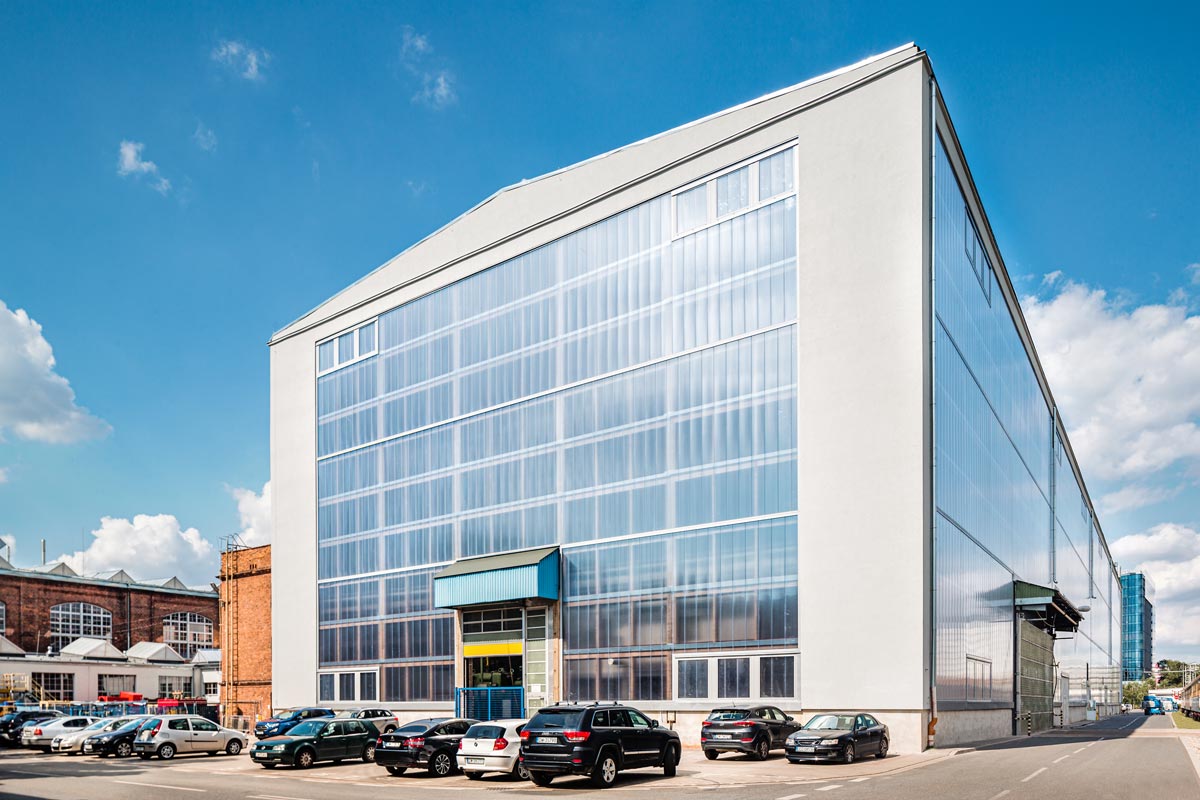
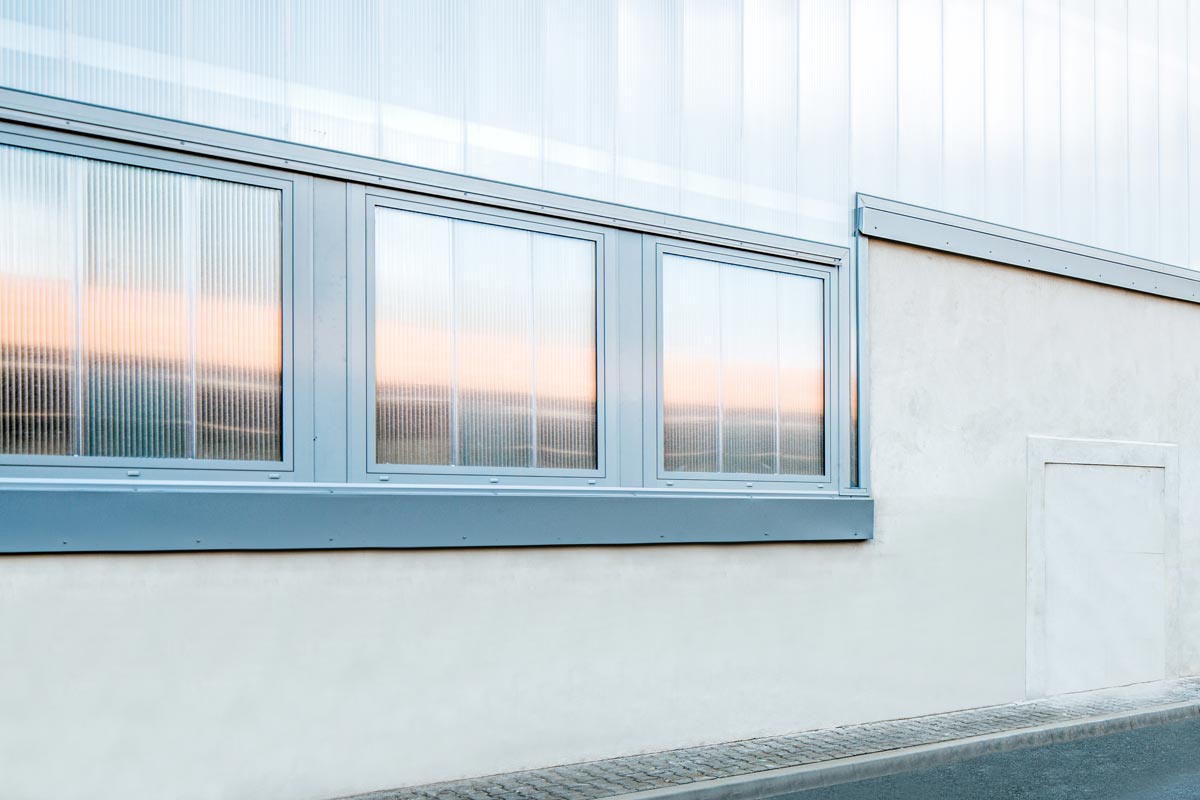
Ventilatieramen
De gevel werd uitgerust met 20 ventilatieramen van 1.200 mm x 1.200 mm. Net als de gevel werden deze ramen gevuld met ALUCO PANEL AP50 polycarbonaatpanelen. De ramen worden bediend door elektrische bedieningen met een slag van 350 mm, die vanaf het gebouw worden bediend via het ventilatiebedieningspaneel.
Dozamel Case Study
Pobierz PDF
Download de volledige versie van het artikel "Dozamel Case Study" als PDF-bestand naar uw apparaat. Tekst in het Engels.
Afronding van het project
Deel III
Het project werd voltooid volgens het werkschema. De opgewaardeerde gebouwen zijn er zeker visueel op vooruitgegaan; de nieuwe dakramen en gevels hebben het erfgoedgebouw er veel aantrekkelijker doen uitzien.
6,860 M²
DAKRAMEN
5,000 M²
POLYCARBONAAT PANELEN
500 %
BETERE THERMISCHE PRESTATIES
200 %
MEER DAGLICHT
Meer daglicht
Het meest cruciale aspect was echter de fundamentele verbetering van de twee primaire functies: doorschijnendheid en thermische prestaties. Zelfs op bewolkte dagen heeft het Dozamel-gebouw geen elektrische verlichting meer nodig. De polycarbonaatpanelen die werden gekozen als vulling voor de dakramen bieden een optimale manier om daglicht in het gebouw binnen te laten, terwijl ze ook zorgen voor een gelijkmatige verstrooiing van het licht op dagen met intens zonlicht.
Verbetering van de thermische prestaties
Het hoofddoel van de thermische isolatie was het verbeteren van de thermische prestaties van het gebouw en dit aspect wordt besproken in de projectsamenvatting. Het doel van thermische isolatie is om de warmteoverdrachtscoëfficiënt zoveel mogelijk te minimaliseren om de benodigde verwarmings- (of koelings-) kosten te verlagen.
Dit doel is met succes bereikt.
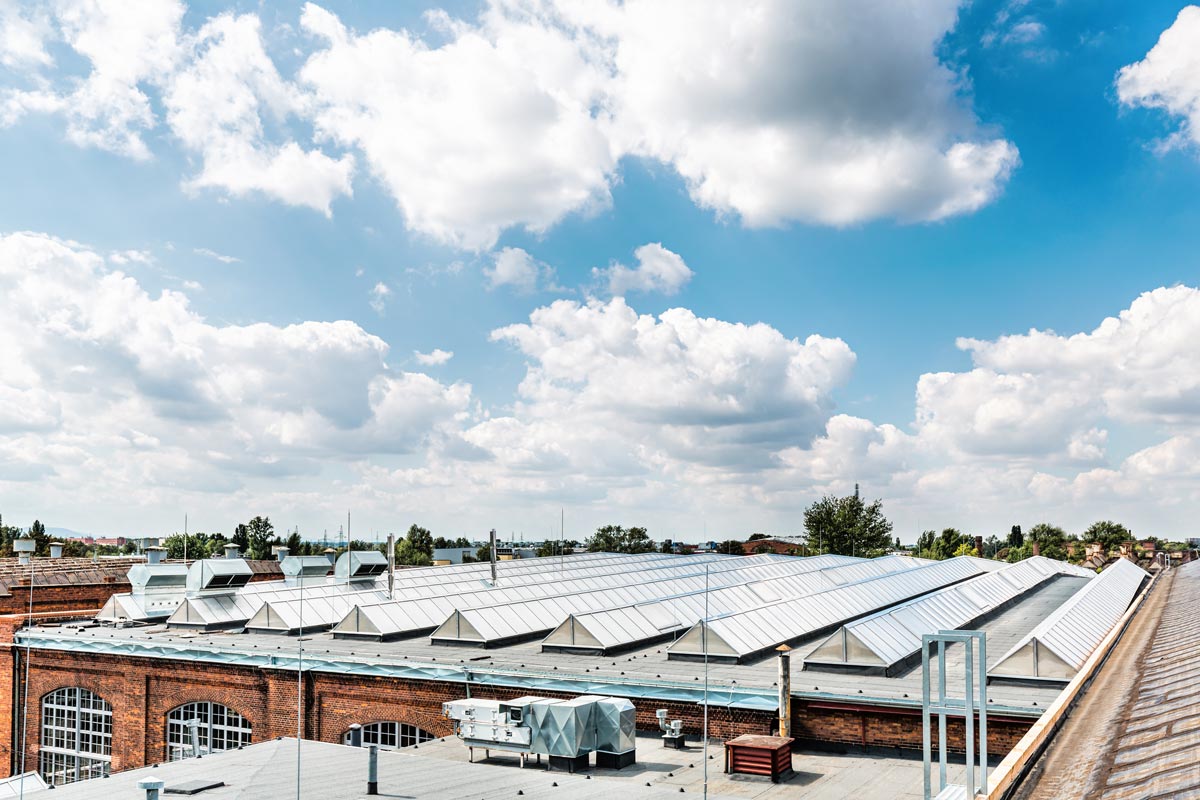
Simulatie van besparingen
Niets kan het succes van het project beter illustreren dan harde cijfers. Daarom geeft de simulatie hieronder de indicatieve energiebesparing weer die is gegenereerd door de upgrade van de dakramen in gebouw B1.
Volgens de DIN 4701-norm bespaart een verlaging van de warmteoverdrachtscoëfficiënt [U] met 0,1 W/m²K 0,9-1,3 liter stookolie of 1,0-1,5 m³ aardgas per vierkante meter beglazing. De onderstaande berekeningen illustreren de potentiële besparingen per vierkante meter beglazing voor verschillende verlagingen van de warmteoverdrachtscoëfficiënt van individuele ruiten en polycarbonaatpanelen.
Beglazingsprestaties vóór de upgrade:
- 4 mm, enkele beglazing,
- U: 5,9 W/m²K.
Beglazingsprestaties na de upgrade:
- vulling met een polycarbonaat paneelunit,
- U: 1,1 W/m²K.
BEREKENINGEN VAN WARMTEVERLIES
Warmteverlies Q (kW) = oppervlakte (m²) x U (W/m² K) x “At” temperatuurverschil (K)
“At” Temperatuurverschil verwijst naar het temperatuurverschil tussen binnen- en buitenlucht. Als het productiegebouw wordt verwarmd tot 15°C, is de warmte die onder het dak wordt verzameld ongeveer 35°C, afhankelijk van de hoogte van het gebouw. Bij een buitentemperatuur van 0°C is het temperatuurverschil (At) 35°C, wat overeenkomt met 35 Kelvin (K).
De totale oppervlakte van de vervangen dakramen op het dak van het B1-gebouw van DOZAMEL was 6.860 m².
Warmte-energieverlies voor enkele beglazing (vóór de upgrade):
Q = 6.860,0 m² x 5,9 W/m²K x 35°C = 1.416.600 W = 1.416,6 kW
Warmtevermogen verlies voor een polycarbonaat paneel (na de upgrade):
Q = 6.860,0 m² x 1,1 W/m² K x 35°C = 264.100 W = 264,1 kW
Het verschil tussen de twee waarden toont de verandering in warmteverliezen als gevolg van de thermische modernisering:
1.416,6 kW – 264,1 kW = 1.152,5 kW
Berekening van het warmteverschil gedurende het jaar:
1.152,5 kW x 24 h x 220 verwarmingsdagen = 6.085.200 kWh
Definitieve schatting van besparingen
Lagere calorische waarde voor:
• aardgas – ca. 9,06 kWh/m³,
• stookolie – ca. 10,05 kWh/l.
BESPARING OP STOOKOLIE:
6.085.200 kWh – 10,05 kWh/l = 605.500 l stookolie x PLN 0,80/kWh = PLN 484.400,00
BESPARING OP AARDGAS:
6.085.200 kWh – 9,06 kWh/m³ = 671.700 m³ aardgas x PLN 0,55/kWh = PLN 369.400,00
De berekeningen zijn gebaseerd op de volgende brandstofprijzen (prijsniveau op 10/2023):
- stookolie: PLN 0,80/kWh,
- aardgas: PLN 0,55/kWh.
OPMERKING: De schatting is exclusief de besparing op de kosten van elektriciteit die nodig is voor een goede verlichting van het gebouw!
Uitleg voor de berekeningen
De warmteoverdrachtscoëfficiënt, meestal U genoemd, is een maat voor het vermogen van een materiaal of constructie om warmte door te geven. Hoe lager de coëfficiënt, hoe beter de bescherming tegen warmteverlies en warmtewinst van buitenaf. Dit is cruciaal voor het evalueren van de isolerende prestaties van gebouwen – hoe lager de warmteoverdrachtscoëfficiënt, hoe kleiner de warmteverliezen door muren, ramen of daken. De coëfficiënt wordt gemeten in W/m²K, d.w.z. in watt per vierkante meter per kelvin.
Dozamel Case Study
Pobierz PDF
Download de volledige versie van het artikel "Dozamel Case Study" als PDF-bestand naar uw apparaat. Tekst in het Engels.
Zie het verschil
De onderstaande foto’s tonen de effecten van ons werk. We hebben soortgelijke foto’s die vóór de opwaardering van de dakramen en de gevel zijn genomen, naast elkaar gezet met foto’s die na de voltooiing van alle werkzaamheden zijn genomen. Het is meteen duidelijk dat, naast de verbetering van tal van technische specificaties, het gebouw ook visueel veel aantrekkelijker is geworden.
Tip: Gebruik de schuifbalk in het midden van de foto om te wisselen tussen de “voor” en “na” aanzichten.
Thermische modernisering van dakramen
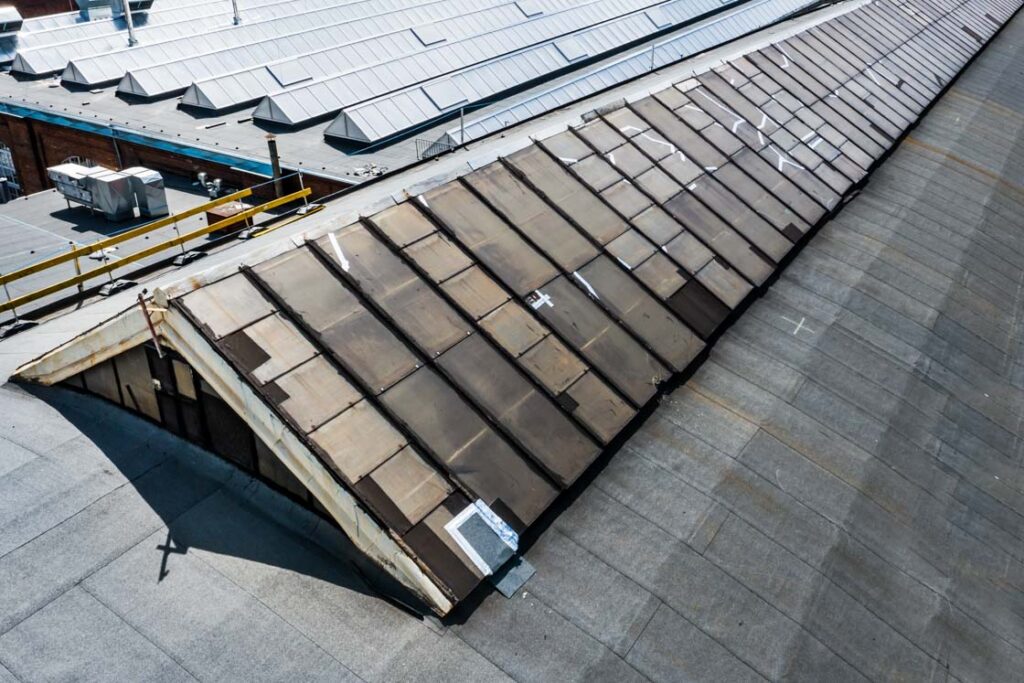
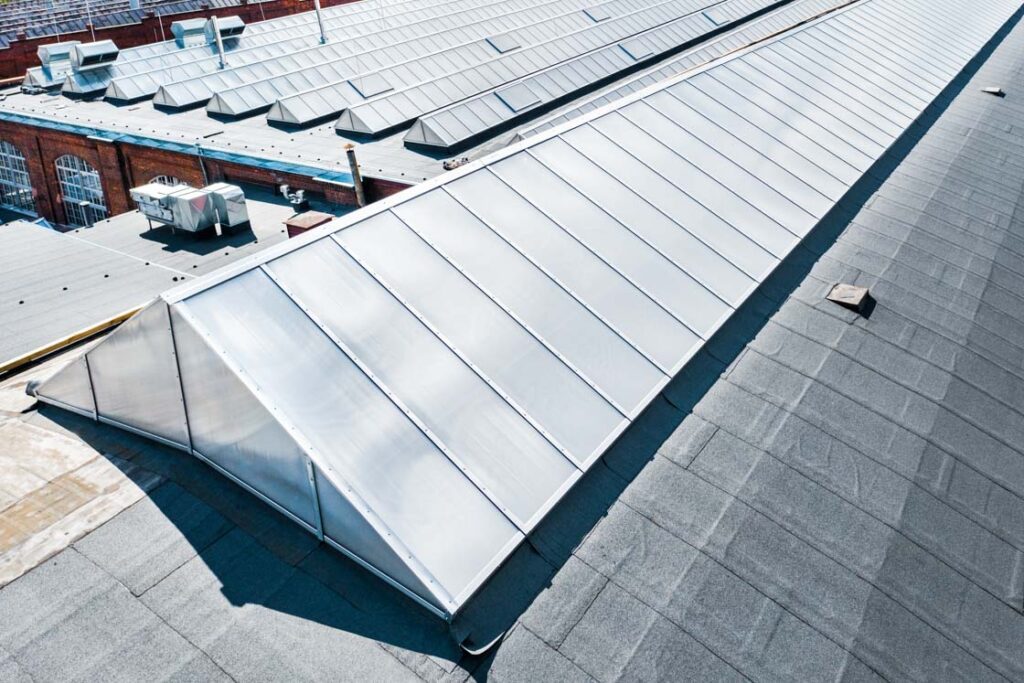
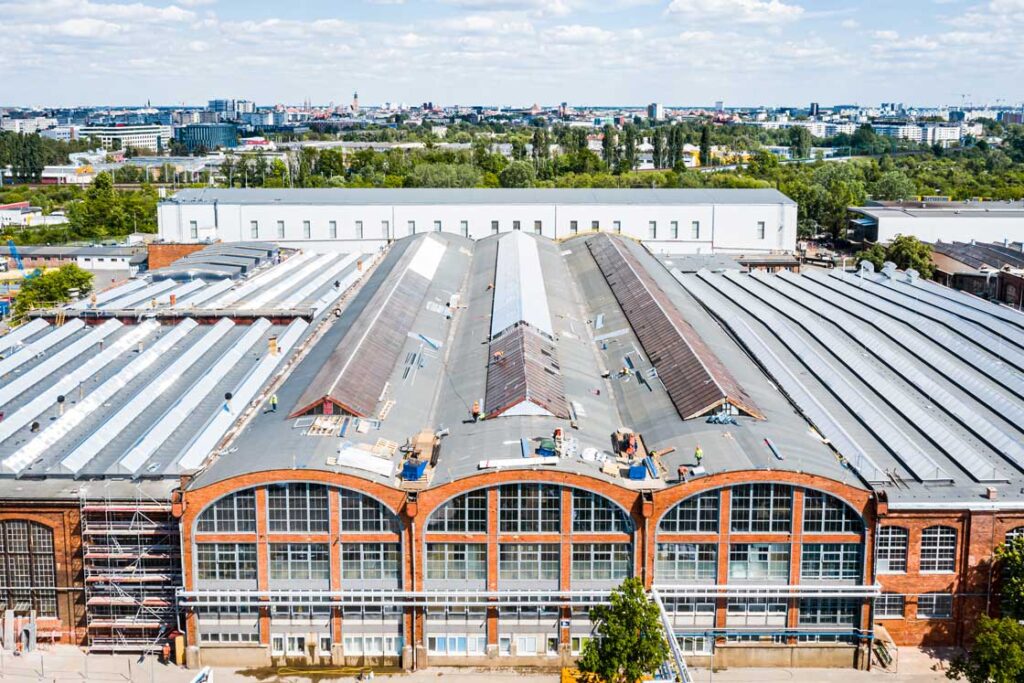
Voor de modernisatie
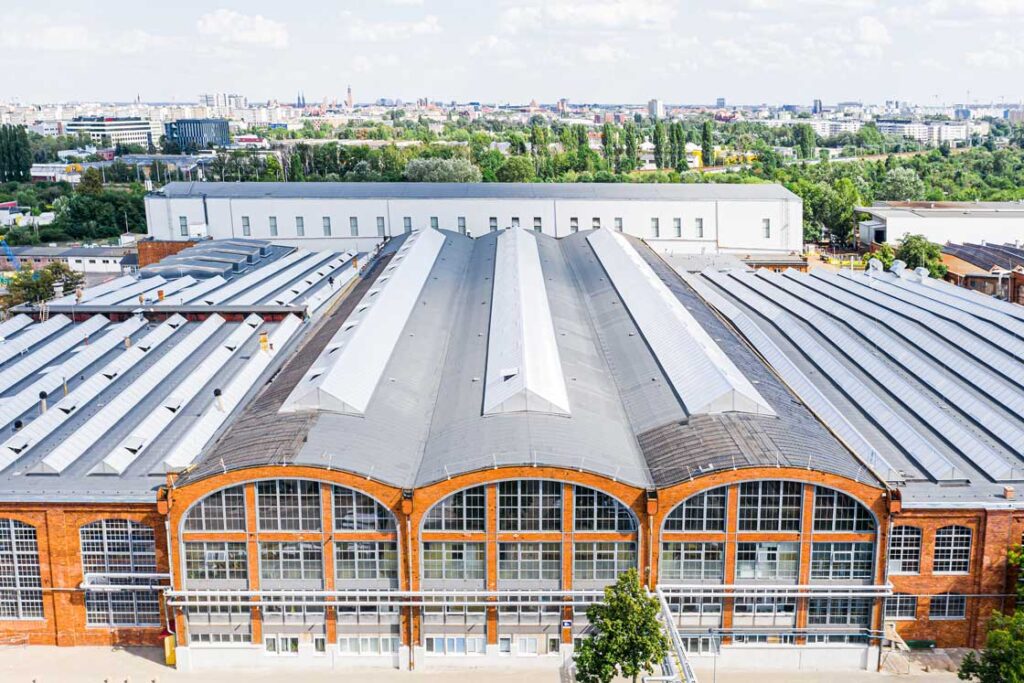
Na de modernisatie
Daglichttoetreding
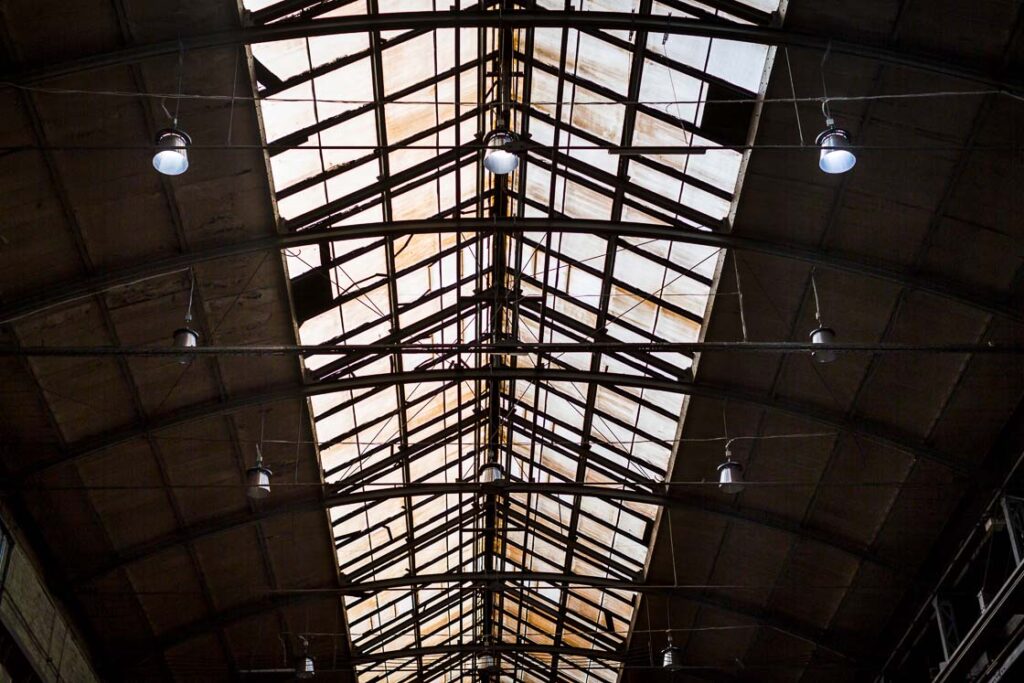
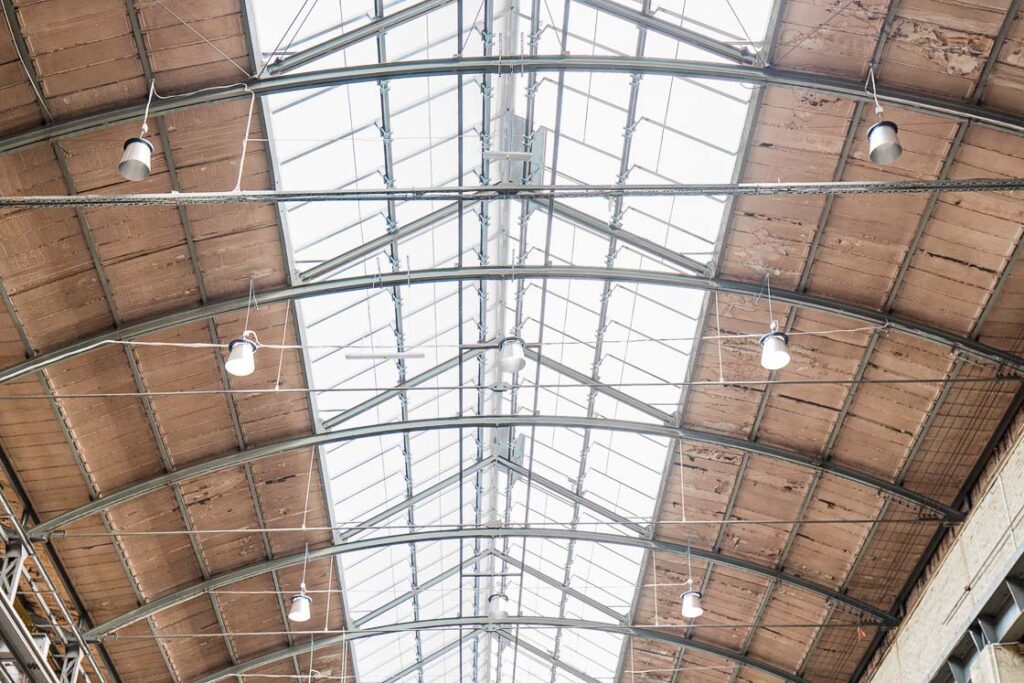
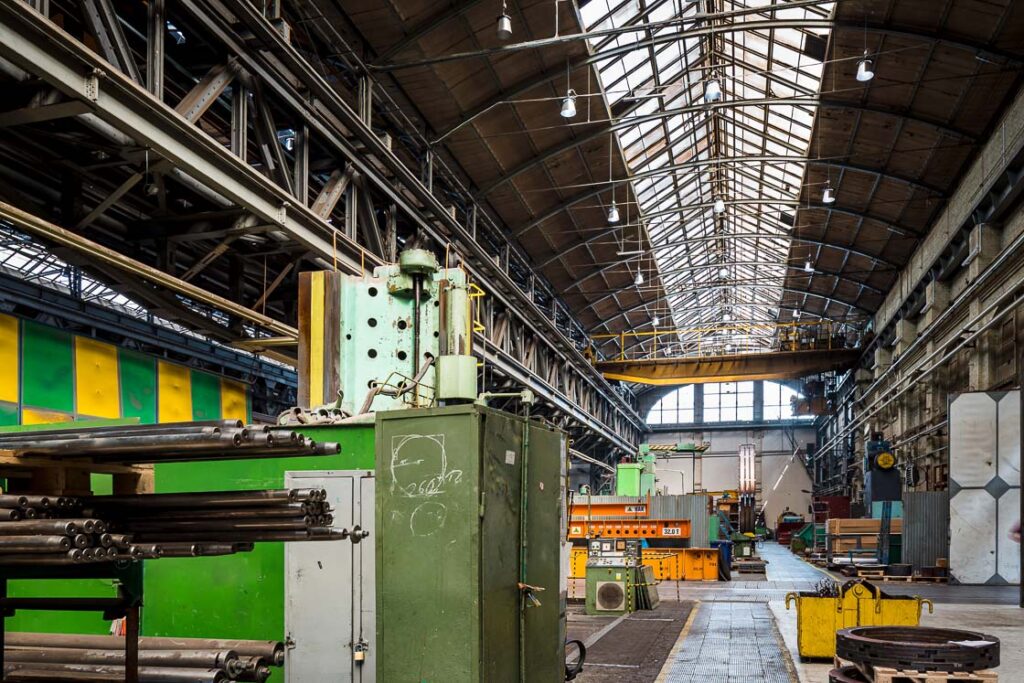
Voor de modernisatie
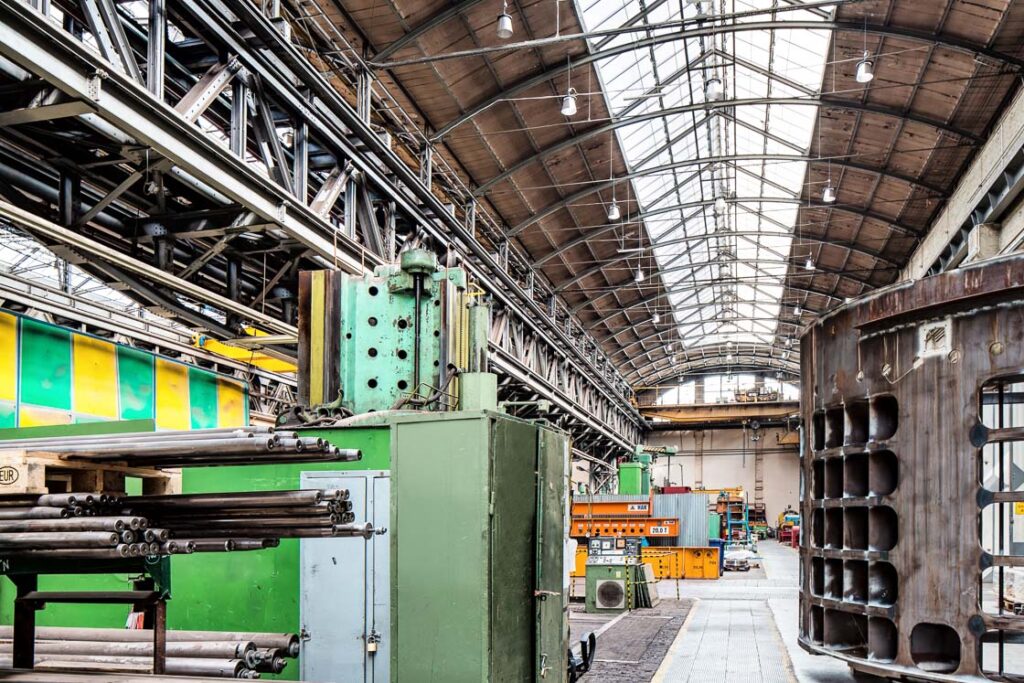
Na de modernisatie
Thermische modernisering van de gevel
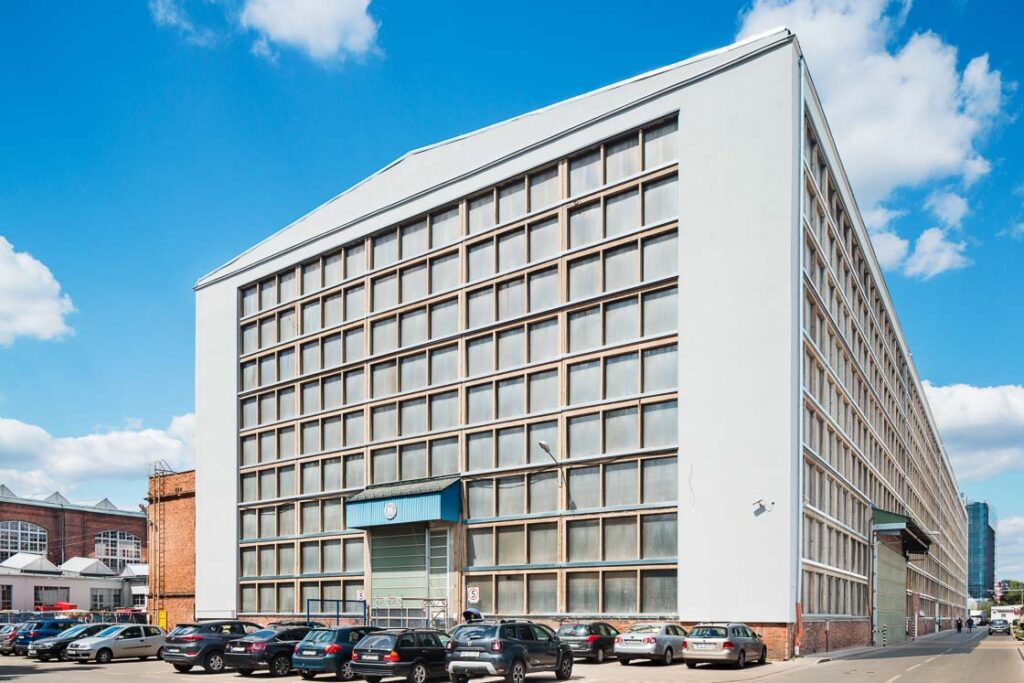
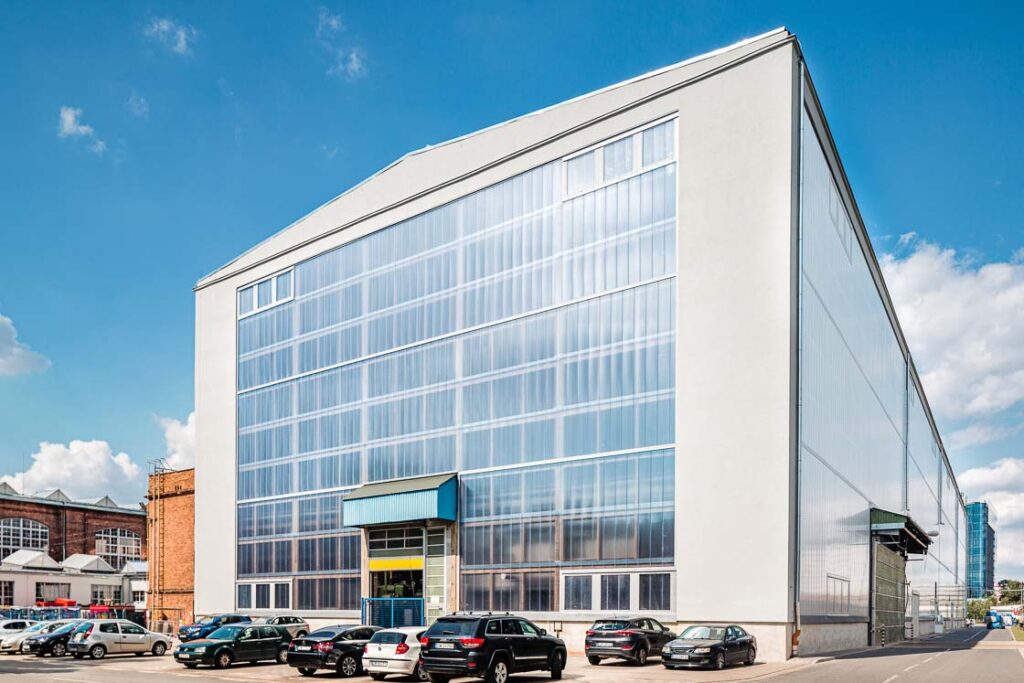
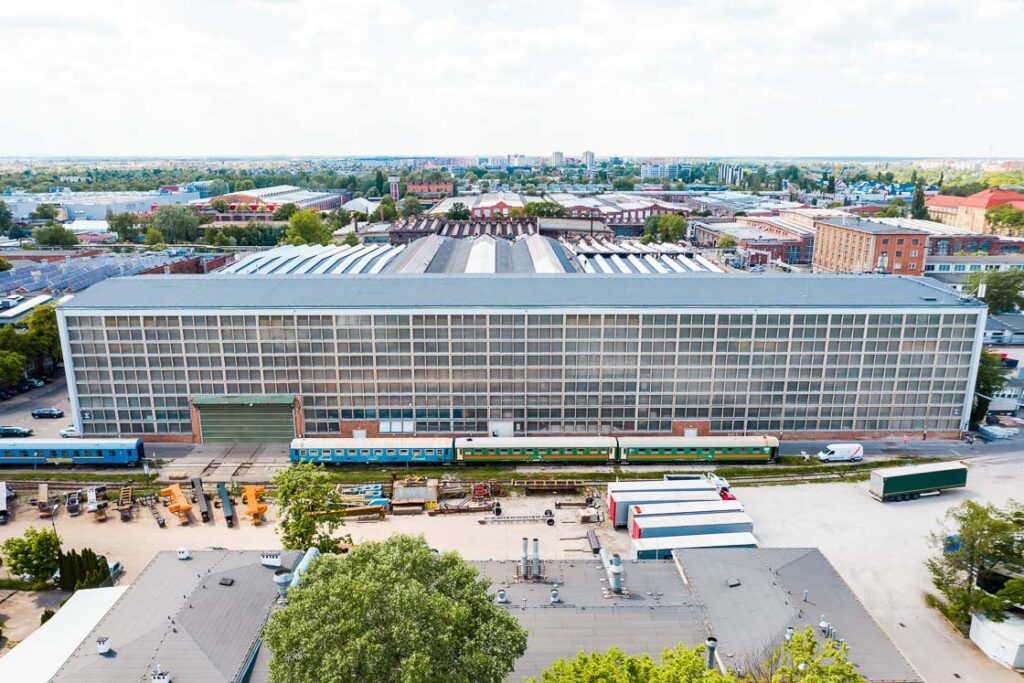
Voor de modernisatie
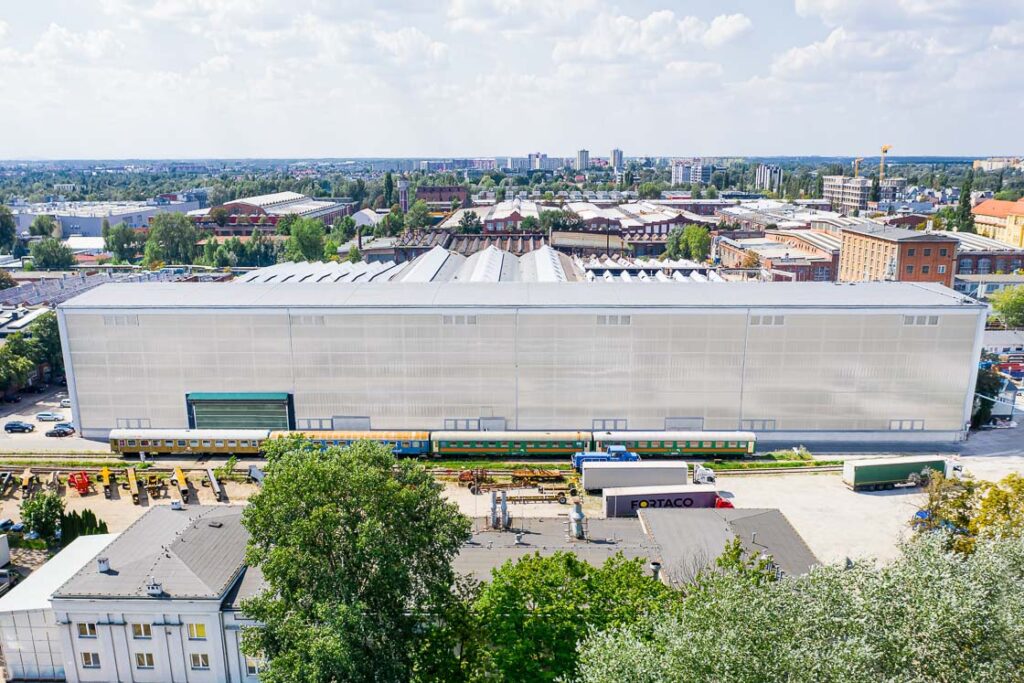
Na de modernisatie
Meer zien
dozamel
De foto's in dit artikel vormen slechts een deel van de uitgebreide fotografische documentatie van het hele project. In onze portfolio hebben we een complete fotogalerij samengesteld, ingedeeld naar de thermische modernisering van de dakramen en de gevel.
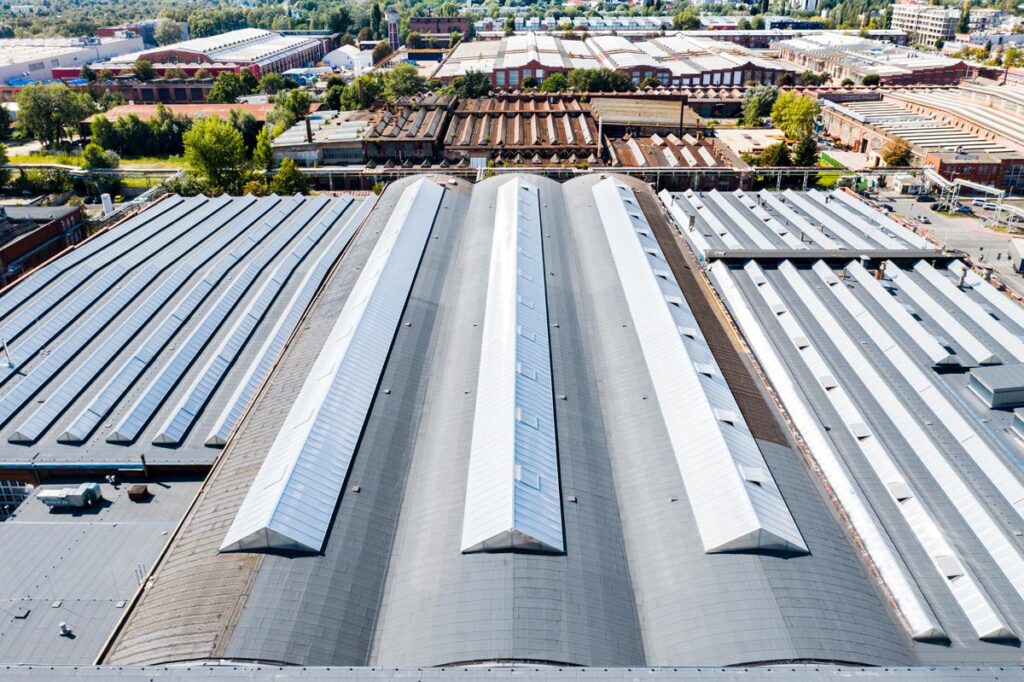
Dakramen
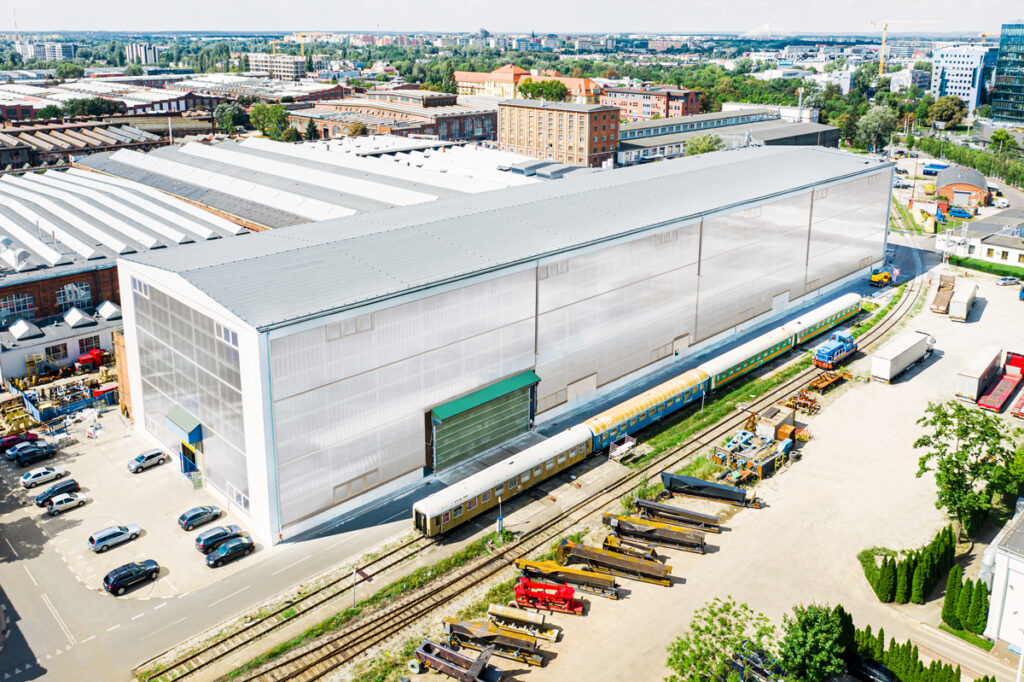
Gevel
Over ons
Aluco System
Aluco System is sinds 1997 actief op de markt en is gespecialiseerd in architecturale oplossingen voor de industrie. Onze missie is om onze klanten te helpen de voordelen van natuurlijke verlichting te maximaliseren.
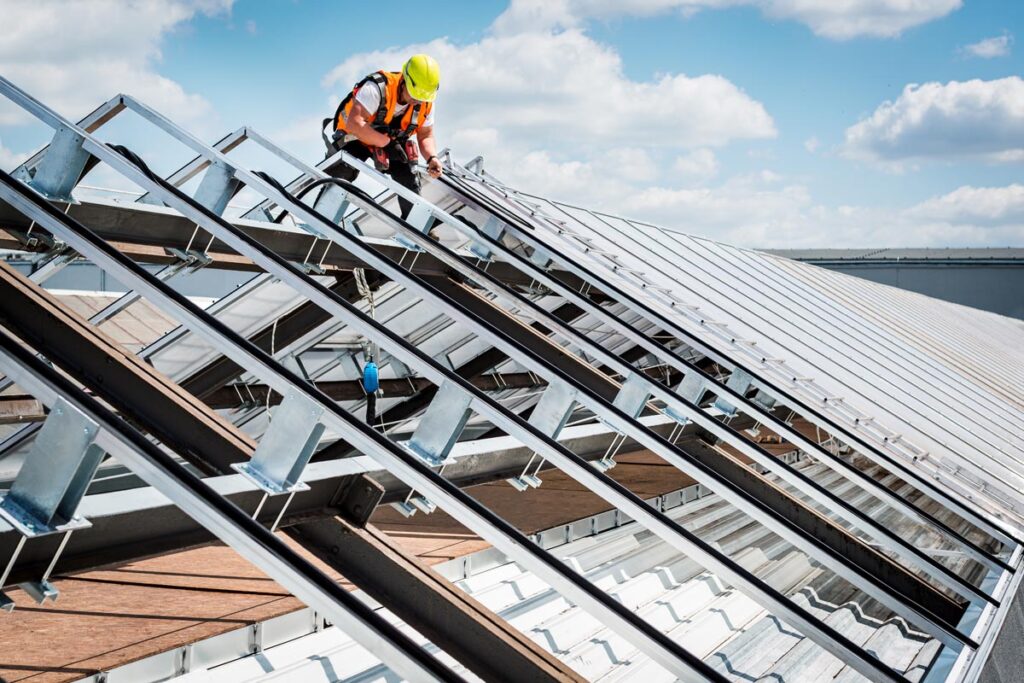
We produceren en leveren dakramen, gevels, rookbeheersing- en ventilatiesystemen, schrijnwerk van glasaluminium en brandwerend schrijnwerk. Daarnaast voeren we uitgebreide projecten uit voor de thermische modernisering van dakramen en gevels.
We ontwikkelen voortdurend meer geavanceerde en energie-efficiënte producten zonder concessies te doen aan kwaliteit en veiligheid. We zijn een 100% Pools bedrijf. Met meer dan 25 jaar ervaring en 750.000 m² geïnstalleerde dakramen zijn we een van de meest herkenbare merken in Polen.