DOZAMEL
CASE STUDY
Learn about the thermal modernization of the facade and roof of an industrial building.
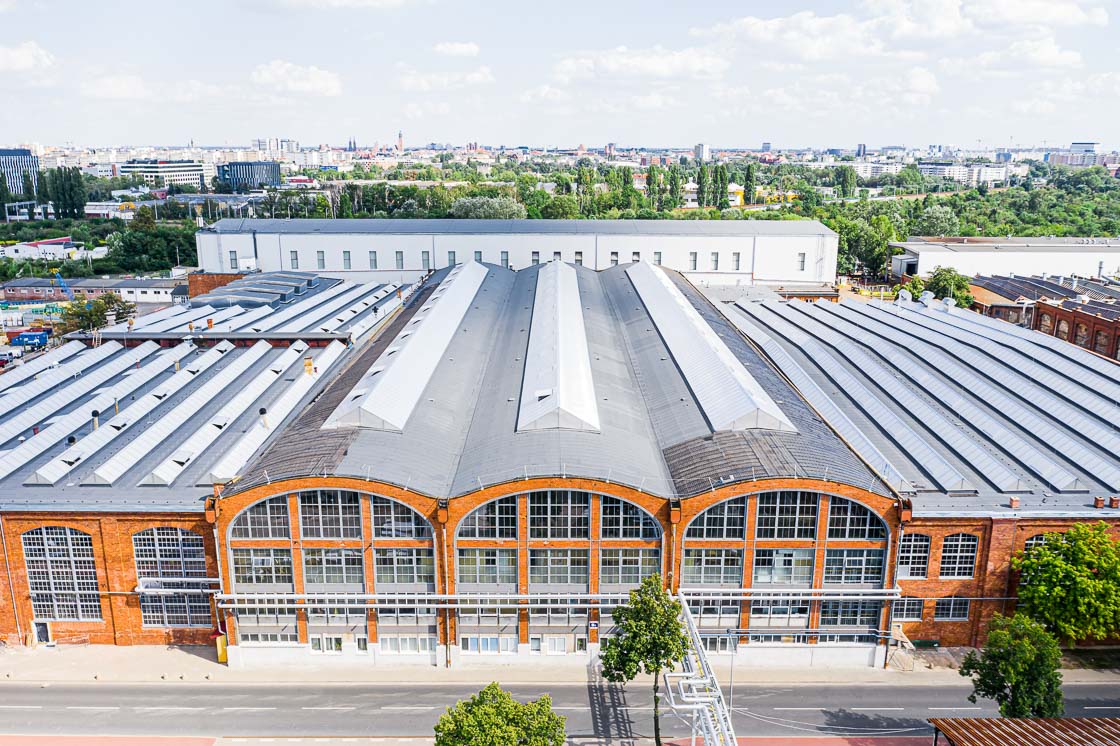
In 2020, we successfully concluded one of our most complex and demanding projects. Undoubtedly, it stood out as one of the most significant challenges encountered by Aluco System thus far. Considering our presence in the industry since 1997, there is very little that still surprises us.
The project involved the extensive thermal modernization of a production building situated in Wrocław, within one of the oldest industrial parks in Poland. The project was executed for OZBUD from Wrocław, serving as the EPC contractor. The building held historical significance, which was the primary reason for the project’s complexity.
In this article, we would like to provide you with some insights into the implementation of the project, covering the most important aspects.
A short history of the Wrocław Industrial Park
The history of the Wrocław Industrial Park (WPP) dates back to the 19th century, with Linke-Hofmann Werke and Fahrzeug und Motoren Werke factories, abbreviated as “Famo,” being key initiators of development in the area. Initially, they produced locomotives and electric machinery. During the interwar period, the site underwent a transformation into an arms production facility, operated with the involvement of prisoners from the Gross-Rosen concentration camp.
After World War II, despite extensive damage, the site was quickly rebuilt. The facility focused on manufacturing electric motors and generators. In 2003, DOZAMEL conceived the idea of establishing the DOLMEL Industrial Park on a 34-hectare site to attract businesses and leverage EU funds for the revitalization of the existing infrastructure.
However, due to an amendment of a relevant act in 2003, it became necessary to sign an agreement with the local self-government to obtain EU funding. It was only in 2005 that the agreement was finally signed, and the Wrocław Industrial Park was established. The 163-hectare area became a unified industrial center, with the city of Wrocław, DOZAMEL, Archimedes S.A., Wrocławski Park Technologiczny S.A., Bombardier Transportation Polska Sp. z o.o., and Wojdyła Inwestycje Sp. z o.o. collaborating as partners.
The establishment of the Wrocław Industrial Park was a response to the strategy of revitalizing the industrial areas of the city. The area, with its unique industrial traditions and historic heritage, was listed in the historic register. The development plan, prepared by DOZAMEL Sp. z o.o., outlined an advanced refurbishment of the industrial infrastructure.
Project Description
PART I
The project focused on the B1 industrial building situated at the Wrocław Industrial Park. The B1 building stands as the largest structure within the complex. Its history traces back to the 20th century when the German company Linke-Hofmann-Werke AG manufactured locomotives at this location. It is a 10-bay production building featuring storage, office, and staff facilities, with an approximate usable floor area of 26,000 m². The facade is constructed with facing bricks and includes ample large glazing.
PROJECT OBJECTIVE:
Comprehensive thermal modernization of the B1 building
Our task was to conduct a thermal modernization of the B1 building. The project involved replacing all roof skylights and the building’s facade. All of these tasks had to be executed without disrupting the ongoing work inside the building. It was a challenging assignment that demanded a considerable amount of creativity, meticulous planning, and extensive experience.
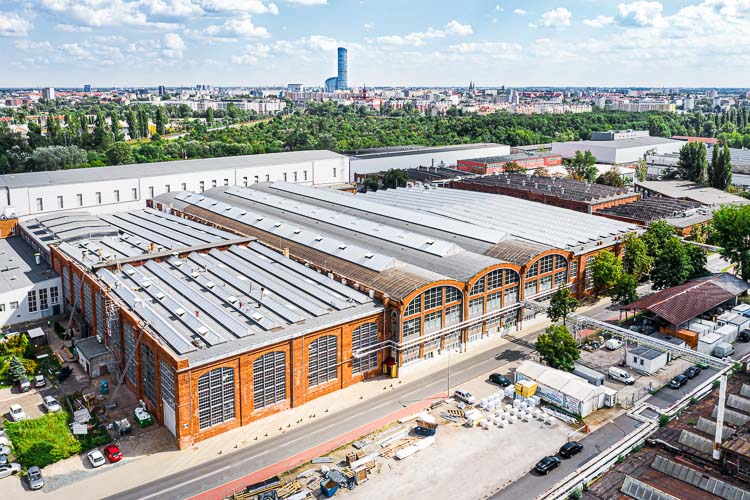
Stage I
The first stage involved replacing polygon skylights across the entire roof, encompassing both the narrower skylights in the end bays and the wider skylights in the three main central bays of the structure. Preserving the polygon shape of the skylight was essential; opting for continuous barrel vault skylights, a popular and economical choice, was not a viable option in this case.
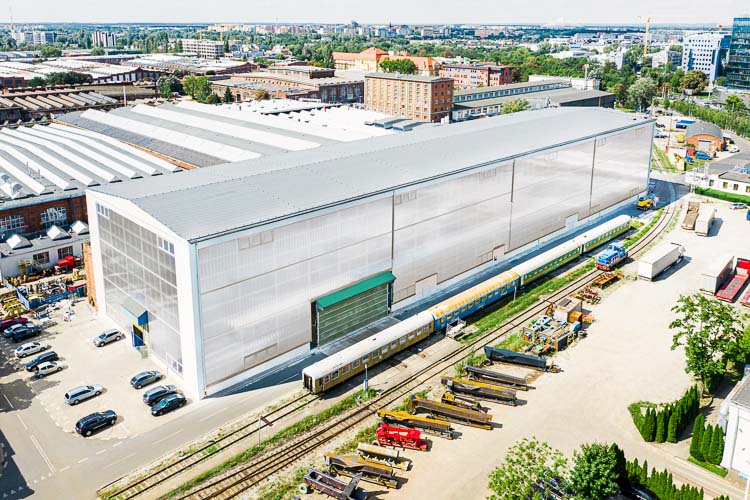
Stage II
The second stage involved upgrading the facade of one of the buildings in the complex. We installed a translucent polycarbonate facade using our proven system.
The Biggest Challenge
We would like to emphasize that the thermal modernization of this building was a challenging project that presented us with the following challenges:
- Large area of skylights and facades: We replaced a total of 6,860 m² of skylights and installed 5,000 m² of polycarbonate panels.
- Logistics: Handling such high quantities of materials required numerous systematic deliveries, which were further complicated by the considerable distance between Wrocław and Kielce – the headquarters of our company.
- Continuity of production: All roof-related work had to be carried out without interrupting the production processes inside the facility. This necessitated ensuring that the roof openings were 100% safe.
- Heritage conservation: The B1 building, like many others in the Wrocław Industrial Park, is a heritage structure, receiving constant protection as a historic site. Therefore, our skylights not only had to meet all applicable technical requirements but also could not interfere with the architectural concept of the building. Fortunately, our Aluco Skylight system was perfectly designed to meet this requirement, as will be discussed further in this article.
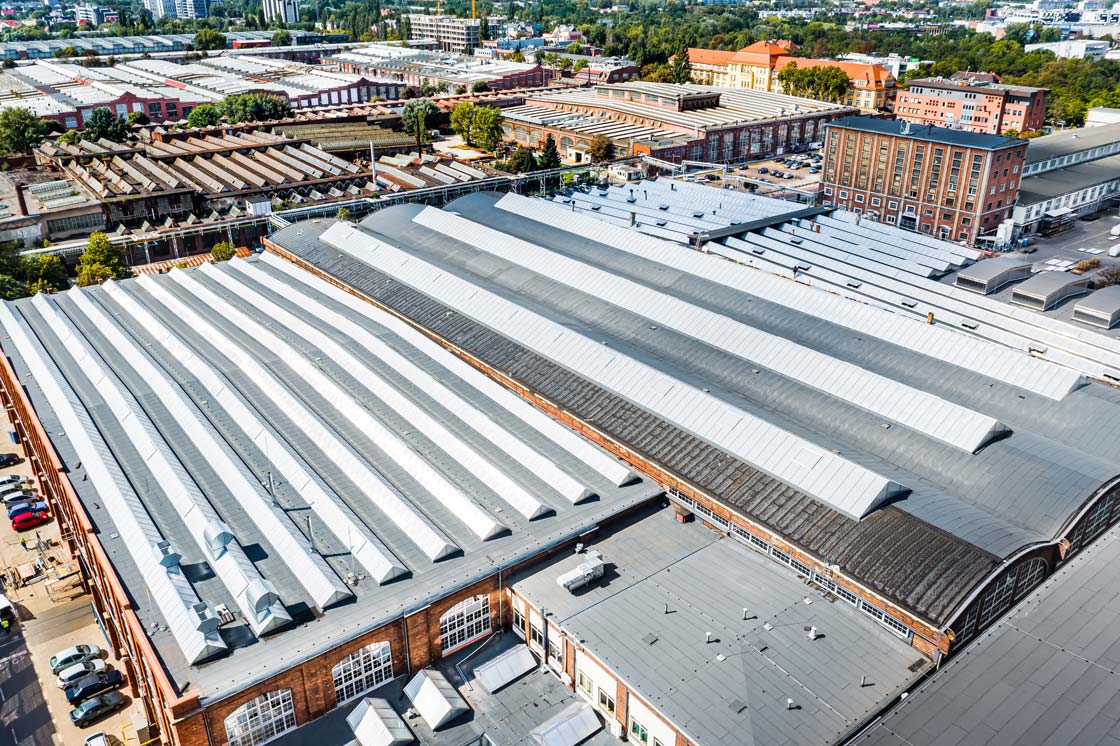
Applied Solutions
We implemented the project using our own systems, namely, Aluco Skylight polygon skylights and vents, as well as Aluco Panel polycarbonate facades.
ALUCO SKYLIGHT TR THERM
Thermally insulated polygon skylights
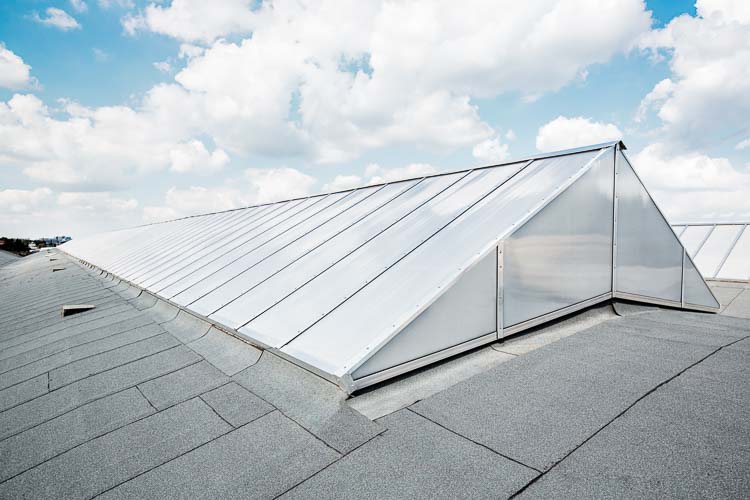
ALUCO PANEL
Polycarbonate facades with ventilation windows
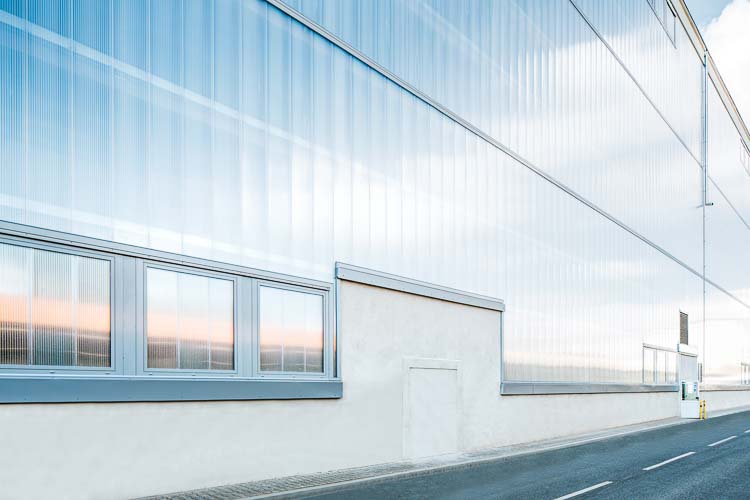
ALUCO SKYLIGHT AIR TR
Industrial vents dedicated to polygon skylights
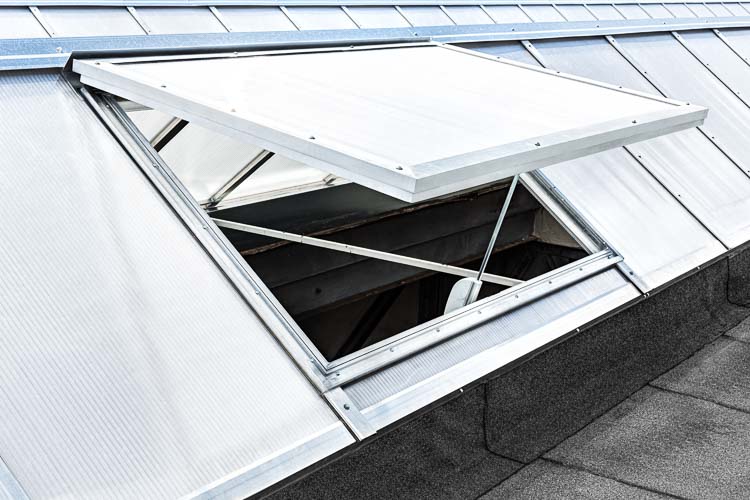
Initial condition
Saying that the existing skylights “could use a replacement” did not even begin to describe the situation. The picture below illustrates that the existing skylight was in urgent need of repair. It was the original skylight installed during the construction of the building at the beginning of the 20th century, indicating that it was certainly over 100 years old at the time of replacement.
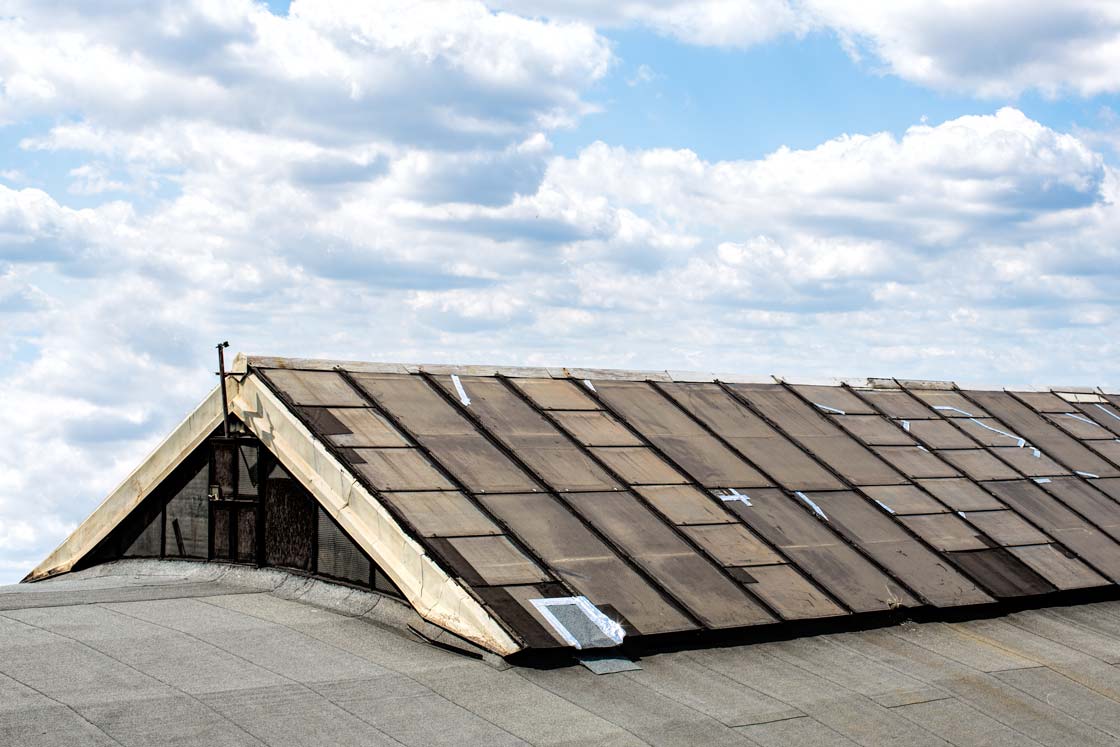
The skylights we encountered on the roof were made of thick wired glass, cracked, and patched in many places. Despite the lack of thermal insulation, the glass allowed very little light to enter. Consequently, the interior of the building was severely underlit. This created an unfavorable situation that adversely affected the working climate inside the building. The facade windows of the building we were tasked to work on were in a similar condition. Aluco System solutions were soon to change this!
Dozamel Case Study
Download PDF
Download the full version of the "Dozamel Case Study" article as a PDF file to your device.
Implementation Of The Project
PART II
Let’s reiterate the purpose of the entire project: “Comprehensive thermal modernization of roof skylights and facade of building B1,” with emphasis on the term “comprehensive.” At our company, comprehensive implementation of a project means minimizing the client or project owner’s involvement in coordinating the project. Aluco System takes responsibility for organizing and implementing as many tasks as possible, extending beyond those directly related to the installation of our products.
Such was our approach to this project. In practice, this meant that our company took responsibility for the dismantling and disposal of existing roof skylights and facade components, ensuring the protection of the work site, and installing new roof skylights and facades. If the client required it, we could also undertake roof repairs.
To fulfill all these tasks, we took the following steps:
- Material logistics
- Dismantling existing roof skylights and preparing the facade
- Protecting the roof to avoid interruptions in the production processes inside the building
- Stage I – installation of new roof skylights
- Stage II – installation of a new polycarbonate facade
- Removal and disposal of waste.
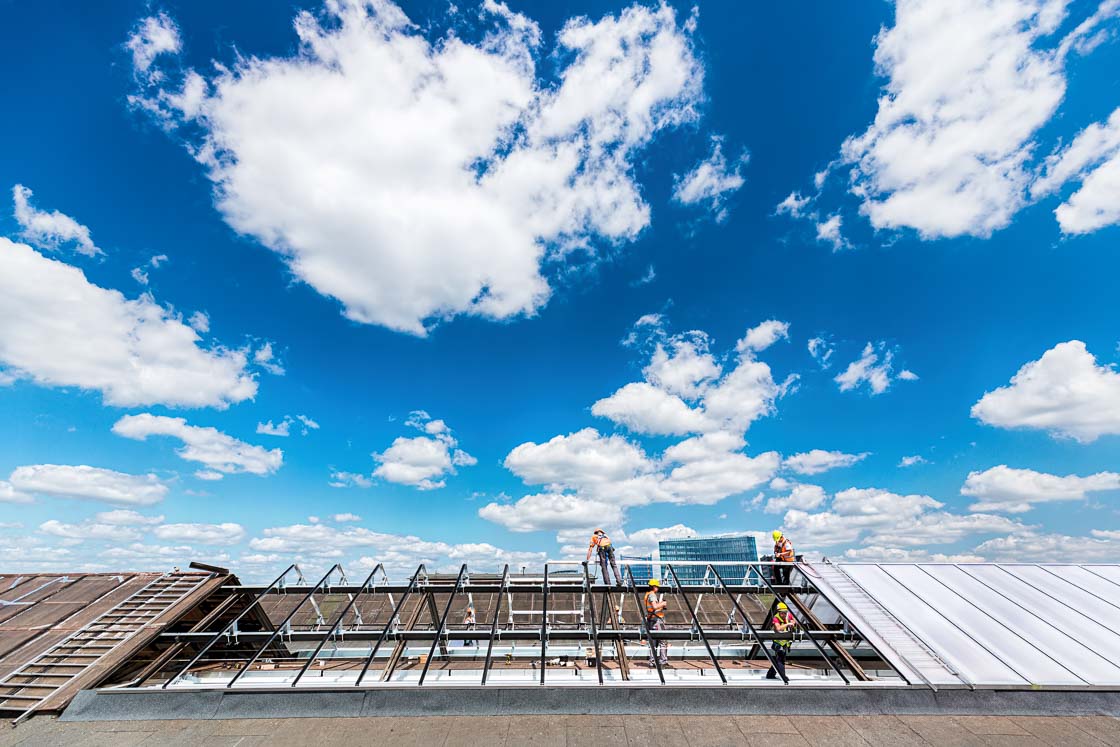
Material Logistics
To face this challenge, we had to carefully consider and precisely arrange all details connected with material deliveries. By maintaining a sufficiently high inventory of intermediate products – in this case, aluminum profiles – we were able to adjust the delivery dates of finished skylight structures for the individual stages to the dates specified in the contract.
The polycarbonate panels used as glazing for the skylights were supplied by a factory in the Czech Republic. The contract stipulated the delivery of ready-to-install polycarbonate panels, cut to size and wrapped with sealing tape. Thanks to this arrangement and the short distance from the production plant to the project site in Wrocław, we not only achieved additional savings but were also able to deliver all components to the site on time.
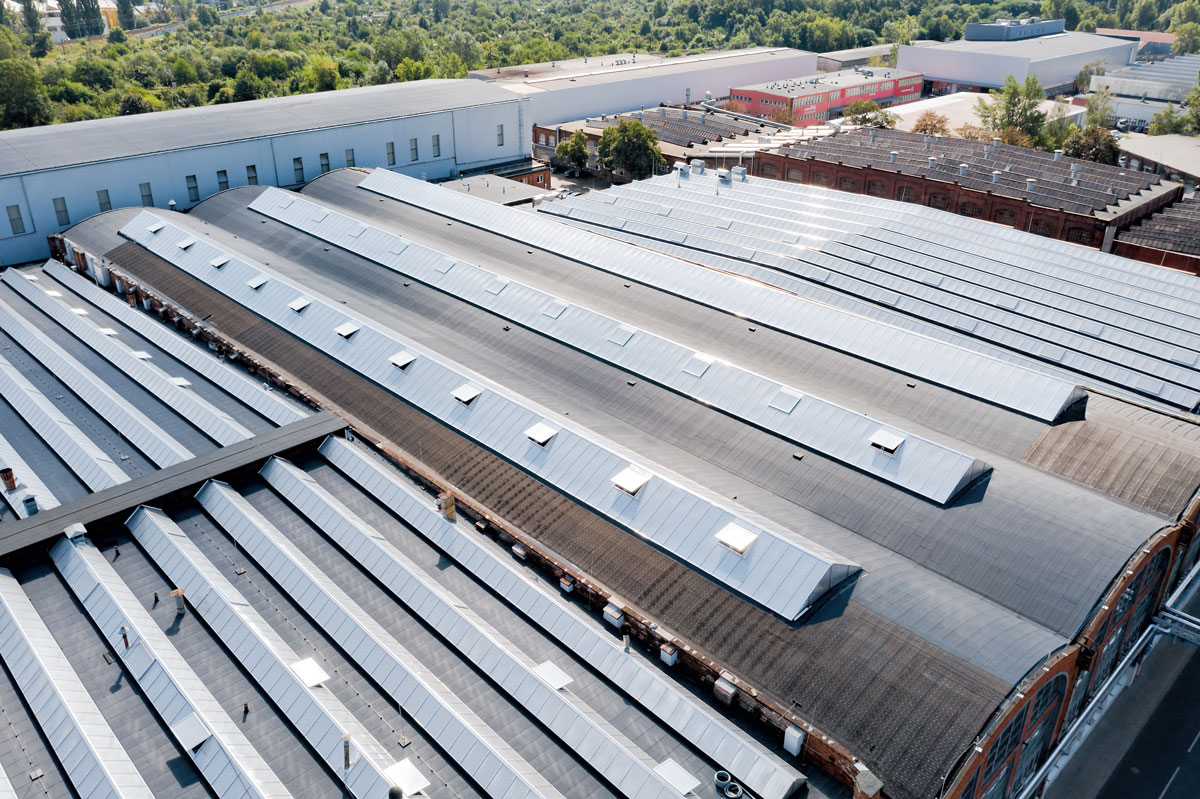
Dismantling of Existing Roof Skylights
We began the dismantling of existing skylights by establishing routes for the horizontal movement of the dismantled materials. OSBs were arranged along the skylights to transport the dismantled glass and the steel structure. The next step involved cleaning the remaining steel structure and protecting it against corrosion. During these works, the surfaces under the skylights were appropriately shielded to prevent the installation crew or dismantled components from falling.
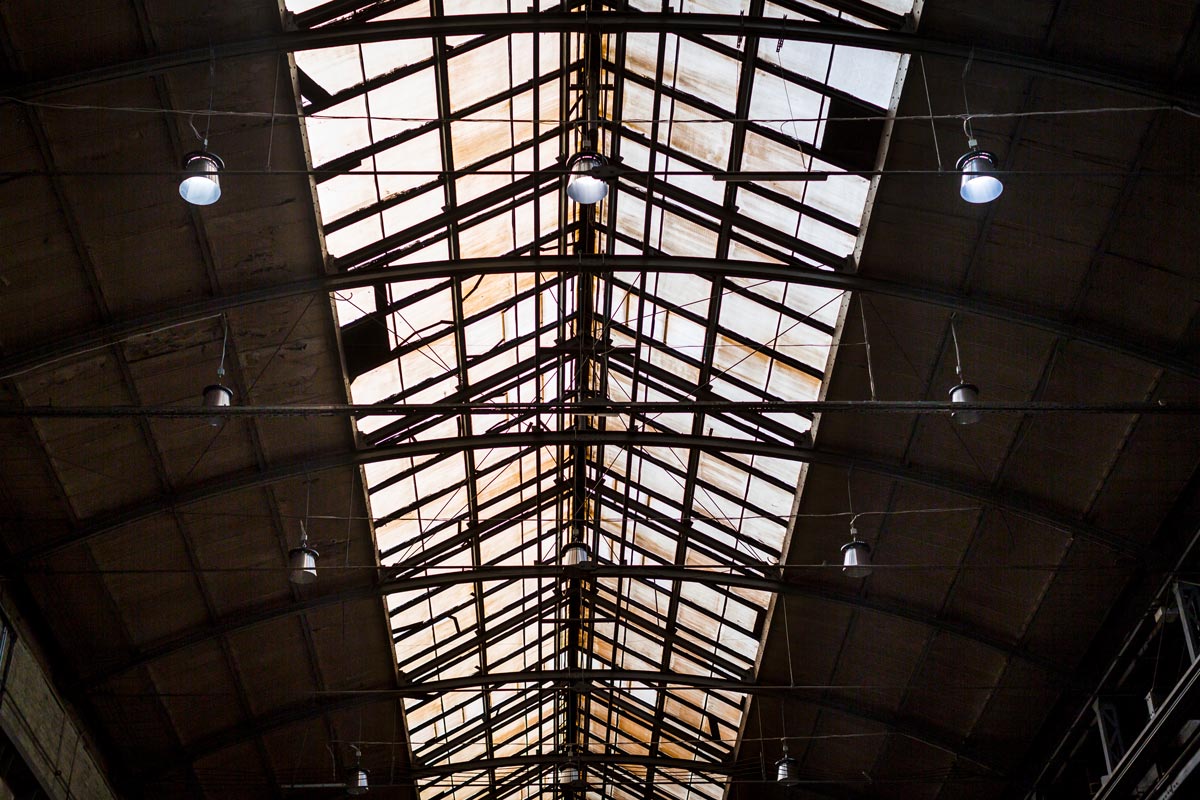
Safety
Protecting the work site was one of the significant challenges in this project, primarily because of the large area of the building and the necessity to safeguard the roof openings without disrupting the ongoing work inside the building. At Aluco System, we prioritize safety and strictly adhere to applicable Occupational Health and Safety (OHS) codes.
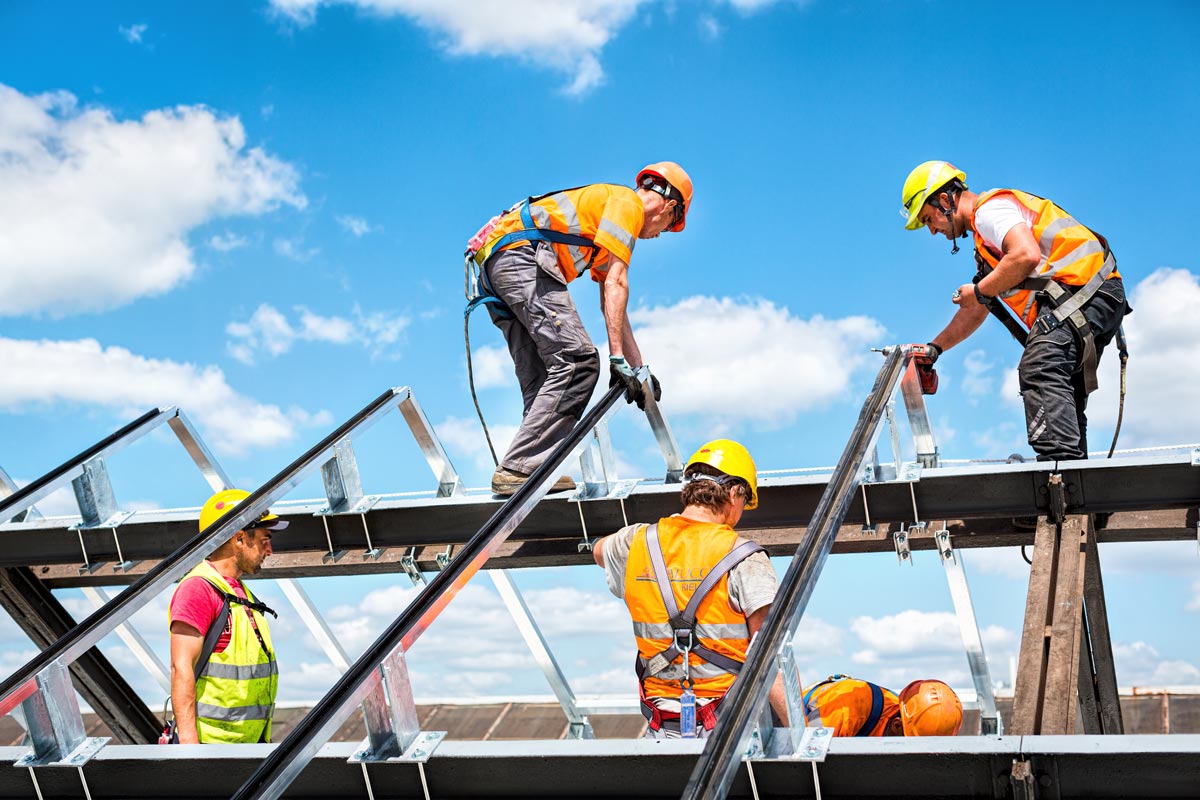
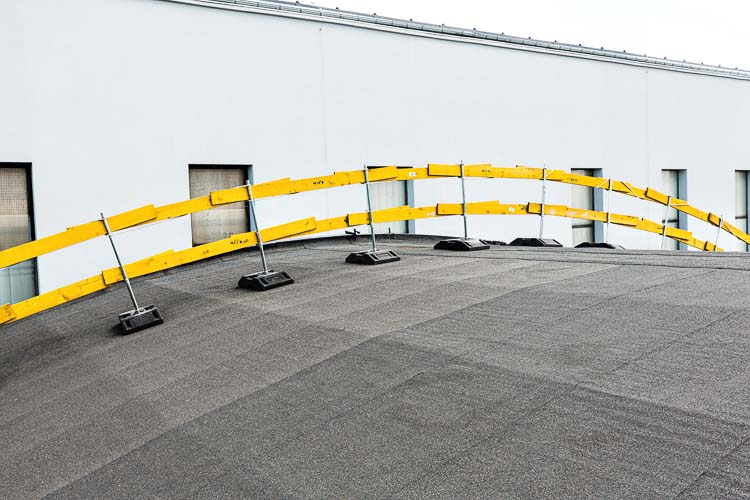
Works at height
The working area on the roof, where individual dismantling and installation works were carried out, was enclosed and safeguarded with railings that we delivered to the project site. Our employees use safety harnesses when working at heights. Additionally, we protected all roof openings during the installation of new skylights. This measure ensured the safety of personnel on the roof and eliminated the risk of accidentally dropping tools, parts, and small items into the building.
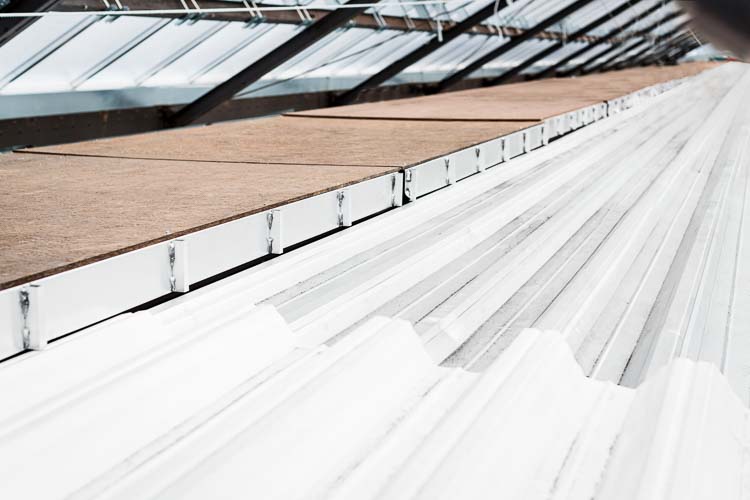
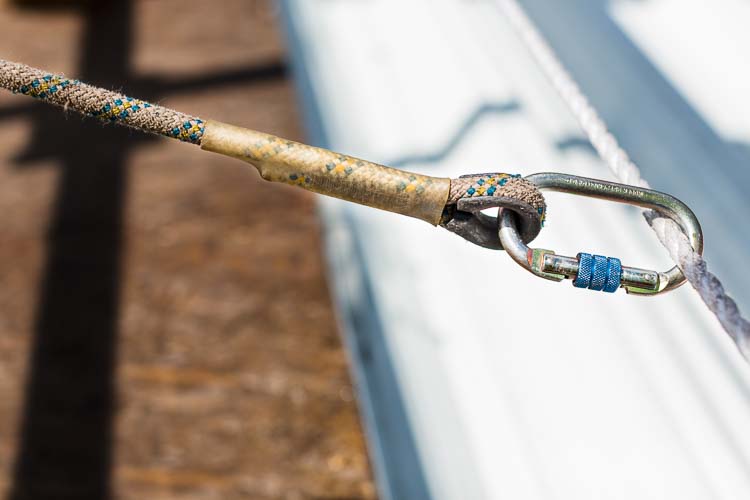
Protection of the main skylight
In terms of ensuring the safety of installation works, the most significant challenge we had to address was how to safeguard the three largest roof openings in the central bays of the main section of the B1 building. With the skylight measuring 8.00 m in length, it was necessary to install an additional support structure along its entire length to facilitate the installation of troughed sheets and OSBs, providing protection for the surfaces beneath the skylight. Thanks to such a well-thought-out structure, we could also move swiftly and safely across the entire surface of the roof opening. The task was further complicated by the 80-meter length of the skylight and the requirement to secure the entire roof opening before commencing the next stage of the works.
No interruptions in production
It was essential to diligently protect the roof openings throughout the entire duration of thermal modernization works, in adherence to an additional condition imposed by the project owner. All activities had to be executed without disrupting the production processes inside the building. While challenging to meet, this requirement was entirely justified. In a facility engaged in advanced industrial production, any delay, even by a day or an hour, could lead to financial losses, contractual sanctions, etc. We successfully fulfilled this condition, with the only noticeable impact being the limitation of daylight admission during our installation works.
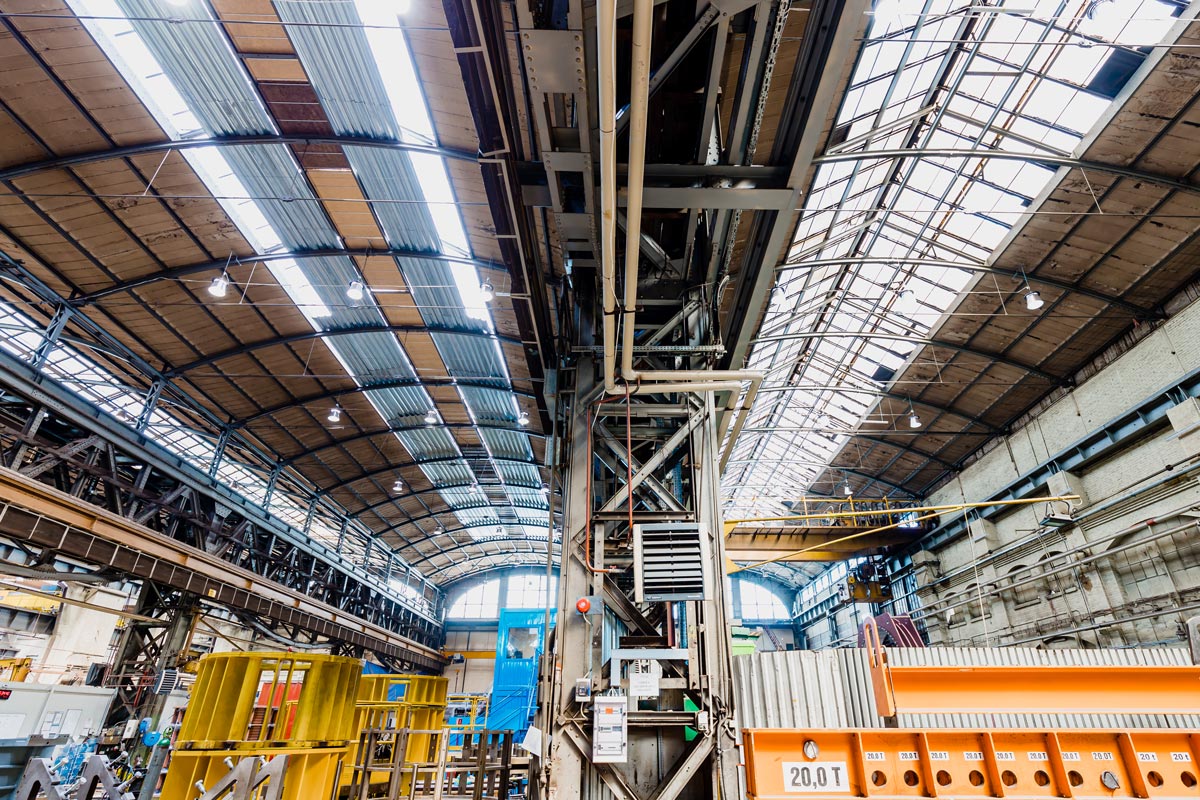
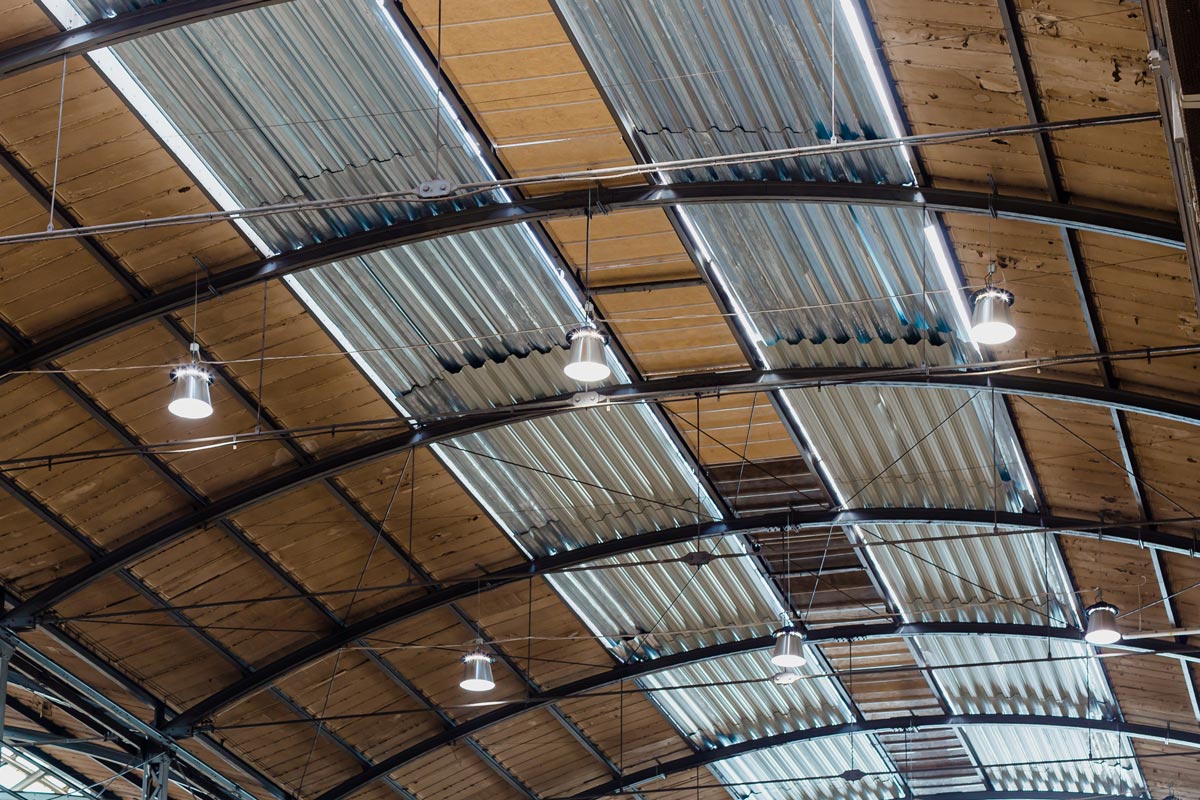
Implementation of Stage I
THERMAL MODERNIZATION OF SKYLIGHTS
The first stage of the project involved replacing the roof skylights throughout the entire facility. The building covers an area of 26,000 m2, and all roof skylights needed upgrading. The illustration below vividly depicts the considerable amount of work we had to undertake. Following the principle that “there is only one way to eat an elephant: a bite at a time,” we divided the entire first stage into three parts. We successively upgraded the skylights at both ends of the building and left the three largest skylights in the central bays of the building for the final phase.
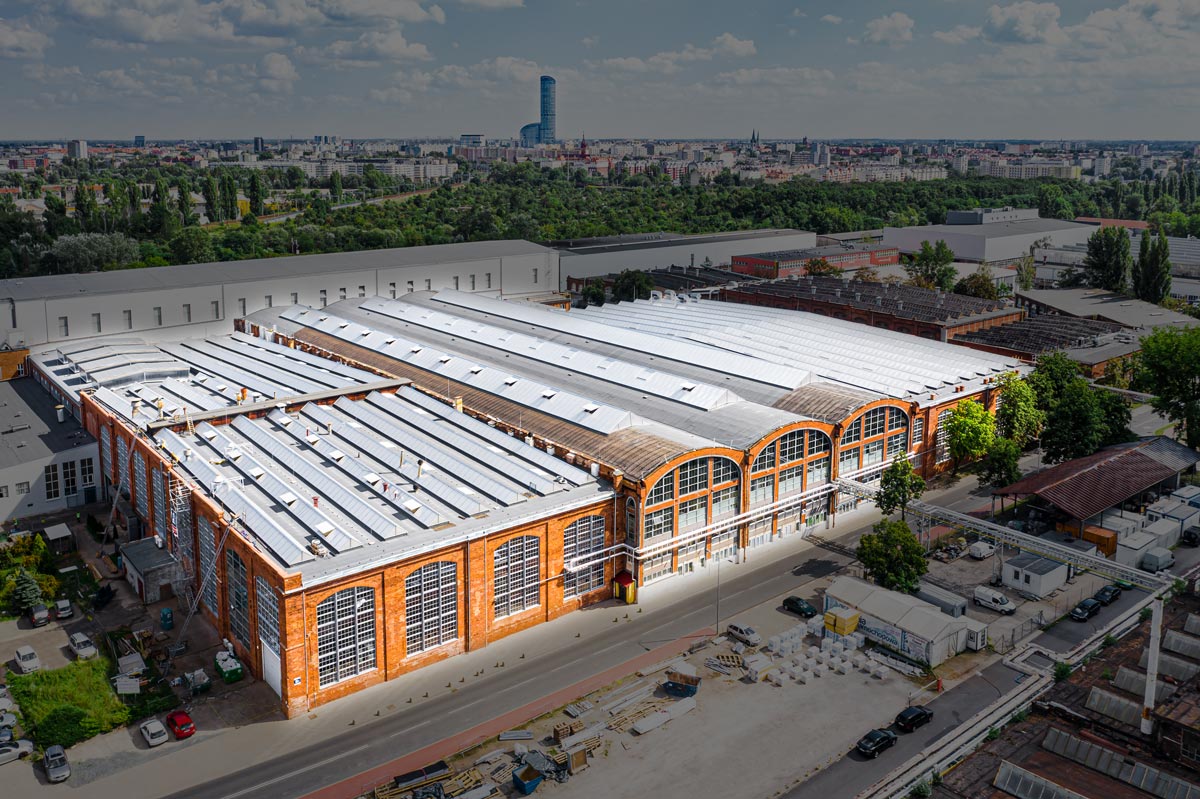
All skylights on the roof of the B1 building take the form of continuous polygon skylights. It should be noted that the entire B1 structure has been under conservation as a heritage site for many years. Therefore, one of the project’s requirements was to preserve the architectural form of the skylight, including its original shape. At Aluco System, we have a product designed specifically for such situations – the Aluco Skylight TR Therm thermally insulated roof skylight.
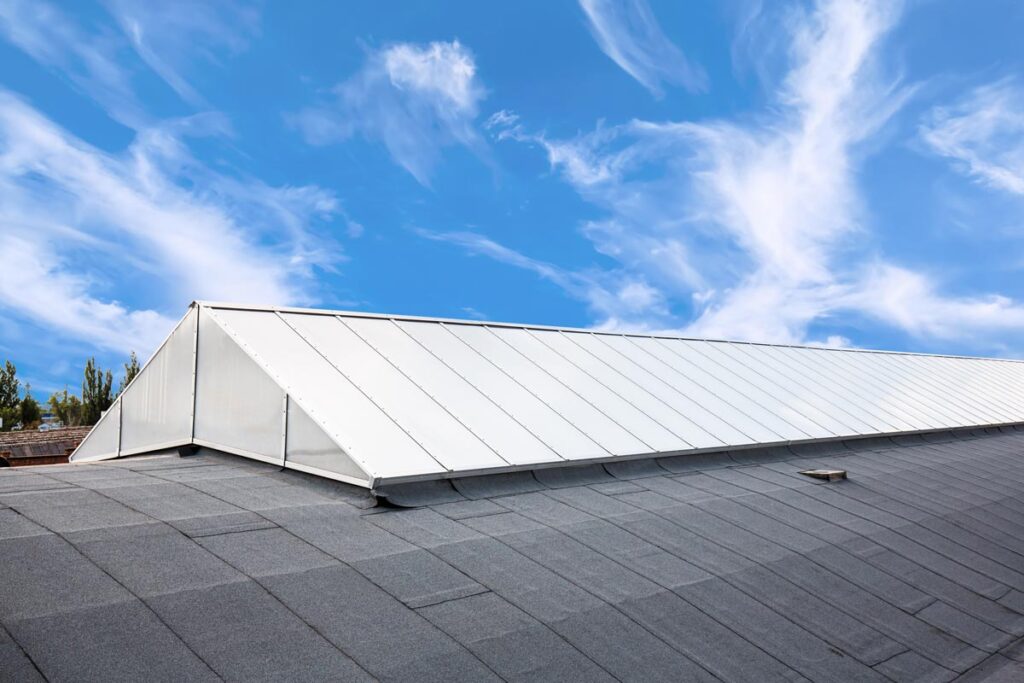
ALUCO SKYLIGHT TR THERM
POLYGON SKYLIGHTS WITH THERMAL INSULATION
The ALUCO SKYLIGHT TR THERM polygon skylight system is an innovative solution designed for heritage industrial facilities, preserving the historic character thanks to the polygon shape. It offers thermal insulation to help save energy. The system conforms to European standards and boasts a very low heat transfer coefficient of U = 0.5 W/(m²K).
Skylight dimensions
The ALUCO SKYLIGHT TR THERM continuous polygon skylight is manufactured to custom dimensions, with a width (span) range of our product extending from 1,000 mm to 4,000 mm. Additionally, the utilization of a steel support structure allows us to create industrial roof skylights with a span of up to 14 meters.
In the discussed project, we fabricated continuous skylights with a width of 8,000 mm for the narrower skylights in the end bays and three continuous skylights with a width of 3,000 mm in the main bays of the building.
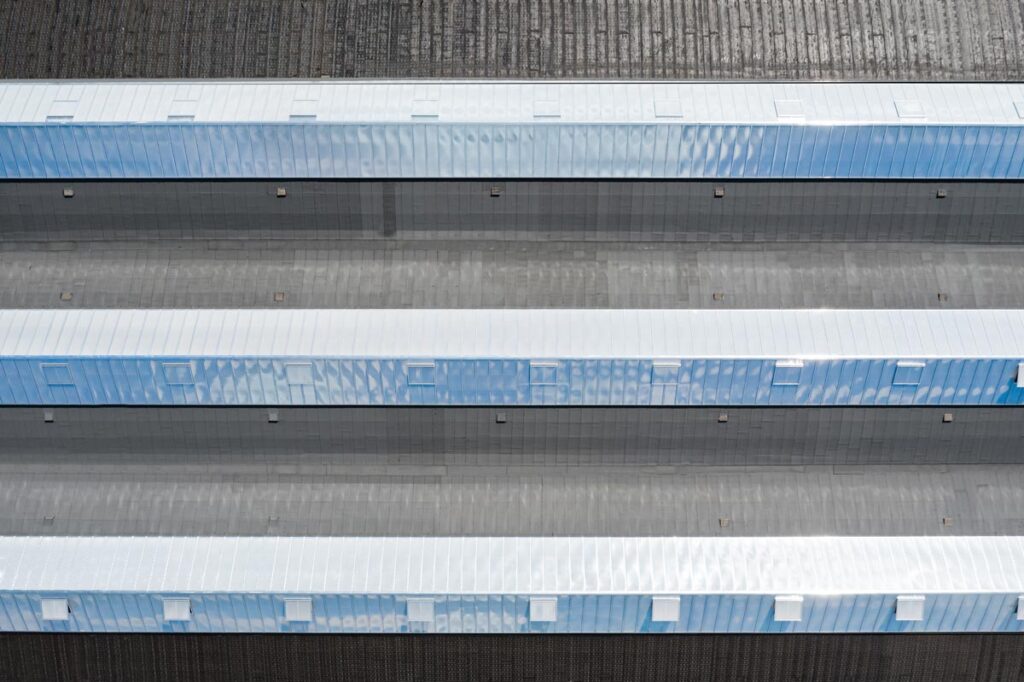
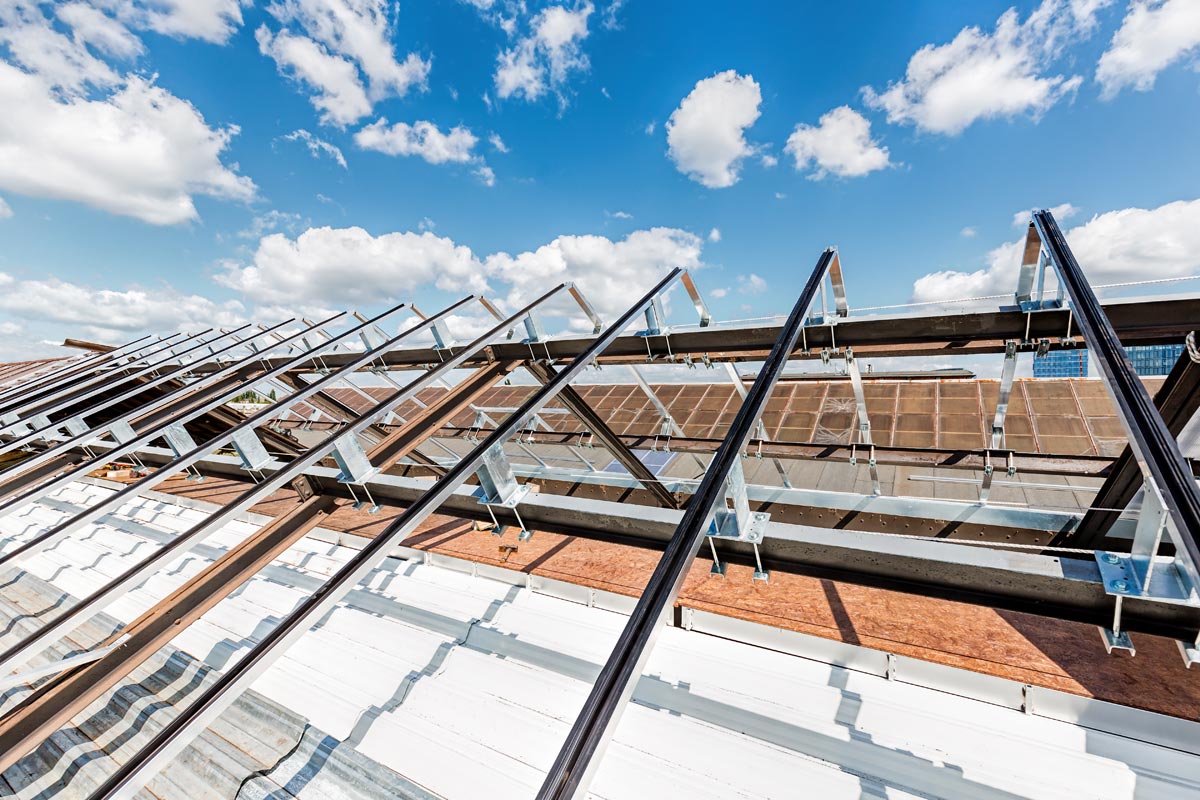
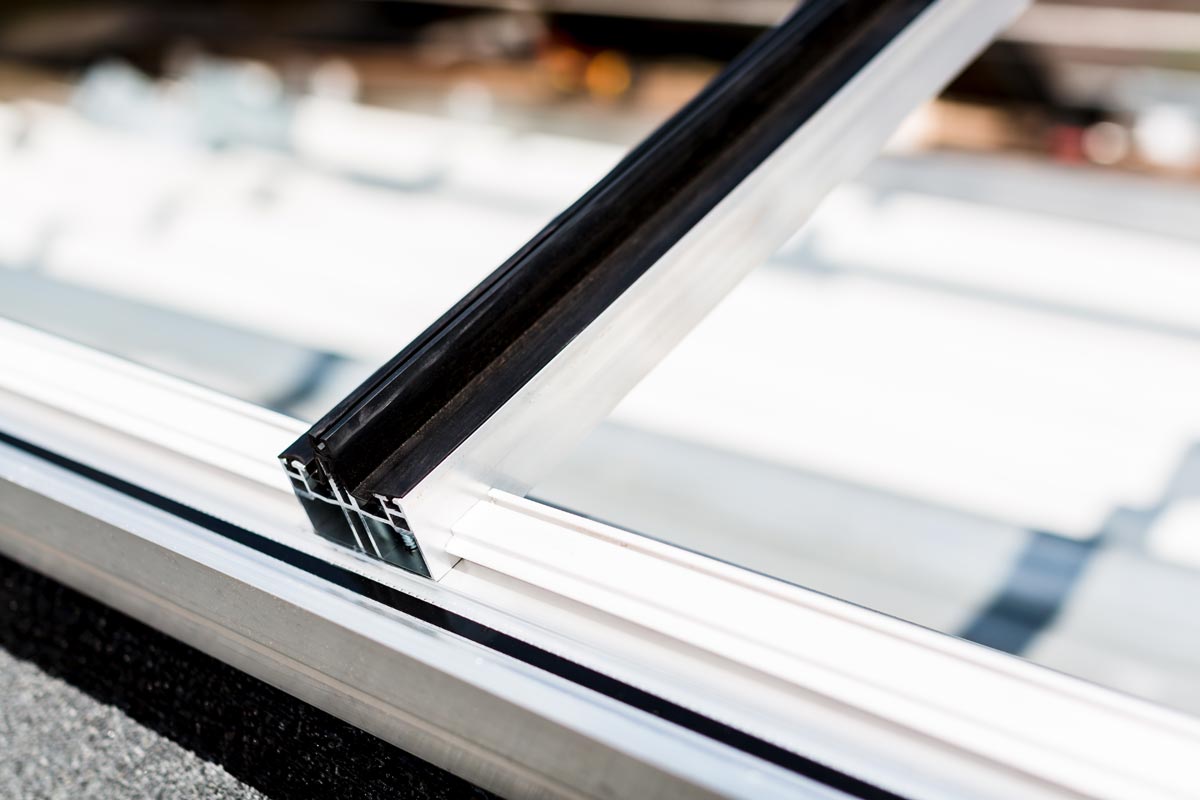
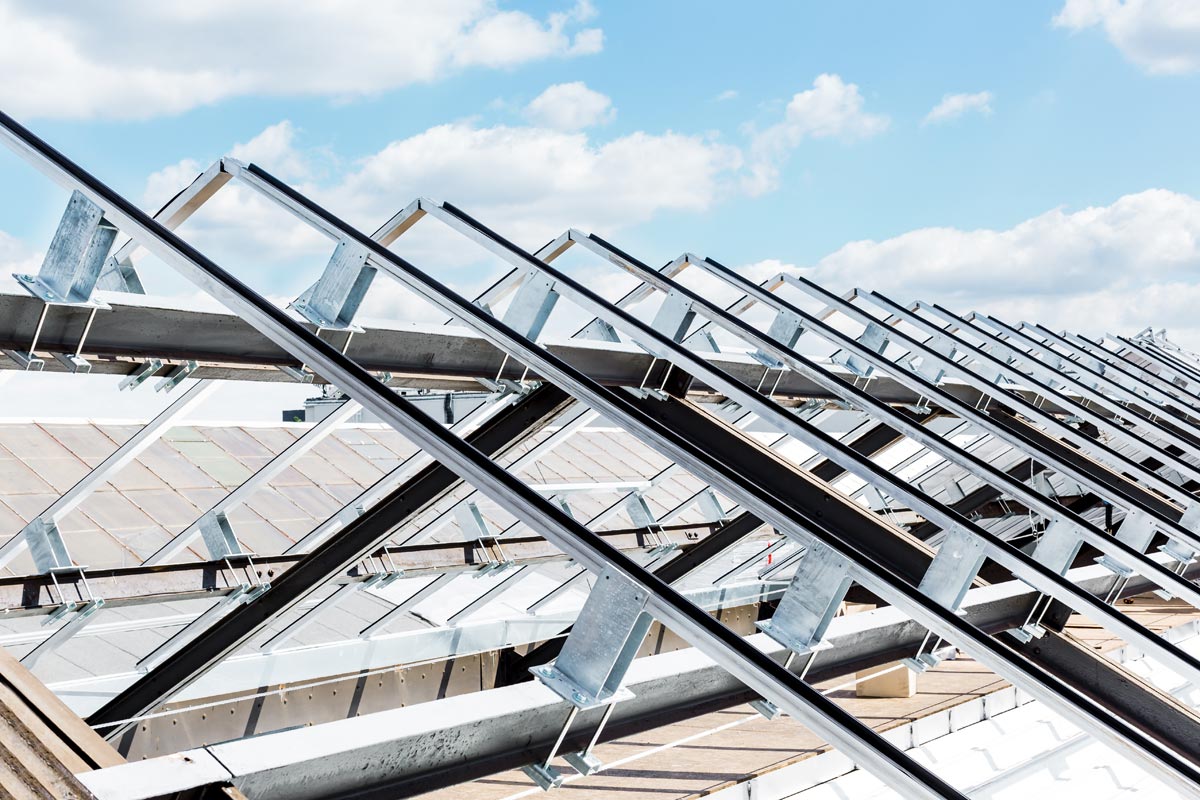
Thermal insulation
Effective thermal insulation is a key advantage of our ALUCO SKYLIGHT TR THERM roof skylights. The continuous skylights on the roof of the B1 building have been safeguarded against thermal bridges through the use of aluminum insulation profiles, known as thermal breaks, installed in each skylight. Additionally, the load-bearing profiles of the skylights were equipped with thermal insulation gaskets to prevent condensation from infiltrating the building.
The bottom profile of the skylight also features an insulating gasket along its entire length. Furthermore, an additional profile is integrated between the individual ribs of the skylight’s bottom profile to enhance the thermal insulation of the entire system.
Vents
All continuous skylights have been provided with vents.
Aluco Skylight Air vents are designed for installation in continuous barrel vaults and polygon skylights. They represent a new addition to our Aluco Skylight roof skylight system, serving the purpose of providing daily ventilation.
The vents are installed in continuous skylights, facilitating effective daylighting of the interior space and ensuring proper air circulation. This, in turn, significantly influences indoor air quality, enhancing the comfort and working efficiency of the users within the industrial facility.
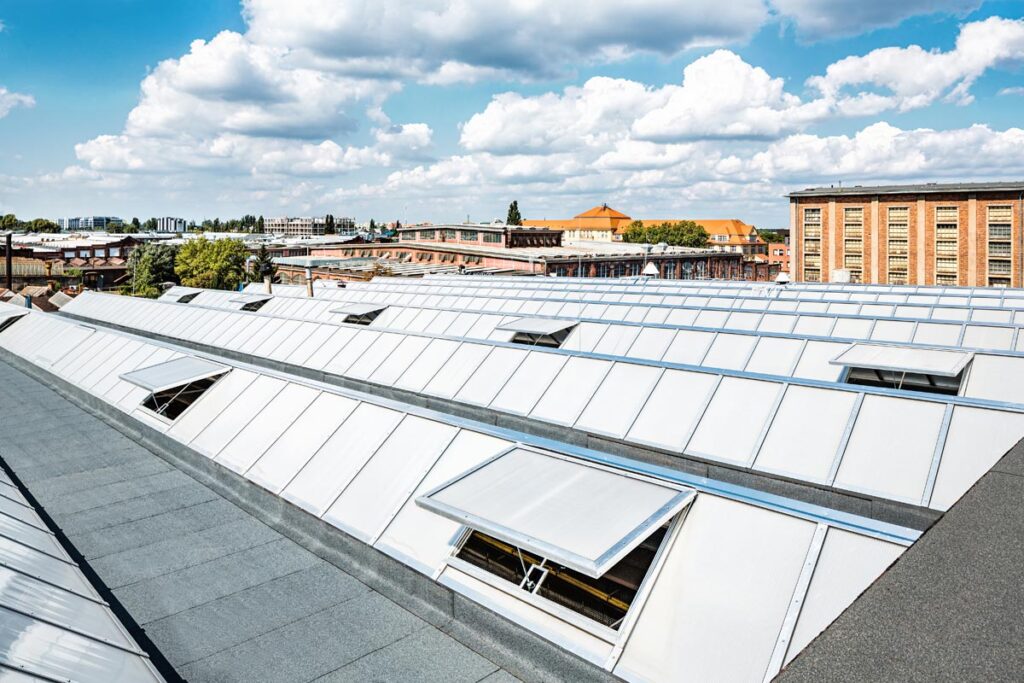
Explore Aluco Skylight TR Therm
Work schedule and performance of the works
The following measures were implemented to adhere to the work schedule:
- Protecting the surface beneath the dismantled skylights. One of the obvious objectives of this stage was to ensure the safe work of Aluco System installation crews during the dismantling works and installation of new skylights and to enable safe work inside the building in the space directly under the skylights. Throughout our operations, work in the renovated building proceeded without any interruptions
- Skylight installation followed a specific rule: the quantity of dismantled skylights equaled the quantity of newly installed skylights. This approach mitigated the potential adverse impact of rainfall on the working area.
- For installation works, we utilized special aluminum walkways. The aluminum grating, designed by the technical department of Aluco System, took the form of walkways with supports placed at 9 m intervals and a width of 0.9 m, facilitating the convenient and swift installation of the troughed sheets to protect the skylight surface.
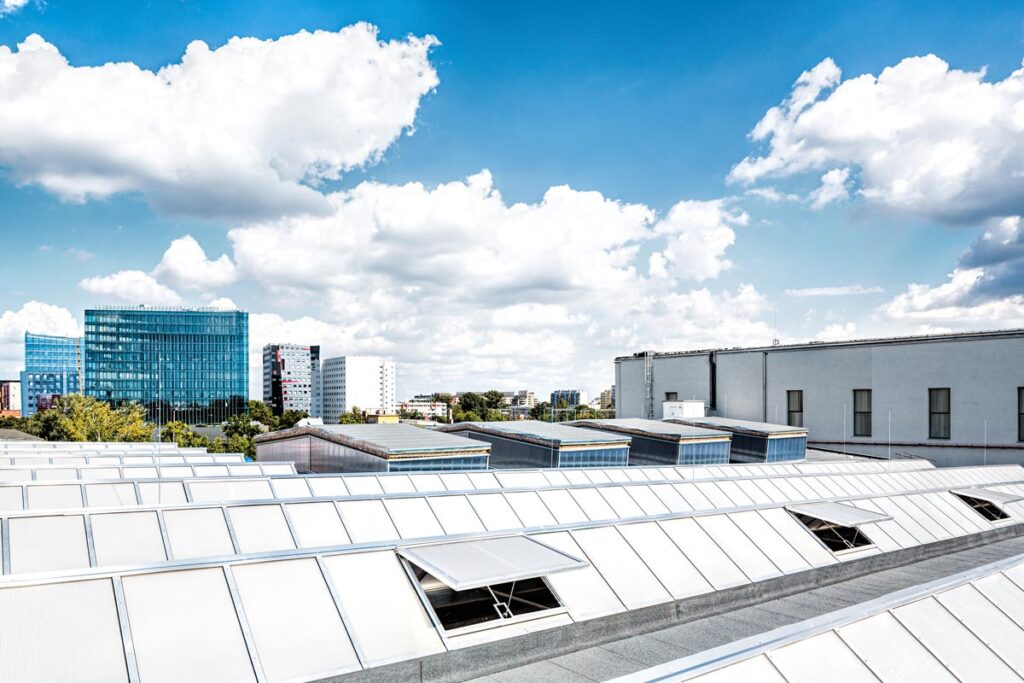
Northern part: 11/2019 – 1/2020
Roof skylights: ALUCO SKYLIGHT TR THERM
Dimensions: 3,000 mm x 40,000 mm
Quantity: 8 pcs.
Heat transfer coefficient: U = 1.1 W/m2K
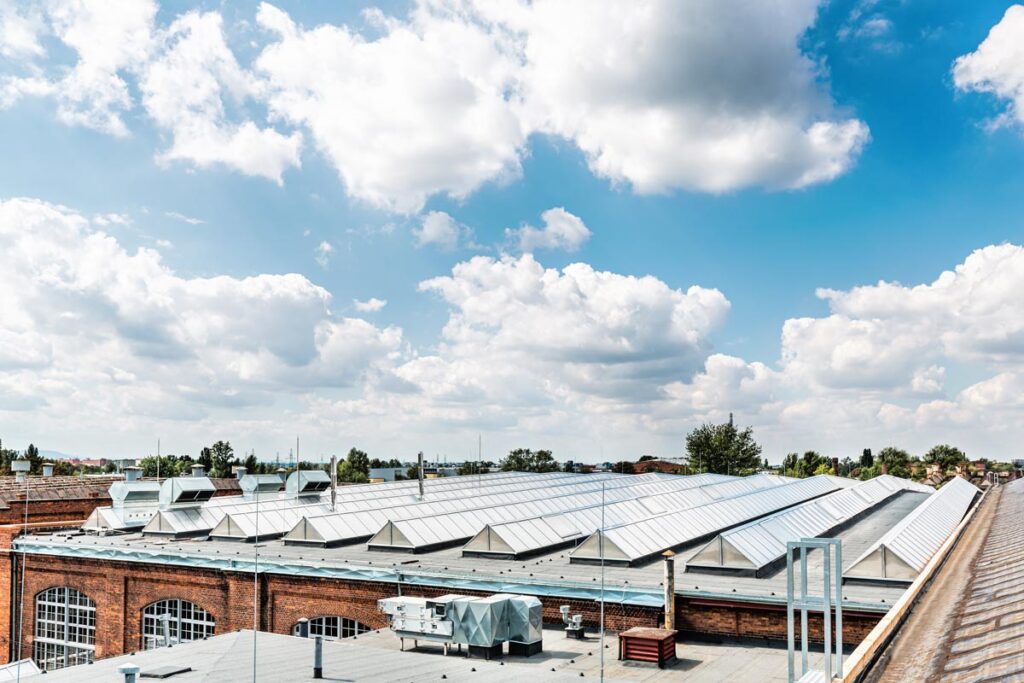
Southern part: 7/2020–7/2020
Roof skylights: ALUCO SKYLIGHT TR THERM
Dimensions: 3,000 mm x 40,000 mm
Quantity: 9 pcs.
Heat transfer coefficient: U = 1.1 W/m2K
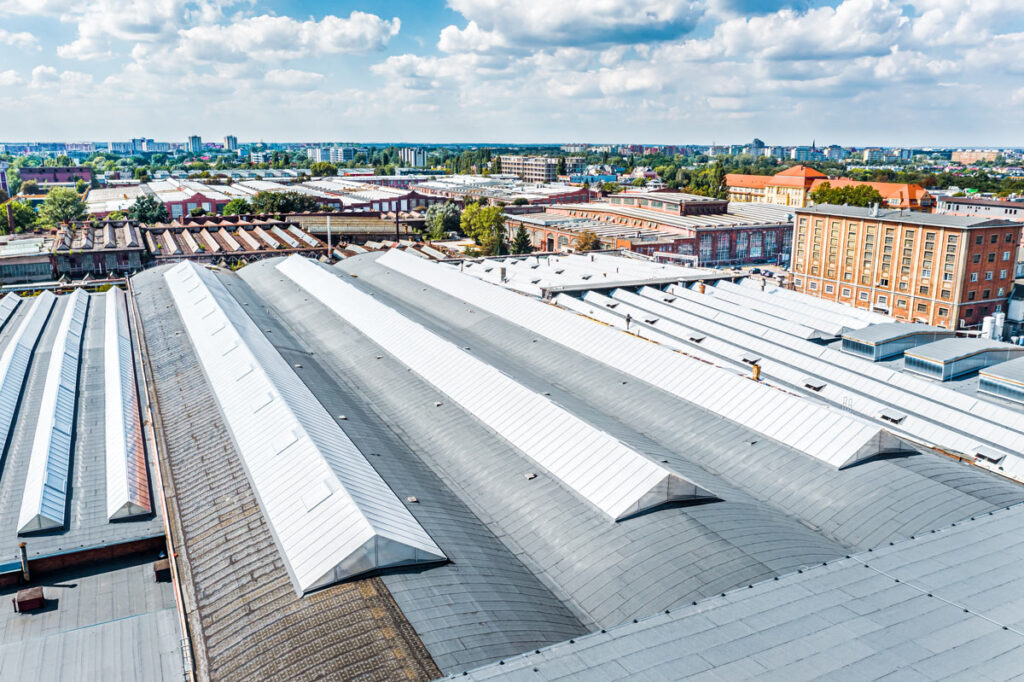
Central part: 5/2020–9/2020
Roof skylights: ALUCO SKYLIGHT TR THERM
Dimensions: 8,000 mm x 108,000 mm
Quantity: 3 pcs.
Heat transfer coefficient: U = 1.1 W/m2K
Dozamel Case Study
Download PDF
Download the full version of the "Dozamel Case Study" article as a PDF file to your device.
Implementation of Stage II
THERMAL MODERNIZATION OF THE FACADE
During the second stage of our project, we initiated the upgrade of a section of the building facade, opting to utilize ALUCO PANEL polycarbonate panels as the primary filling material. This enhancement specifically targeted the production section of the B1 building, as illustrated in the picture below.
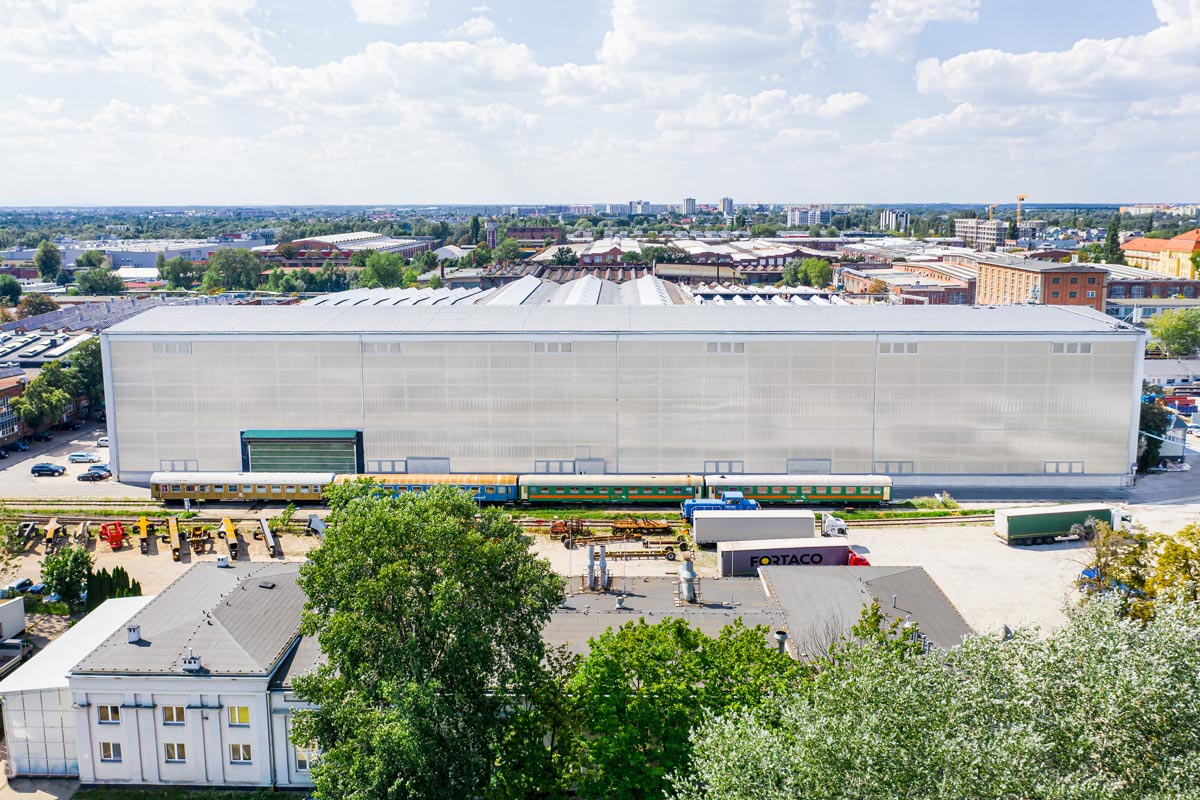
Before the upgrade, the facade of building B1 consisted of a combination of wired glass and double-glazed polycarbonate panels, all set in uninsulated steel profiles.
The heat transfer coefficient for such a facade ranged from 3.5 W/m²K to 5.5 W/m²K. As a result, the thermal performance of the facade deviated significantly from contemporary standards, leading to substantial heat losses and, consequently, high expenditures on the heating of the building.
ALUCO PANEL AP 50
We proposed installing a new facade using the ALUCO PANEL AP 50 system. The system comprises 50-mm polycarbonate panels with a heat transfer coefficient of U= 0.9 W/m²K, set in thermally insulated aluminum profiles.
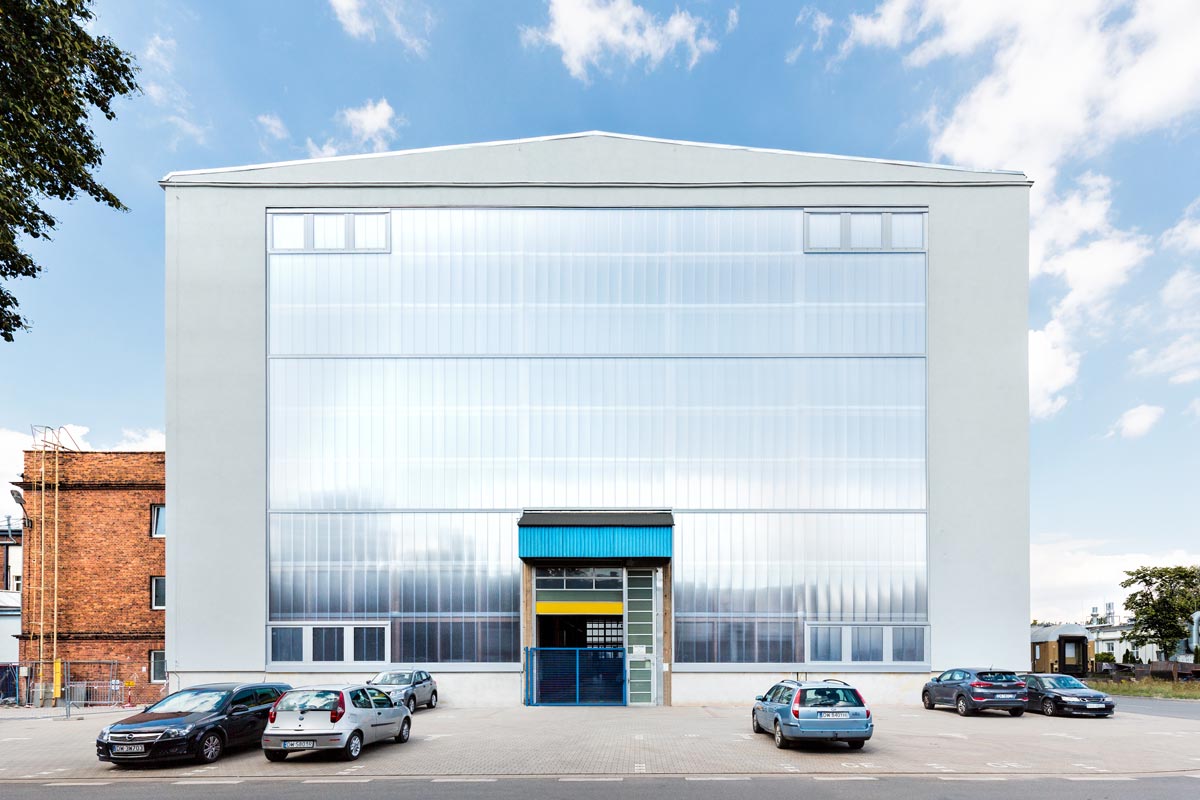
ALUCO PANEL
POLYCARBONATE FACADE
ALUCO PANEL is an innovative and durable system of polycarbonate facades that exhibit resistance to weather conditions, UV radiation, and chemical factors. These panels are robust, impact-resistant, and easy to install. Polycarbonate is frequently employed in the construction industry as a material for facades, roofs, and space dividers. Our translucent polycarbonate panels are particularly well-suited for use in storage buildings, production facilities, and public structures.
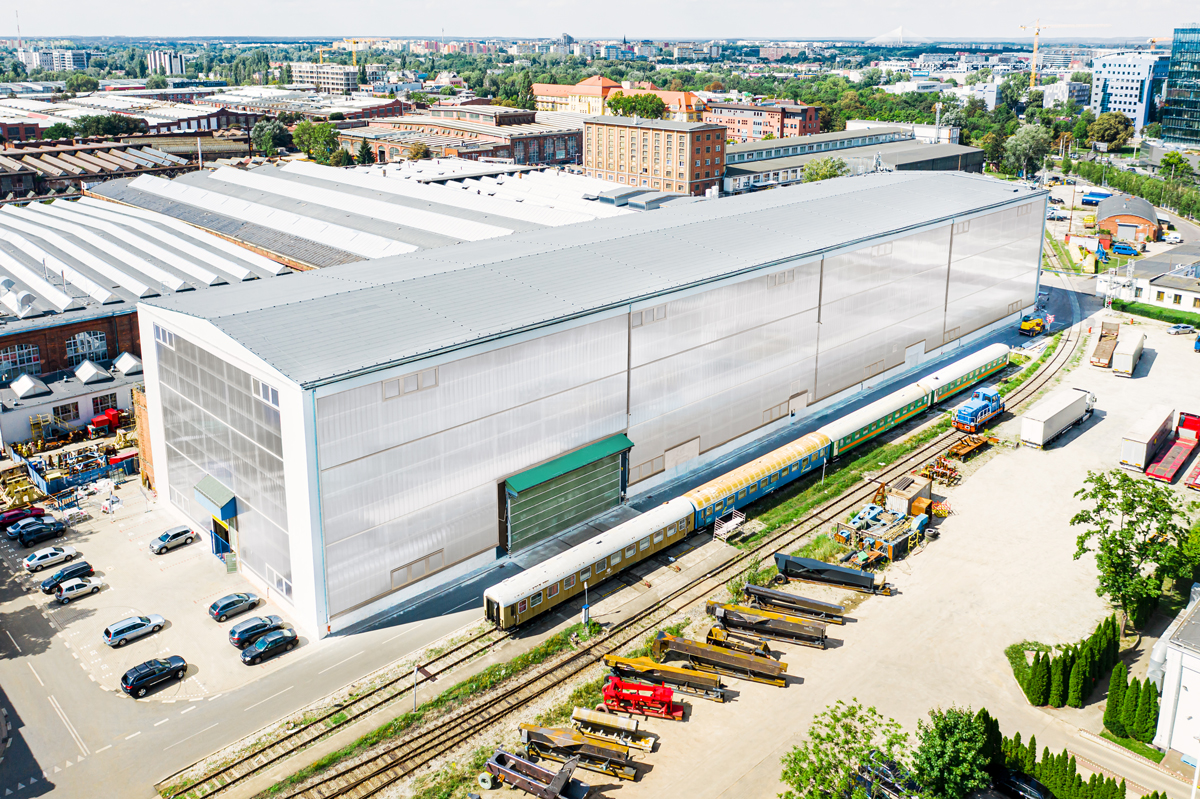
The installation of polycarbonate panels
The area of the renovated facade was 5,000 m². The challenge arose from the building’s height of 19.5 m and the difficulty of accessing the end bays. This issue was addressed by employing a specialized telescopic boom lift with an outreach of 53.0 m. From its basket, the installation crew could safely carry out the installation works.
To adhere to the work schedule, it was crucial to procure professional telescopic boom lifts and platforms. This equipment facilitated the safe and efficient dismantling of the existing facade and the installation of the new facade.
Similarly to the thermal modernization of the skylights on the roof of the building, the building operated continuously during the thermal modernization of the facade.
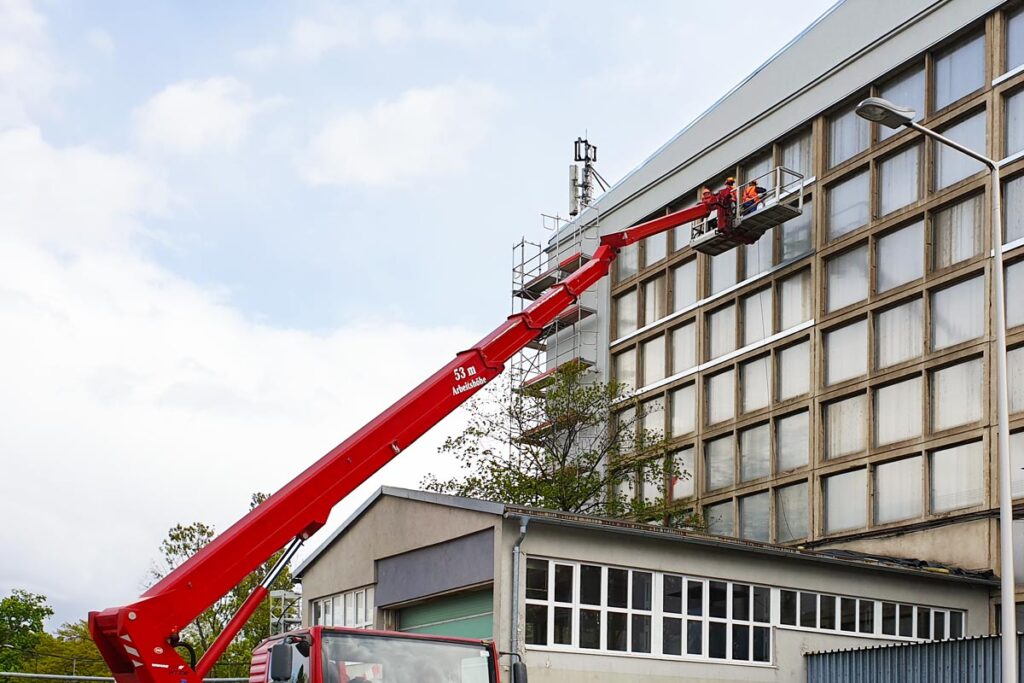
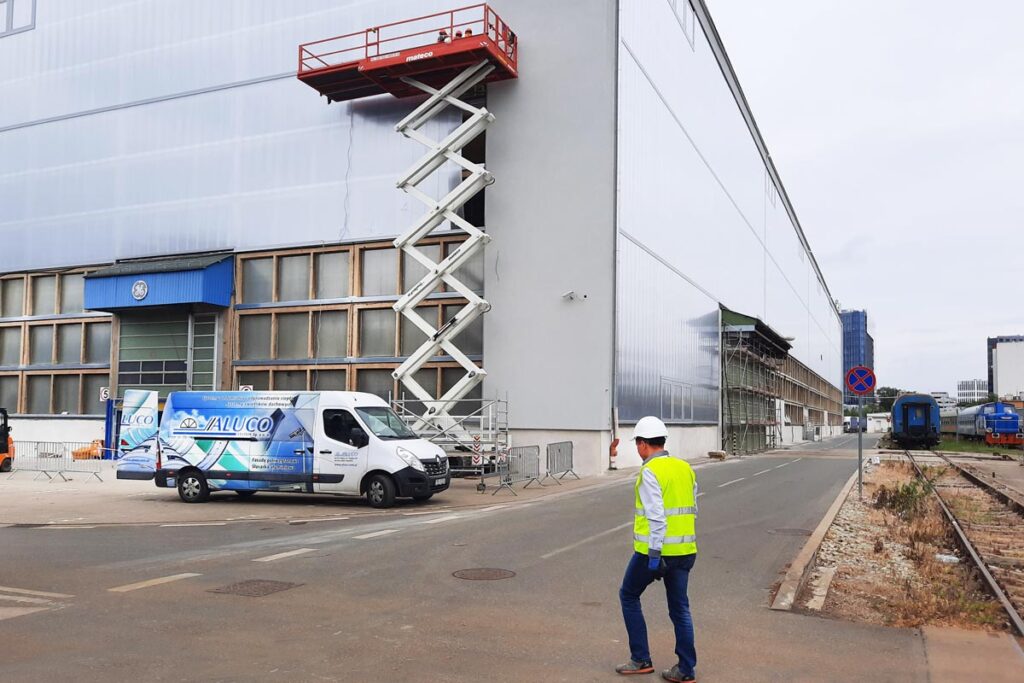
Performance of the works
The first stage involved the installation of the support structure made from cold-formed steel profiles. Subsequently, we installed aluminum perimeter profiles with expansion joints. The next step was the gradual dismantling of the existing glazing, and we covered the dismantled surfaces by installing new polycarbonate panels to eliminate rain from falling into the building during work interruptions (such as at night and on weekends).
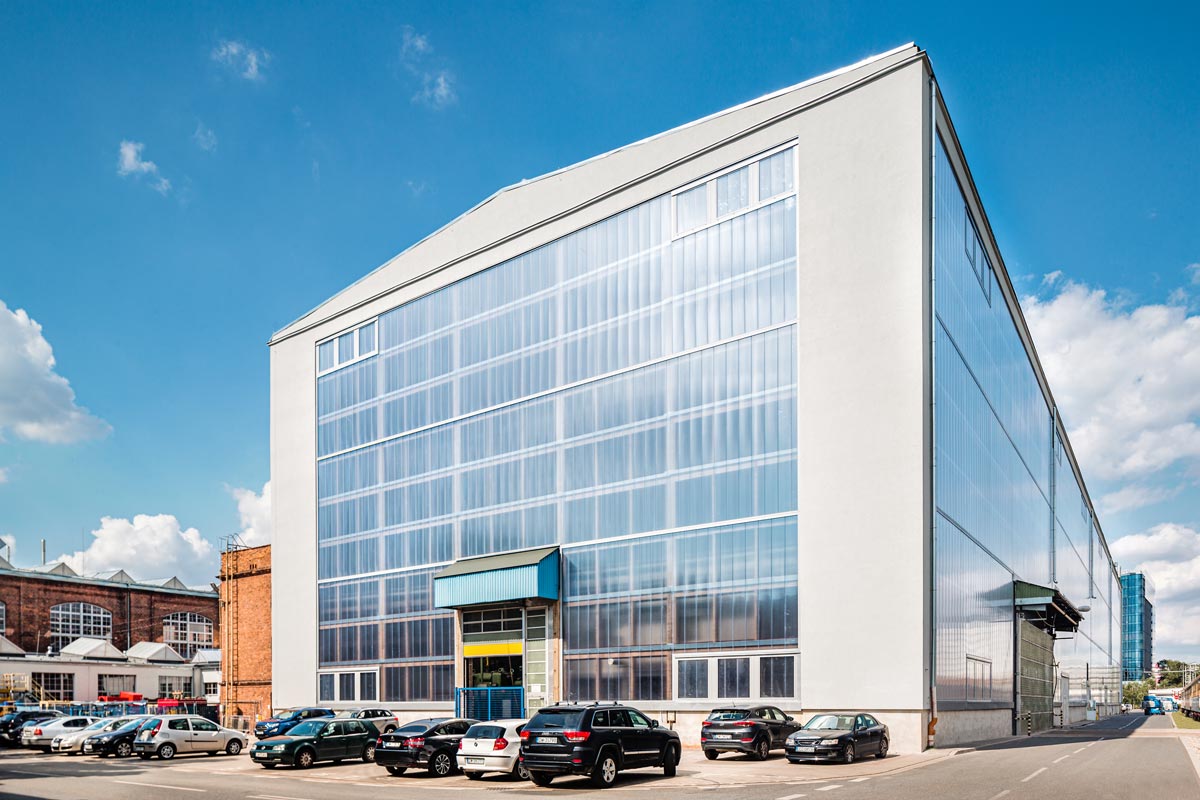
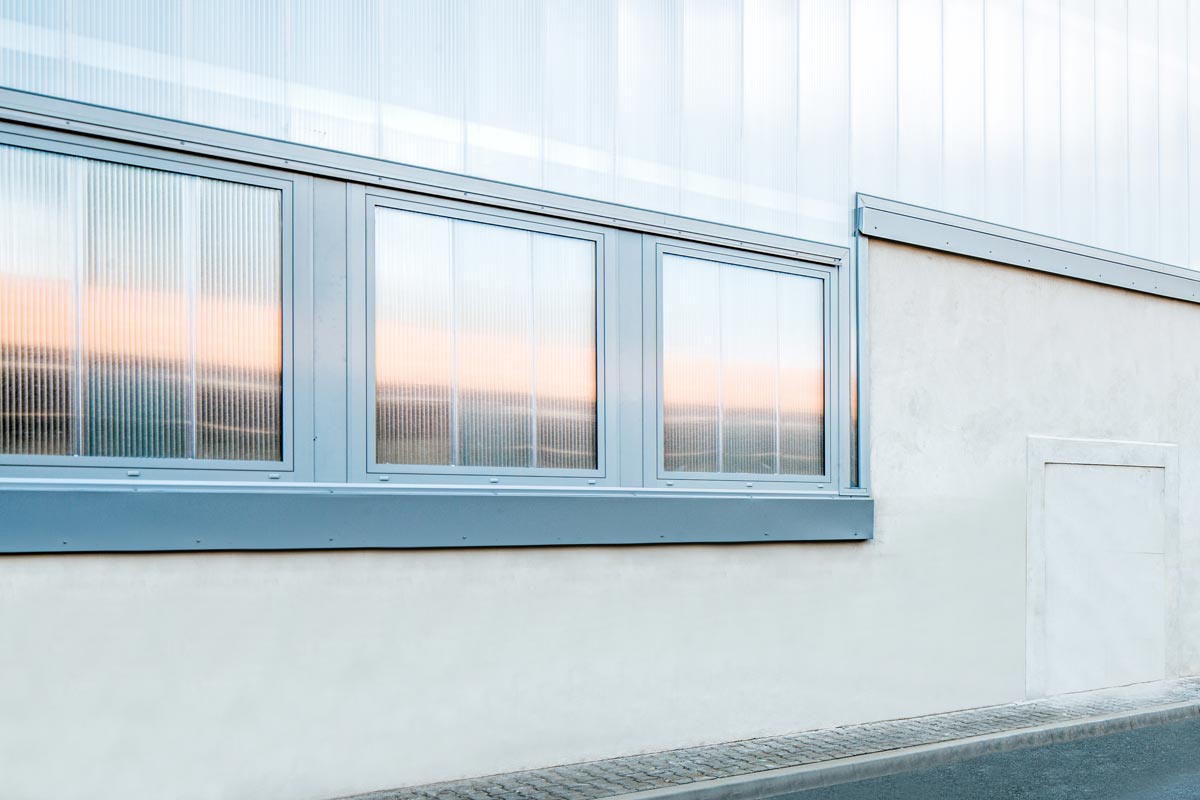
Ventilation windows
The facade was equipped with 20 ventilation windows measuring 1,200 mm x 1,200 mm. Similar to the facade, these windows were filled with ALUCO PANEL AP50 polycarbonate panels. The windows are operated by electric actuators with a stroke of 350 mm, controlled from the building level via the ventilation control panel.
Dozamel Case Study
Download PDF
Download the full version of the "Dozamel Case Study" article as a PDF file to your device.
Completion of the Project
Part III
The project was completed according to the work schedule. The upgraded buildings have certainly improved visually; the new skylights and facades have made the heritage building look much more appealing.
6,860 M²
OF SKYLIGHTS
5,000 M²
OF POLYCARBONATE PANELS
500 %
BETTER THERMAL PERFORMANCE
200 %
MORE DAYLIGHT
More daylight
However, the most crucial aspect was the fundamental improvement of the two primary functions: translucency and thermal performance. Even on cloudy days, the Dozamel building no longer requires electric lighting. The polycarbonate panels chosen as the filling for the skylights provide an optimal means of admitting daylight into the building, while also ensuring uniform scattering of light on days with intense sunlight.
Improvement of thermal performance
The primary objective of the thermal insulation works was to enhance the thermal performance of the building, and this aspect will be discussed in the project summary. The goal of thermal insulation is to minimize the heat transfer coefficient as much as possible to decrease the required heating (or cooling) costs. This objective has been successfully achieved. Nothing can better illustrate the success of the project than hard numbers. Therefore, the simulation below depicts the indicative energy savings generated by the upgrade of the skylights in building B1.
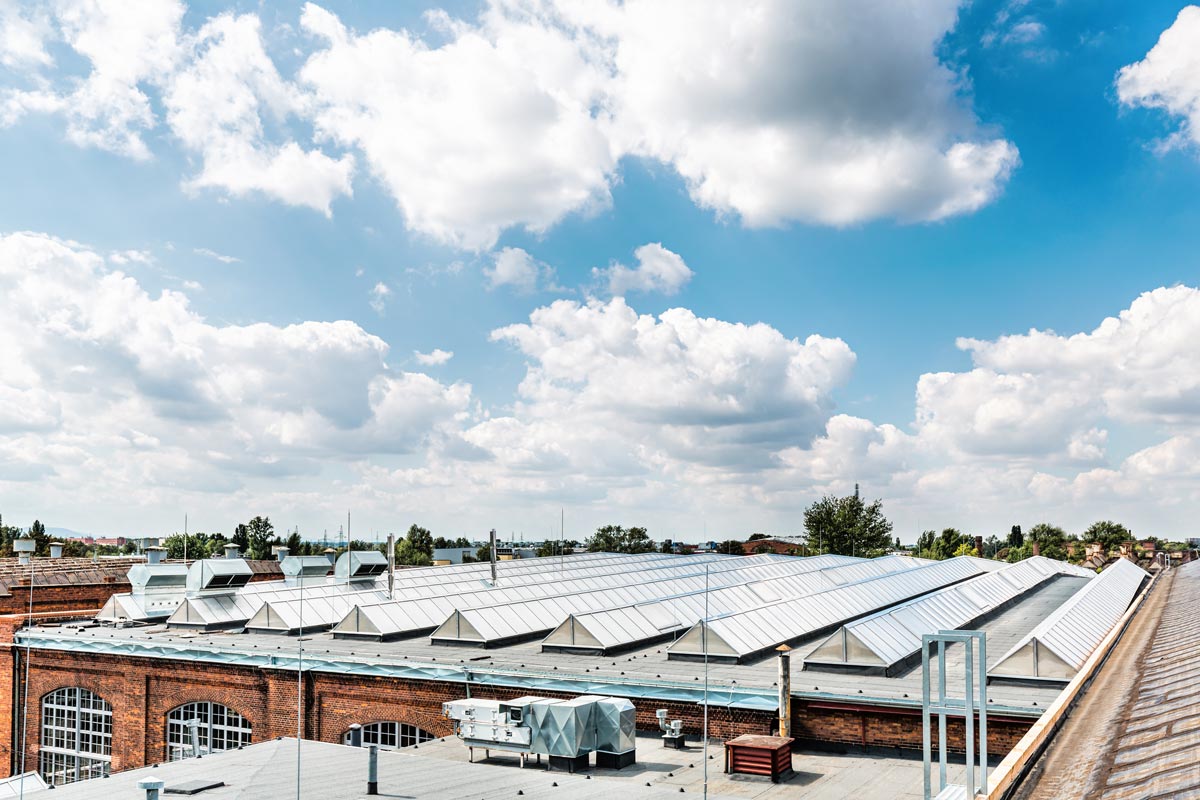
Simulation of savings
According to the DIN 4701 standard, a reduction of the heat transfer coefficient [U] by 0.1 W/m²K saves 0.9–1.3 litres of fuel oil or 1.0–1.5 m³ of natural gas per square metre of glazing. The calculations below illustrate the potential savings per square metre of glazed area for different reductions of the heat transfer coefficient of individual panes and polycarbonate panel units.
Glazing performance before the upgrade:
- 4 mm, single glazing,
- U: 5,9 W/m²K.
Glazing performance after the upgrade:
- filling with a polycarbonate panel unit,
- U: 1,1 W/m²K.
CALCULATIONS OF HEAT LOSS
Heat loss Q (kW) = area (m²) x U (W/m² K) x At temperature difference (K)
At Temperature difference refers to the temperature variance between indoor and outdoor air. If the production building is heated to 15°C, the heat collected under the roof is approximately 35°C, depending on the height of the building. With an outdoor temperature of 0°C, the temperature difference (At) is 35°C, equivalent to 35 Kelvin (K).
The total area of the roof skylights replaced on the roof of the B1 building of DOZAMEL was 6,860 m².
Heat loss for single glazing (before the upgrade):
Q = 6,860.0 m² x 5.9 W/m²K x 35°C = 1,416,600 W = 1,416.6 kW
Heat loss for a polycarbonate panel unit (after the upgrade):
Q = 6,860.0 m² x 1.1 W/m² K x 35°C = 264,100 W = 264.1 kW
The difference between the two values shows the change in heat losses as a result of the thermal modernization:
1,416.6 kW – 264.1 kW = 1,152.5 kW
Calculation of heat difference during the year:
1,152.5 kW x 24 h x 220 heating days = 6,085,200 kWh
Final estimate of savings
Lower calorific value for:
- natural gas – approx. 9.06 kWh/m³,
- fuel oil – approx. 10.05 kWh/l.
Savings on fuel oil:
6,085,200 kWh – 10.05 kWh/l = 605,500 l of fuel oil x PLN 0.80/kWh = PLN 484,400.00
Savings on natural gas:
6,085,200 kWh – 9.06 kWh/m³ = 671,700 m³ of natural gas x PLN 0.55/kWh = PLN 369,400.00
The calculations are based on the following fuel prices (price level on 10/2023):
- fuel oil: PLN 0.80/kWh,
- natural gas: 0,55zł/kWh.
NOTE: The estimate does not include the savings on the costs of electricity required for the proper lighting of the building!
Explanations for the calculations
The heat transfer coefficient, usually referred to as U, is a measure of the ability of a material or structure to transfer heat. The lower the coefficient, the better the protection against heat loss and heat gains from the outside. This is crucial for evaluating the insulating performance of buildings – the lower the heat transfer coefficient, the smaller the heat losses through walls, windows, or roofs. The coefficient is measured in W/m²K, i.e., in watts per square meter per kelvin.
See the difference
The photographs below depict the effects of our work. We have juxtaposed similar photos taken before the upgrade of the roof skylights and the facade with those taken after the completion of all tasks. It is immediately evident that, in addition to the enhancement of numerous technical specifications, the building has also become much more visually appealing.
Hint: Use the slider in the middle of the photograph to switch between the “before” and “after” views.
Thermal modernization of skylights
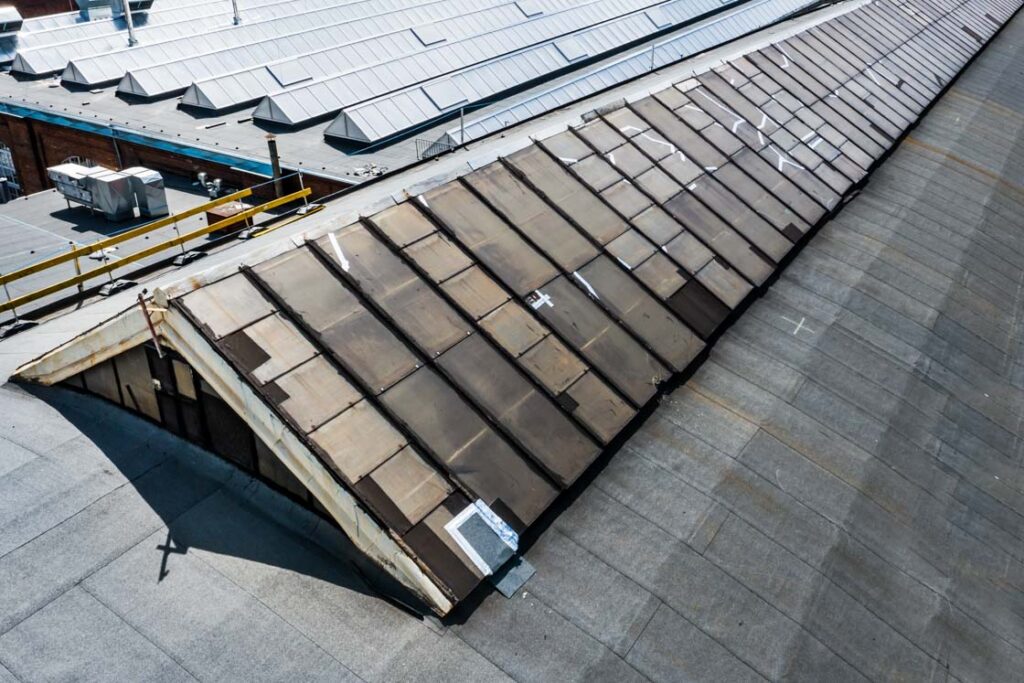
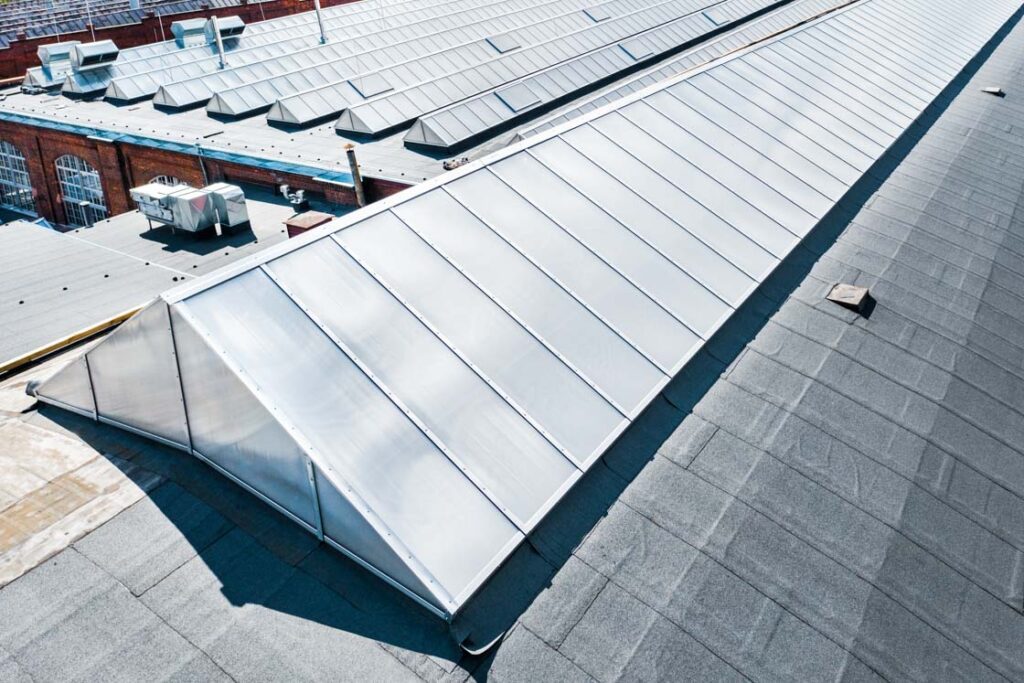
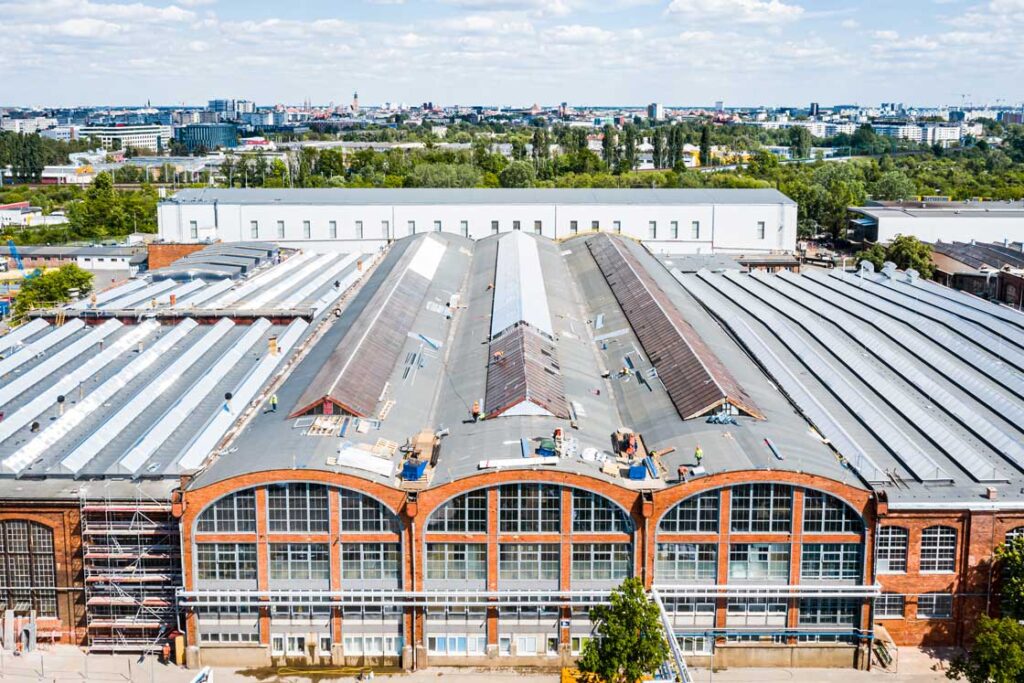
Before the modernization
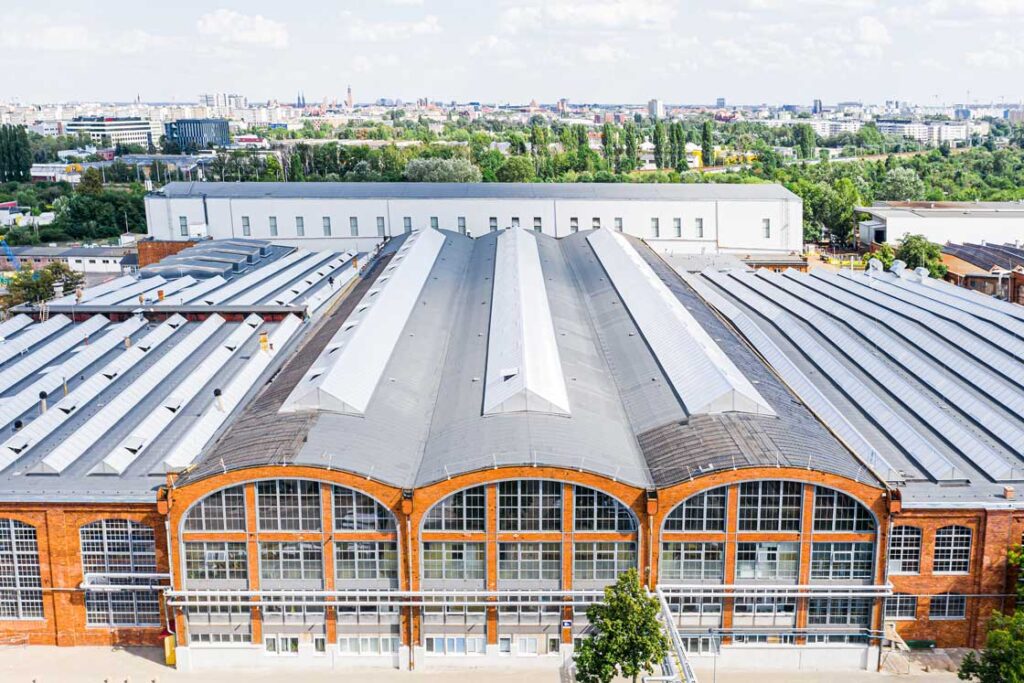
After the modernization
Daylight access
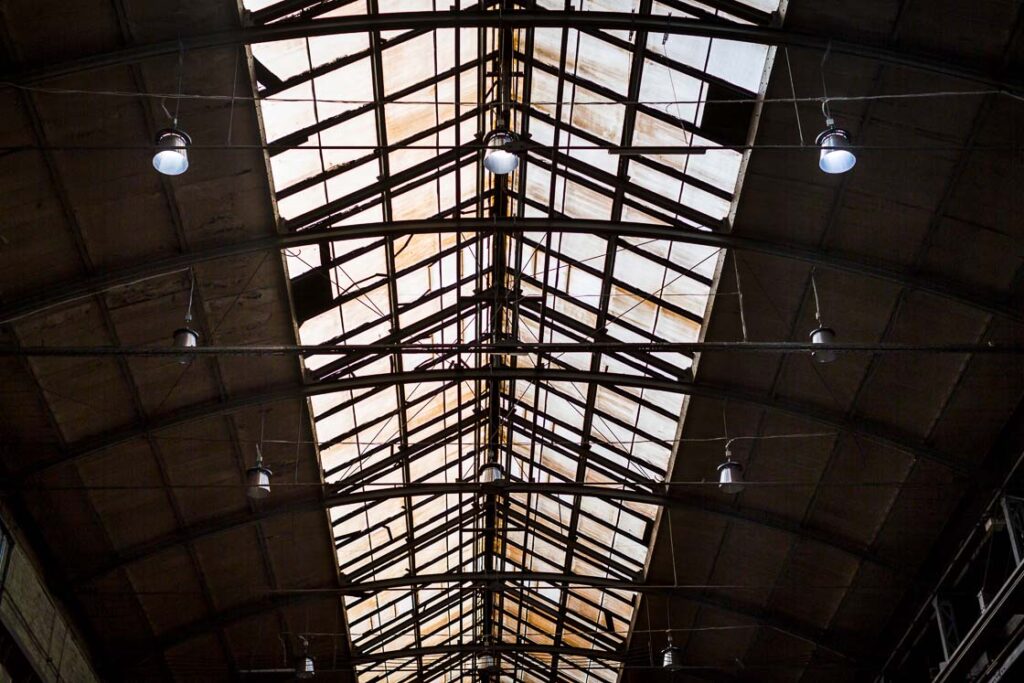
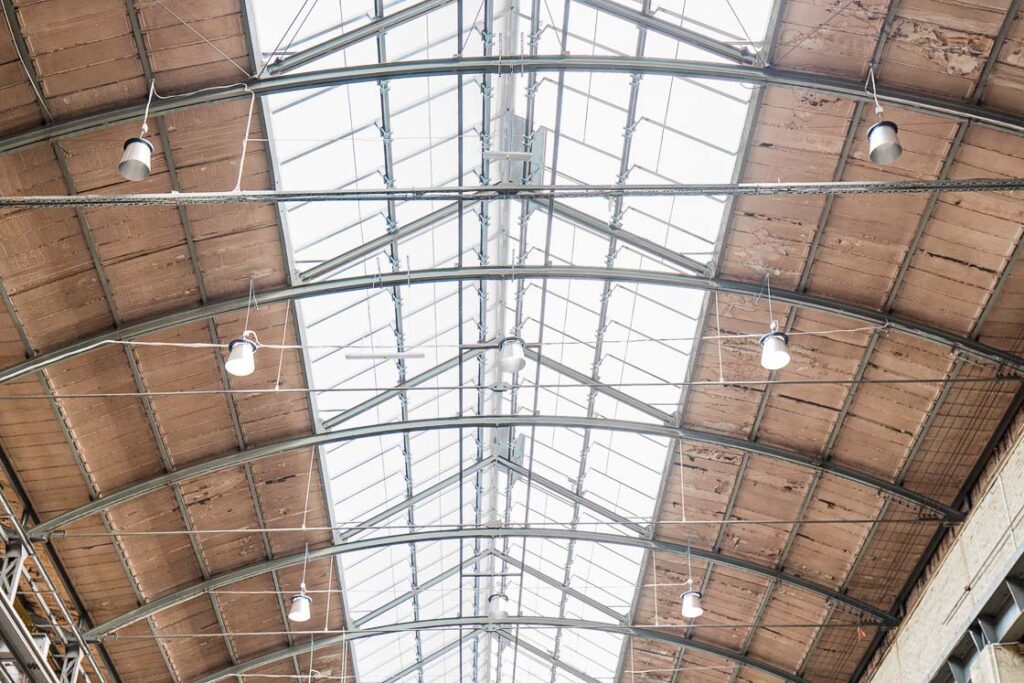
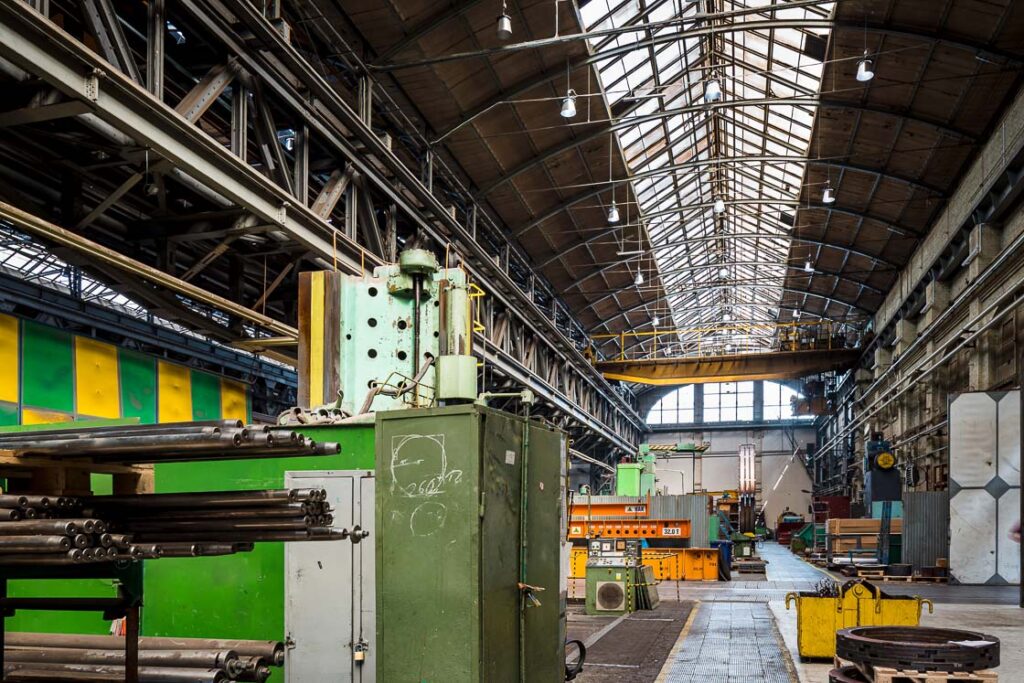
Before the modernization
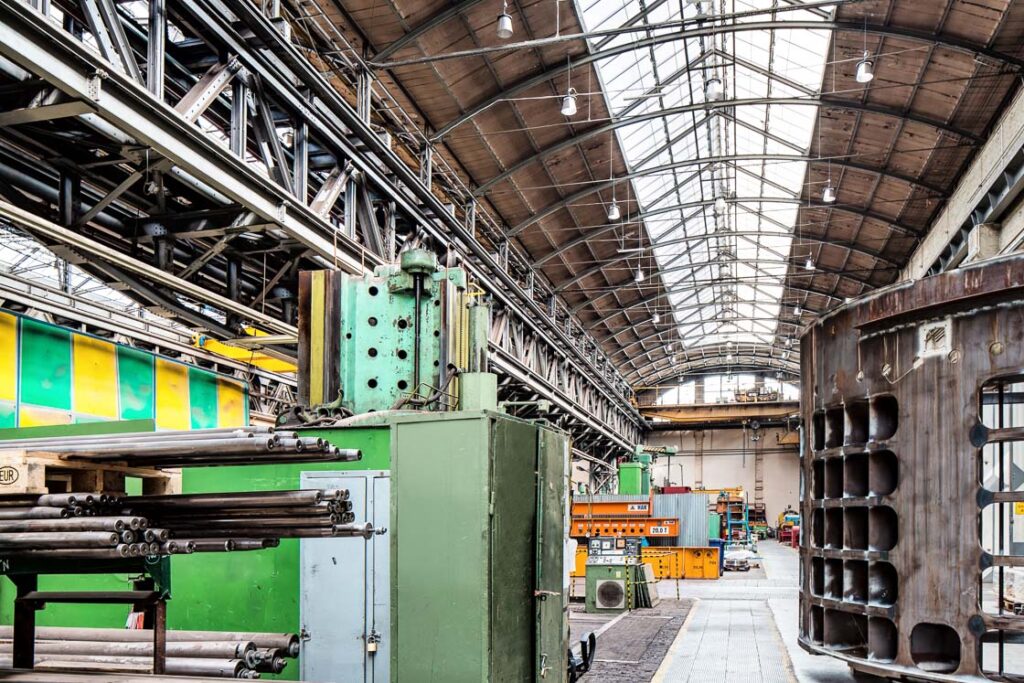
After the modernization
Thermal modernization of the facade
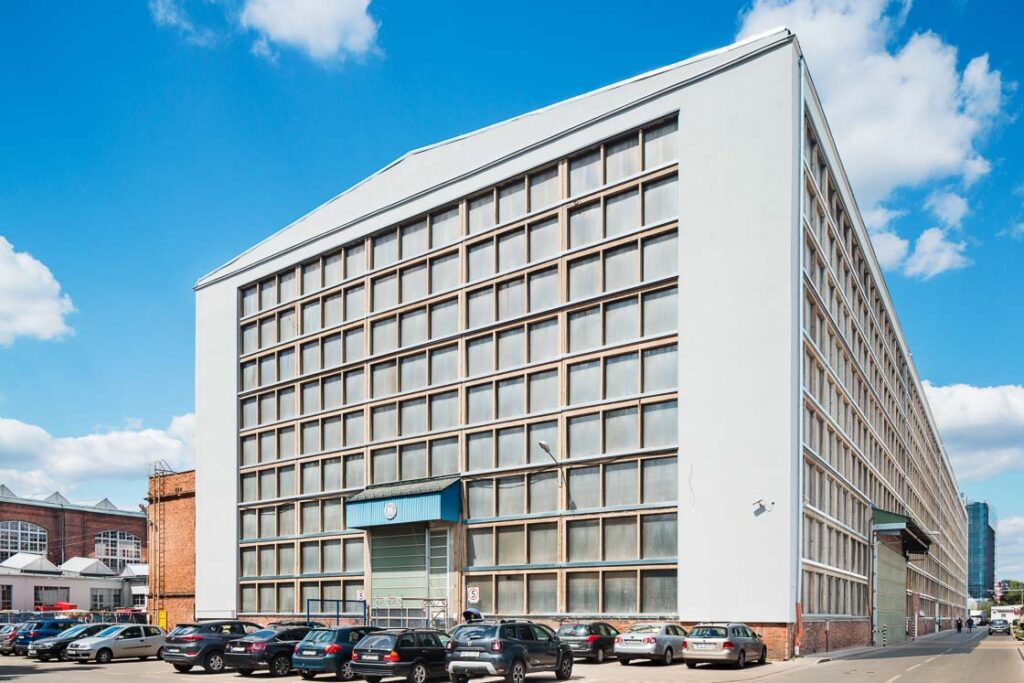
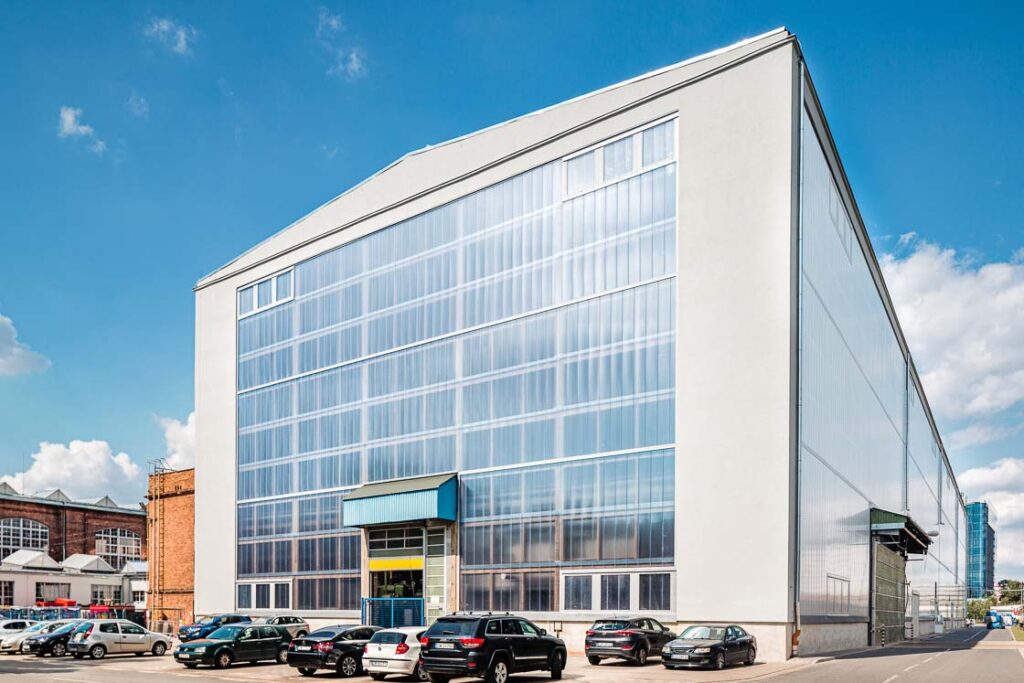
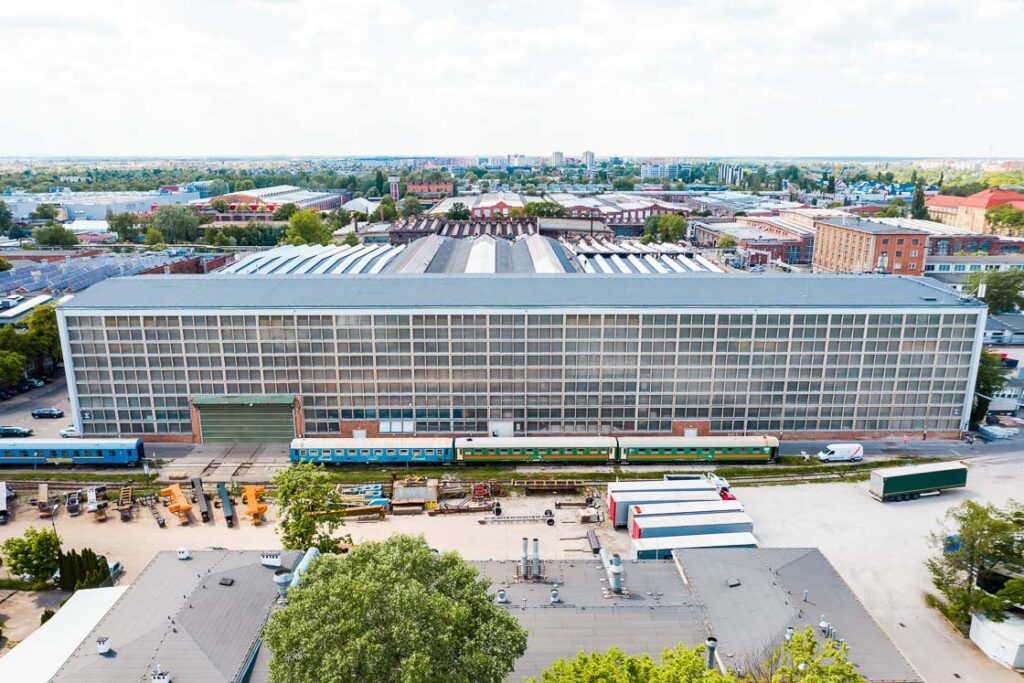
Before the modernization
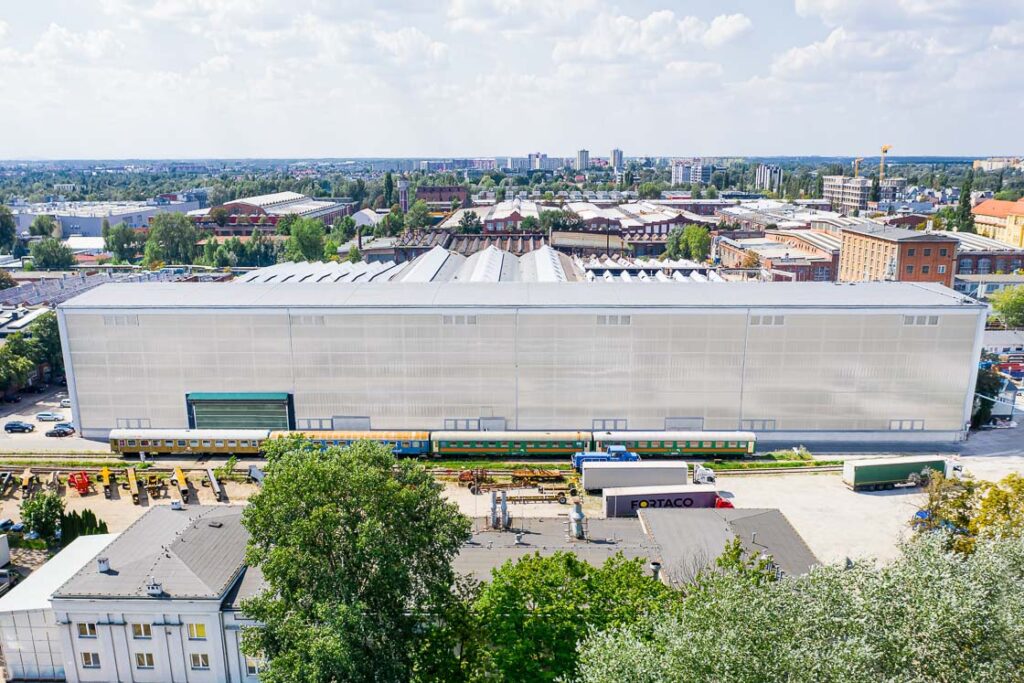
After the modernization
Dozamel Case Study
Download PDF
Download the full version of the "Dozamel Case Study" article as a PDF file to your device.
See More
dozamel
The photos presented in this article constitute only a portion of the extensive photographic documentation for the entire project. In our portfolio, we have compiled a complete gallery of photographs, categorized into the thermal modernization of the roof skylights and the facade.
About us
Aluco System
Aluco System has been operating in the market since 1997, specializing in architectural solutions for the industry. Our mission is to assist our customers in maximizing the benefits of natural lighting.
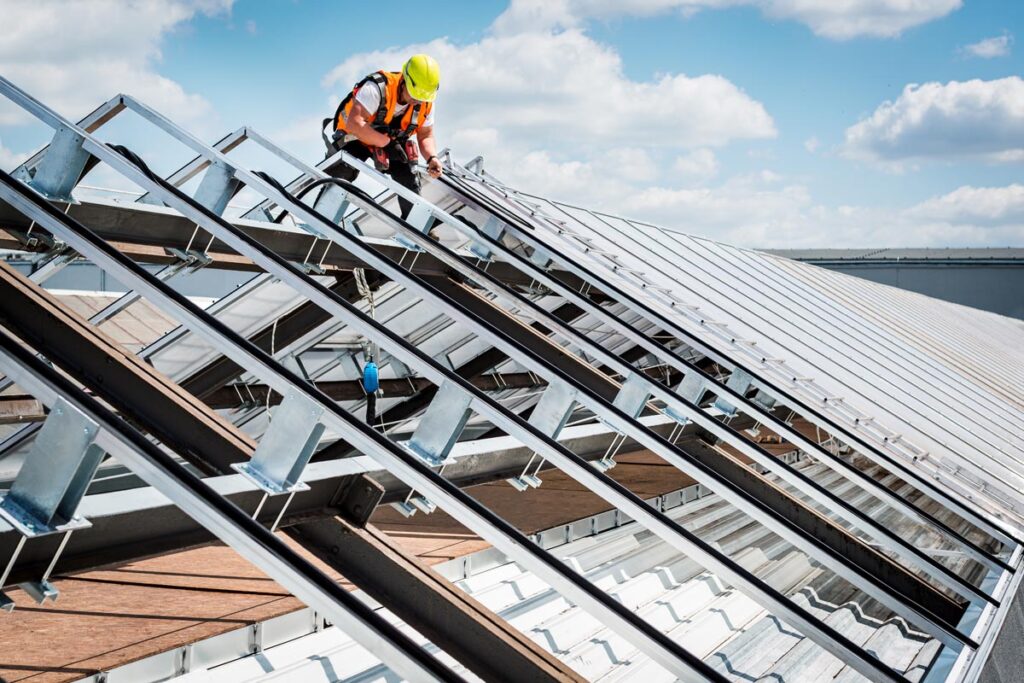
We manufacture and deliver roof skylights, facades, smoke control and ventilation systems, glass aluminum joinery, and fire-rated joinery. Additionally, we undertake comprehensive projects related to the thermal modernization of skylights and facades.
We continually develop more advanced and energy-efficient products without compromising on quality and safety. We are a 100% Polish company. With over 25 years of experience and 750,000 m² of installed roof skylights, we are one of the most recognizable brands in Poland.